Casting coating is a commonly used auxiliary material in casting production. It is a physical suspension dispersion system in colloidal state. It can be uniformly coated on the surface of the mold or core during the casting process, and contact with high-temperature molten metal to form a protective layer to prevent casting defects such as sand sticking and sintering, and improve the surface quality of the casting. In recent years, casting coating technology has developed rapidly, the performance of coating has been continuously improved, the function has been continuously expanded, and the variety of coating has become more and more abundant. The key to obtain high quality castings is the correct choice of coating and the reasonable application of coating.
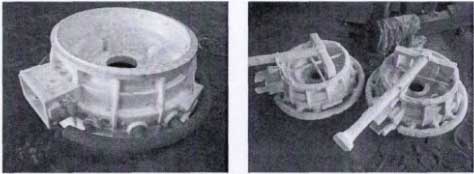
Casting coating is usually composed of refractory aggregate, carrier liquid, suspending agent, binder and additives.
(1) Refractory aggregate
The refractory aggregate is the basis of the coating. It is suspended in the coating with the help of a suspending agent and uniformly coated on the working surface of the mold (core). After the carrier liquid volatilizes, the binder makes the powder dry and form a dense coating to protect the working surface. The commonly used refractory aggregates for coating steel castings include zircon powder, quartz powder, brown corundum, bauxite, magnesia powder, olivine powder, mullite powder, etc; Commonly used refractory aggregates for coatings for cast iron castings include flake graphite, earthy graphite, quartz powder, bauxite, mullite powder, pearlescent powder, etc; Common refractory aggregates used in coatings for non-ferrous alloy parts include graphite, talc powder, etc.
(2) Carrier liquid
The carrier liquid is mainly divided into water and organic solvents. The commonly used organic solvents are methanol, ethanol and isopropanol. The coating with water as the carrier is called water-based coating, and the coating with alcohol as the carrier is called alcohol based coating. The advantages of water base are: good suspension, safe and reliable, low price; The disadvantage is that it needs to be dried. The alcohol based coating can be cured after ignition, eliminating the drying process, but its price is higher.
(3) Suspending agent
The function of the suspending agent is to prevent the precipitation of the refractory aggregate and the excessive penetration of the carrier liquid into the sand mold (core). The commonly used suspending agents for water-based coatings include bentonite, attapulgite clay, sepiolite, carboxymethyl cellulose, sodium alginate and polyacrylamide. Commonly used suspending agents for alcohol based coatings include organic bentonite (initiated with xylene or solvent gasoline), sodium bentonite, lithium bentonite, attapulgite clay, sepiolite, rectorite and polyvinyl butyral.
(4) Binder
In order to improve the adhesion of the coating, enhance the adhesion of the coating and the strength of the coating, the refractory powder particles are adhered to the surface of the cavity, and the binder should be added during the production of the coating. The commonly used binders for water-based coatings include clay, bentonite, water glass, silica sol, phosphate, sulfate, polyaluminum chloride, syrup, pulp waste liquid, dextrin, starch polyvinyl alcohol (PVA), polyvinyl acetate lotion, water-soluble phenolic resin, etc; The commonly used binders for alcohol based coatings include organic bentonite phenolic resin, ethyl silicate, polyvinyl acetal (PVB), rosin, paint chips, etc. PVB, rosin, paint flakes, etc. are thermoplastic low-temperature binders for alcohol based coatings. They become liquid when heated and are not resistant to metal liquid scouring. They are not suitable for large pieces. Thermosetting phenolic resin and linear phenolic resin added with Urotropine are no longer liquefied, so they can be used to produce large pieces; Ethyl silicate can be used as a high-temperature binder for coatings, which must be hydrolyzed in advance.
(5) Additions
The additives mainly include surfactant, defoamer, etc. The function of surfactant is to improve the wettability and permeability of coating to the surface of mold and core. Commonly used surfactants include op-15 (polyethylene alkyl alcohol ether, commonly known as lubeling), T-80 (also known as Tween 80), JFC, etc; Common defoamers include n-butanol, n-octanol, saf, spa-202, etc; Common preservatives include thymol (also known as thymol), anaerobic phenol (also known as pentachlorophenol), sodium pentachlorophenol, etc.