Ductile cast iron is widely used in various industries, including automotive, construction, and water treatment. Despite its strengths, one of the critical factors affecting the long-term performance of ductile cast iron is its corrosion resistance, especially when exposed to aggressive environments. This article delves into the corrosion resistance of ductile cast iron, the challenges posed by different environments, and effective strategies to enhance its durability.
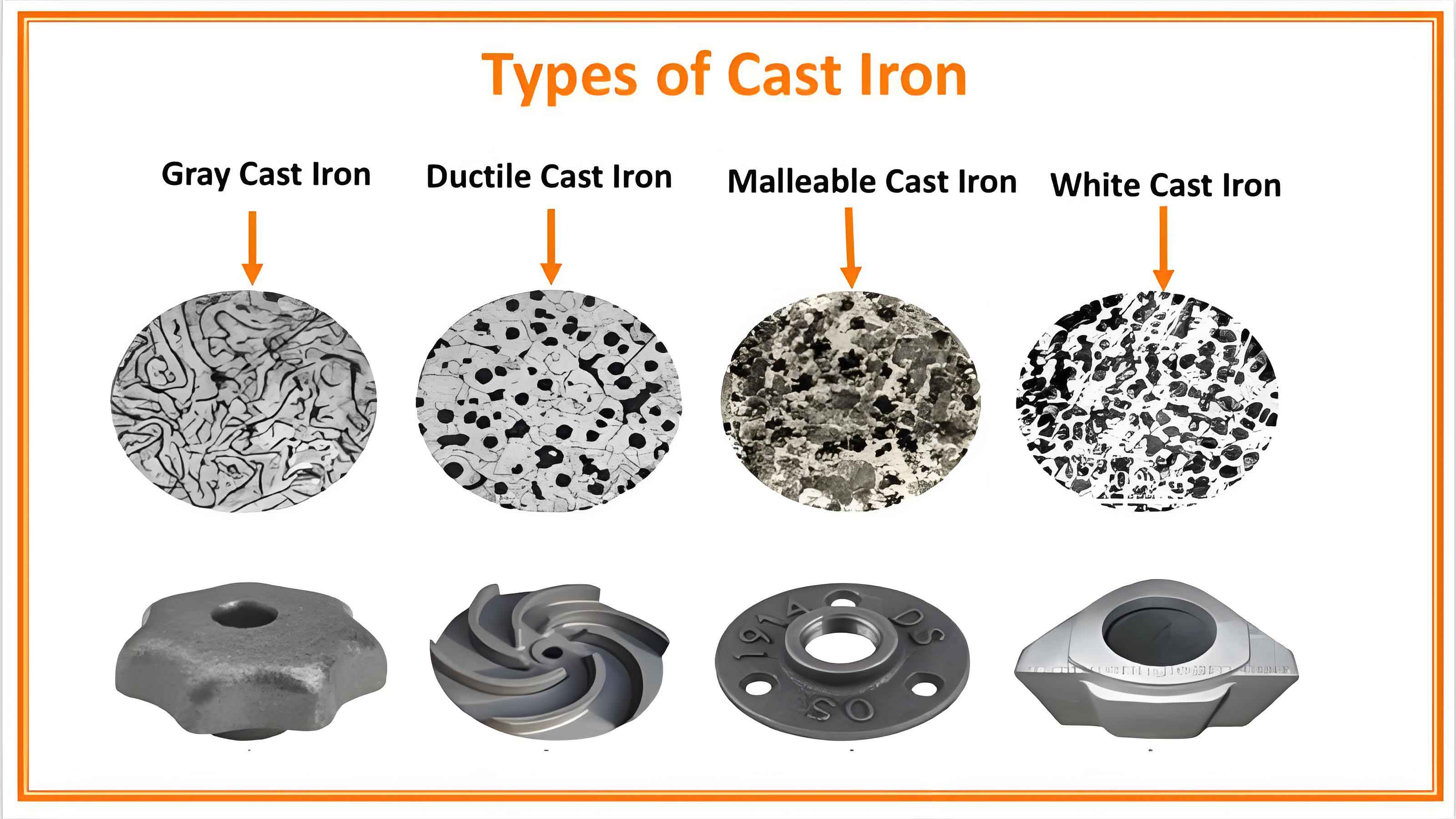
Introduction
Corrosion is a natural process that deteriorates materials, particularly metals, due to chemical reactions with their environment. For ductile cast iron, corrosion resistance is a crucial property that determines its suitability for applications in harsh conditions. This article examines the factors influencing the corrosion behavior of ductile cast iron and explores methods to mitigate corrosion in aggressive environments.
Factors Affecting Corrosion Resistance
Several factors influence the corrosion resistance of ductile cast iron, including its microstructure, composition, and the nature of the environment.
Microstructure
The microstructure of ductile cast iron, characterized by spherical graphite nodules within a metallic matrix, plays a significant role in its corrosion behavior. The presence of these nodules reduces the likelihood of crack propagation, which can otherwise accelerate corrosion.
Composition
The alloying elements in ductile cast iron, such as silicon, manganese, and phosphorus, impact its corrosion resistance. For instance, silicon enhances corrosion resistance by forming a protective silicon dioxide layer on the surface.
Table 1: Influence of Alloying Elements on Corrosion Resistance
Element | Effect on Corrosion Resistance |
---|---|
Silicon | Forms a protective oxide layer |
Manganese | Can reduce corrosion resistance at high levels |
Phosphorus | Increases brittleness, reducing corrosion resistance |
Environment
The environment in which ductile cast iron is used significantly affects its corrosion resistance. Factors such as pH, chloride concentration, temperature, and the presence of corrosive agents (e.g., sulfuric acid, seawater) can accelerate the corrosion process.
Table 2: Environmental Factors Affecting Corrosion Resistance
Environmental Factor | Effect on Corrosion |
---|---|
pH | Low pH (acidic conditions) accelerates corrosion |
Chloride Ions | High chloride concentration increases corrosion |
Temperature | Higher temperatures generally increase corrosion rates |
Corrosive Agents | Presence of acids, salts, and gases (e.g., SO2) enhances corrosion |
Corrosion Mechanisms
Ductile cast iron is susceptible to various types of corrosion, including uniform corrosion, pitting corrosion, and galvanic corrosion.
Uniform Corrosion
Uniform corrosion occurs evenly across the surface of ductile cast iron, leading to a gradual reduction in thickness. This type of corrosion is common in acidic environments.
Pitting Corrosion
Pitting corrosion is localized and results in small, deep pits on the surface. This form of corrosion is particularly dangerous as it can lead to structural failure. Chloride ions are often responsible for pitting corrosion.
Galvanic Corrosion
Galvanic corrosion occurs when ductile cast iron is in contact with a more noble metal in the presence of an electrolyte. The electrochemical potential difference between the two metals causes the less noble metal (ductile cast iron) to corrode preferentially.
Enhancing Corrosion Resistance
Several strategies can enhance the corrosion resistance of ductile cast iron, making it more suitable for use in aggressive environments.
Alloying
Adding specific alloying elements can improve the corrosion resistance of ductile cast iron. For instance, adding chromium and nickel can enhance resistance to oxidizing environments.
Table 3: Effect of Alloying Elements on Corrosion Resistance Enhancement
Alloying Element | Effect on Corrosion Resistance |
---|---|
Chromium | Improves resistance to oxidation and high-temperature corrosion |
Nickel | Enhances resistance to acid and chloride environments |
Molybdenum | Increases resistance to pitting and crevice corrosion |
Surface Coatings
Applying protective coatings is an effective way to prevent corrosion. Common coatings include epoxy resins, zinc coatings (galvanization), and ceramic coatings.
Cathodic Protection
Cathodic protection involves connecting the ductile cast iron to a more easily corroded “sacrificial” metal. This method is widely used in pipelines and marine environments.
Environmental Control
Controlling the environmental conditions, such as reducing the exposure to corrosive agents and maintaining a neutral pH, can significantly mitigate corrosion.
Regular Maintenance and Monitoring
Implementing regular maintenance schedules and monitoring for early signs of corrosion can help address issues before they become severe.
Case Studies
Case Study 1: Water Treatment Plants
In water treatment plants, ductile cast iron pipes are exposed to various chemicals and fluctuating pH levels. By applying epoxy coatings and using cathodic protection, the lifespan of these pipes has been significantly extended, reducing maintenance costs and downtime.
Case Study 2: Marine Applications
Ductile cast iron components used in marine environments face aggressive corrosion due to saltwater exposure. The application of zinc coatings and the addition of nickel to the alloy composition have proven effective in enhancing corrosion resistance, ensuring reliable performance in these harsh conditions.
Conclusion
The corrosion resistance of ductile cast iron in aggressive environments is influenced by its microstructure, composition, and environmental factors. Understanding these factors and implementing appropriate strategies, such as alloying, surface coatings, cathodic protection, and environmental control, can significantly enhance the durability and performance of ductile cast iron components. By adopting these solutions, industries can extend the service life of their infrastructure and reduce maintenance costs, ensuring sustainable and reliable operations in challenging environments.