After the shape of cast steel joint is determined, the next step is to determine the modeling method. Because of the complex space shape of the cast steel joint and the high requirement of the material, the choice of the molding technology is very important.
At present, the common casting methods for cast steel joints are sand casting and EPC. Sand casting is the most basic and widely used casting method in foundry production. Application and cast steel joint production, the main casting mold is wood mold manufacturing. However, there are many disadvantages in wood mold manufacturing:
(1) The spatial structure of cast steel joint is complex, so it is very difficult to select parting surface and draft;
(2) Cast steel joints must be synchronized with the construction progress of the building, so the construction period is relatively short. The cost of wood mold is relatively high, and the manufacturing time is long.
(3) Because cast steel joints are designed according to specific buildings, most of them are unique. Each pair of wood mould is only used once, which leads to a great waste and increases the production cost of cast steel joint.
The conventional EPC process adopts solid mold casting, which uses the high temperature of molten metal to vaporized the foam, thus making the metal replace the position of the foam to obtain the required castings. However, the material of cast steel joints is low alloy steel (C:0.17%-0.23%) which is relatively strict in controlling the elements. If solid pouring is done, the surface of the cast steel nodes will be carburized and vaporized, which will deteriorate their service performance. In addition, due to the large volume of the cast steel joints, there are certain requirements for the strength of the foam in order to prevent the deformation of the foam pattern. This will require a higher degree of compaction of the foam, so if the conventional EPC process is used, the situation of carbon carburization will be even more serious.
Based on the above considerations, the composite casting process is adopted for the cast steel joint. The lost foam foam model has the advantages of high degree of freedom, easy processing and low cost. Foam is used to make the node pattern and make use of organic water glass sand molding. After the molding is finished, after the sand mold is hardened, the foam will be removed through the way of destruction, so that the cavity can be formed. In the aspect of pattern making, due to the large size and complex shape of the pattern, if the pattern is completely modeled by the EPC pattern, then the pattern making is quite difficult, especially the internal cavity making process of the node is particularly tedious. Greatly affect the progress of production, and the foam strength is relatively weak in the thin-walled parts, it is easy to deform in the molding process, affecting the dimensional accuracy of the casting. Therefore, only the vanishing mode is used to make the outer contour of the node. The inner cavity is formed by sand core.
The sand core is made of wood mold, which has mature technology and high precision. When molding, first put the foam pattern into the sand box. After the sand mold is hardened, the foam will be removed by the way of destruction, and the sand core can be put into the cavity, and then the coating and the closing operation can be carried out. This completes the whole node modeling process. The composite process not only uses the high degree of freedom design of EPC, but also avoids the defects of surface carburization.
Taking the modeling process of the back peak node as an example, the specific process is as follows: firstly, the outer contour of the cast steel node is produced by using manual foam cutting assisted numerical control machining (without cavity characteristics). Then the mold is modeled with sodium silicate sand, and after the hardening of the sand mold is completed, the foam is removed by means of destruction. Then you can lower the core.
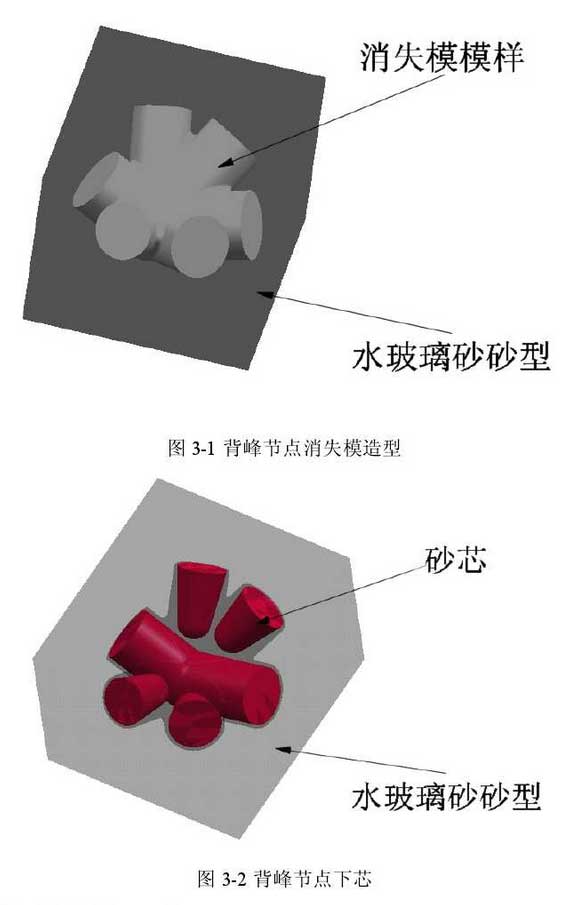
The actual core lowering process is as shown in the figure:
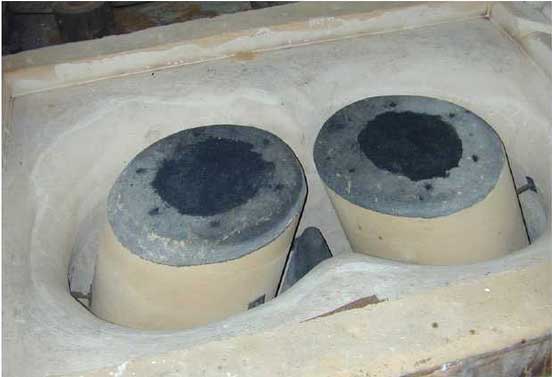