The comparative study of the ductile iron casting process and other metal casting techniques involves examining the differences in materials, processes, properties, applications, and limitations. Key metal casting processes to compare include gray iron casting, steel casting, aluminum casting, and die casting. Let’s delve into each:
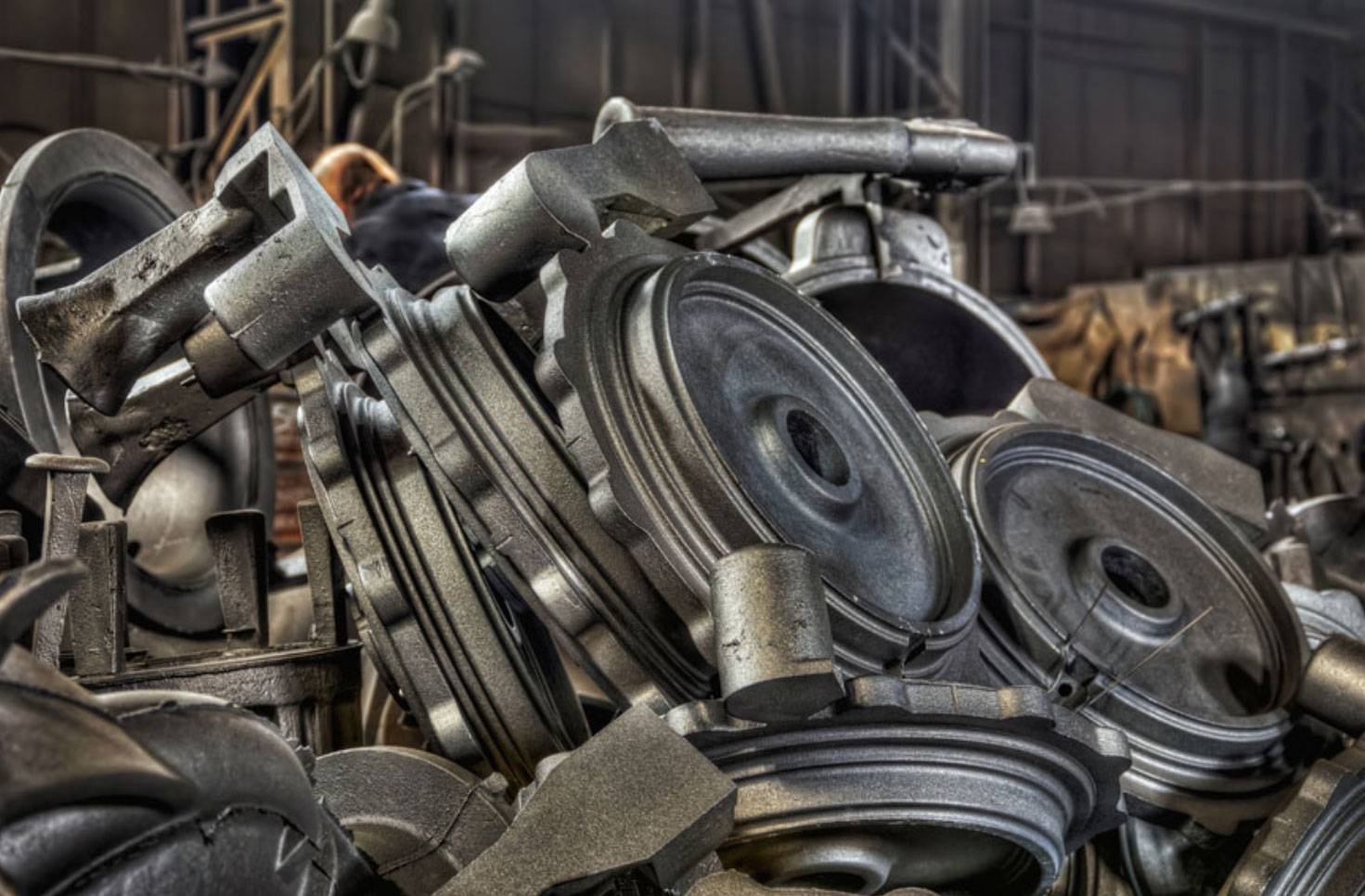
1. Ductile Iron Casting vs. Gray Iron Casting
- Material Composition: Ductile iron contains spheroidal graphite, while gray iron has flake graphite.
- Mechanical Properties: Ductile iron has higher tensile strength and ductility compared to gray iron, which is more brittle.
- Applications: Ductile iron is preferred for parts requiring high strength and toughness, while gray iron is often used in applications where vibration damping is important, like engine blocks.
- Cost: Ductile iron can be more expensive due to the additional treatment for graphite nodulization.
2. Ductile Iron Casting vs. Steel Casting
- Material Properties: Steel castings are known for their high strength, especially under tensile stress, but are less ductile compared to ductile iron.
- Weight and Cost: Ductile iron generally provides a better strength-to-weight ratio and is usually more cost-effective than steel castings.
- Weldability: Steel castings offer superior weldability compared to ductile iron.
- Applications: Steel is often chosen for critical high-strength applications in industries like aerospace, whereas ductile iron finds more use in automotive and infrastructure.
3. Ductile Iron Casting vs. Aluminum Casting
- Material Characteristics: Aluminum castings are significantly lighter, making them ideal for applications where weight is a critical factor.
- Corrosion Resistance: Aluminum offers better corrosion resistance than ductile iron.
- Melting Point: Aluminum has a much lower melting point, which can affect the choice of casting process and energy consumption.
- Applications: Aluminum castings are widely used in the automotive and aerospace industries for lightweight components, whereas ductile iron is used for heavier, load-bearing parts.
4. Ductile Iron Casting vs. Die Casting
- Process: Die casting, commonly used with metals like aluminum and zinc, involves forcing molten metal into molds under high pressure.
- Dimensional Accuracy and Surface Finish: Die casting generally achieves higher dimensional accuracy and a smoother surface finish than ductile iron casting.
- Production Speed: Die casting is suited for high-volume production due to faster cycle times.
- Strength: While die castings are strong, ductile iron typically offers superior tensile strength and durability.
Common Factors Across Different Casting Processes
- Design Flexibility: Most casting processes offer good design flexibility, allowing for complex shapes and intricate details.
- Tooling and Equipment: The choice of casting technique can depend on the available tooling and equipment, as well as the desired properties of the final product.
- Economic Considerations: Cost-effectiveness is a key consideration, which includes material costs, production scale, and energy consumption.
Conclusion
Each casting process has its own set of advantages and is suited to specific applications based on material properties, cost, strength requirements, weight considerations, and production volume. The choice between ductile iron casting and other techniques depends on the specific requirements of the application, including mechanical properties, cost constraints, and production capabilities.