This article focuses on the rheological squeeze casting process of the Al-11Zn-1.8Mg-0.9Cu-0.15Zr-0.15Sc casting aluminum alloy. Through a combination of numerical simulation and experimental verification, the effects of process parameters such as melt temperature, mold temperature, and squeeze pressure on the casting quality were investigated. The results show that under the conditions of a melt temperature of 660°C, a mold temperature of 200°C, and a squeeze pressure of 75 MPa, the casting exhibits good performance with uniform composition, a grain size of 30 μm, a hardness of 180 HBW, a tensile strength of 535 MPa, and an elongation of 9%. This study provides important technical support for the engineering application of this alloy.
1. Introduction
1.1 Research and Development Status of Al-Zn-Mg-Cu Alloy
1.1.1 Introduction to Al-Zn-Mg-Cu Alloy
Aluminum alloys, as lightweight materials, are widely used in industrial fields. Among them, the Al-Zn-Mg-Cu alloy (7xxx series aluminum alloy) has attracted particular attention due to its excellent mechanical properties. As a high-strength aluminum alloy, the 7xxx series aluminum alloy exhibits unique advantages in aerospace, automotive, and defense industries. In the aerospace field, it is mainly used to manufacture aircraft structures, wings, fuselages, and engine parts. With the continuous upgrading of aircraft and the rapid development of the aviation industry, the demand for 7xxx series aluminum alloys is increasing year by year. In the automotive manufacturing field, due to the need for lightweight development, the Al-Zn-Mg-Cu alloy is widely used in automotive parts, such as engine housings and wheels. In the defense industry, it is mainly used to manufacture the structural components of rockets, missiles, and other military equipment. With the continuous upgrading of military equipment, the demand for Al-Zn-Mg-Cu alloys is also increasing. In general, due to its high hardness, high yield strength, and tensile strength, as well as excellent mechanical properties, the 7xxx series aluminum alloy exhibits stable and reliable performance in aerospace components, automotive parts, rocket and missile structural components, and other fields. In addition, it also has excellent corrosion resistance, good weldability, and heat treatment performance, which can meet the material performance requirements of different fields. With the continuous improvement of material performance requirements in various industries and the increasing demand for lightweight, high-strength, and corrosion-resistant characteristics, the demand and application scale of 7xxx series aluminum alloys are showing a rapid growth trend, and the application direction is gradually developing towards large and complex components, such as aircraft fuselages, automotive body structures, wheels and suspensions, ship hulls, cabins, and other large and complex structures. In recent years, China’s new energy vehicle industry has developed rapidly, and driving range is one of the important indicators to measure the performance of new energy vehicles. Relevant studies have shown that if the weight of a new energy vehicle body is reduced by 10 kg, its driving range can be increased by about 2.5 km. For every 10% reduction in the total weight of a vehicle, its steering force will be reduced by 6%, the braking distance will be reduced by 5%, the fuel consumption will be reduced by 6% – 8%, the acceleration time will be reduced by 8%, and the emissions will be reduced by 10%. At the same time, the service life of the tires will be increased by about 7%. At present, the proportion of aluminum alloys used in China’s automotive manufacturing industry is about 20% and is increasing. It is expected that by 2030, the mass reduction of vehicles may reach 35%. Therefore, the demand for large and complex 7xxx series aluminum alloy parts has great growth potential.
However, the current 7xxx series aluminum alloy structural parts are mainly formed by multiple processes such as casting into ingots, cogging forging, plastic deformation, heat treatment, and machining. This forming method has a low material utilization rate, a long processing time, and high costs, which limits the application of the Al-Zn-Mg-Cu alloy. If large and complex structural parts such as automobile bodies can be formed by integrated casting, a large amount of time and production costs can be saved. However, due to the high alloying degree of the Al-Zn-Mg-Cu alloy and relatively poor casting performance, defects such as shrinkage porosity, hot cracking, segregation, and coarse and uneven microstructure are prone to occur during the solidification process. It is difficult to meet the product design requirements by using the existing direct casting method to form high-strength deformed aluminum alloys. Therefore, the development of a short-process, low-cost casting technology for the Al-Zn-Mg-Cu alloy with performance reaching the forging level has important practical value.
1.1.2 Research Progress of Ultra-high Strength Cast Aluminum Alloy
Ultra-high strength aluminum alloys mainly refer to the Al-Zn-Mg-Cu alloys with better mechanical properties in the 7xxx series aluminum alloys. Since the United States developed the 7075 high-strength aluminum alloy in 1943, research on ultra-high strength aluminum alloys has entered a period of rapid development. Researchers have successively studied and improved the alloy composition and corresponding heat treatment process of ultra-high strength aluminum alloys, and their strength, plasticity, creep performance, and corrosion resistance have been greatly improved. In recent years, near-net-shape casting technology has become an important development direction of the 7xxx series aluminum alloys. However, the existing casting performance of the 7xxx series deformed aluminum alloys cannot meet the production requirements of near-net-shape casting technology. After in-depth research and exploration, the methods to improve the casting performance of the 7xxx series aluminum alloys mainly include two aspects: optimization of the casting forming method and optimization design of the alloy composition.
In terms of forming method optimization, the squeeze casting method is used to form ultra-high strength aluminum alloys. The aluminum alloy melt solidifies under high pressure, and the alloy melt completes the solidification and feeding process under pressure, which can effectively reduce the occurrence of defects such as shrinkage porosity inside the casting and obtain aluminum alloy castings with a more compact microstructure. During the squeeze casting process, the grain size of the alloy melt is finer and the microstructure is more uniform. Moreover, due to the continuous action of the squeeze pressure on the alloy melt, the surface of the alloy melt is in good contact with the surface of the casting, and the outer surface contour of the casting is clear and the roughness is low, which can reduce the size difference between the casting and the final formed part and the machining allowance, thereby improving the utilization rate of the alloy material and reducing the production cost. On the basis of the squeeze casting forming process, the rheological squeeze casting method has been further studied and developed. Before squeeze casting, the alloy melt is homogenized, which can improve the uniformity of the composition and temperature fields of the metal melt and further refine the grains.
In terms of alloy composition optimization design, casting aluminum alloys with high casting performance are developed through composition optimization to solve the problem of poor casting performance of existing deformed aluminum alloys. In order to improve the comprehensive properties of the alloy, such as mechanical properties, damage tolerance, and hot cracking resistance, researchers have conducted a large number of studies on the role of alloying elements in the Al-Zn-Mg-Cu alloy. Studies have found that Zn and Mg elements play a major strengthening role in the Al-Zn-Mg-Cu alloy, and the Cu element also has a certain strengthening effect, but its main role is to improve the corrosion resistance of the material. The effects of adding Sc and Zr in the Al-Zn-Mg-Cu alloy are similar, which have a significant effect on inhibiting recrystallization and refining grains. When Sc, Zr, and other elements are added to the aluminum alloy, Al(Sc, Zr) phases will be formed during the solidification process, and the effect of inhibiting grain growth is more obvious.
Zn and Mg elements are the main alloying elements in the Al-Zn-Mg-Cu alloy system. When dissolved in the aluminum matrix, they can play a solid solution strengthening role. Studies have shown that for the Al-Zn-Mg-Cu alloy, the η phase, T phase, S phase, and MgZn₂ phase are the main precipitated phases, among which the MgZn₂ phase is the most important strengthening phase. The content and ratio of Zn and Mg have an important impact on the formation and volume fraction of the main strengthening phase MgZn₂. The ratio of Zn/Mg determines the type of precipitated phase in the Al-Zn-Mg-Cu alloy. It is generally believed that the T phase and η phase are precipitated in the eutectic layer, and the ratio of Zn/Mg has a significant impact on the formation of the eutectic layer. When the molar fraction ratio of Zn/Mg is greater than 2 (the mass fraction ratio is greater than 3.8), the η phase is the main strengthening phase; otherwise, it is the T phase. The solubility of the η phase and T phase in aluminum is related to temperature. When the temperature decreases, the solubility decreases sharply. The solubility of the MgZn₂ phase at the eutectic temperature is relatively high, which can reach 28%, and it decreases to 4% – 5% at room temperature, and the solid solution strengthening effect is significant. Without exceeding the allowable solid solubility range, increasing the mass percentage of Zn and Mg elements in the alloy melt can significantly increase the amount of the aging precipitated phase MgZn₂ in the alloy, thereby effectively improving the tensile and yield strengths of the alloy, but the ductility and corrosion resistance of the alloy will be reduced. Wen Kai studied different Al-Zn-Mg-Cu alloys with a Zn/Mg ratio of 4.5 and found that the higher the alloying degree, the higher the content of the strengthening phase in the alloy, and the higher the hardness and strength of the alloy. However, adding a large amount of alloying elements such as Zn, Mg, and Cu not only improves the mechanical properties of the alloy but also makes the alloy brittle and produces microstructural defects, making it difficult to obtain near-net-shape structural parts with good mechanical properties. This defect is likely due to the high content of alloying elements, which reduces the fluidity of the alloy and thus its casting performance. Moreover, the higher the content of alloying elements, the more serious the impact on the solidification range, grain size, thermal conductivity, eutectic phase size and proportion, macrosegregation, and microsegregation of the alloy. Chen et al. studied the influence of different Zn element contents on the strength and other properties of ultra-high strength Al-Zn-Mg-Cu alloys and found that when the Zn content changes within the range of 9.0 wt.% – 11.0 wt.%, with the increase in the mass percentage of Zn in the alloy melt, the effect of Zn on the improvement of the alloy strength gradually decreases, and the elongation of the alloy also decreases. Li Yue studied the Al-Zn-Mg-Cu alloy without adding a grain refiner and found that the minimum and maximum hot cracking sensitivity Zn element addition amounts of the alloy were 4% and 12%, respectively. After adding a grain refiner, the minimum and maximum hot cracking sensitivity Zn element addition amounts of the alloy were 4 – 6% and 9%, respectively. Eskin studied the variation trend of the hot cracking sensitivity of the Al-Zn-Mg-Cu alloy with the Zn element content, and the experimental results showed that when the Zn content was within a certain range, increasing the Cu element content would significantly increase the hot cracking sensitivity of the alloy, and the Zn element content corresponding to the peak hot cracking sensitivity of the alloy decreased.
Grain refiners are widely used in the production of aluminum alloy parts and can play roles in promoting the refinement of the grain structure, improving the mechanical properties of the alloy, reducing segregation and micro-inhomogeneity, inhibiting hot cracking, and improving the fluidity of the alloy, thereby obtaining uniform and defect-free aluminum alloy castings. In recent years, more people have chosen to add rare metal elements as refiners in Al-Zn-Mg-Cu alloy structural parts. Among them, the Zr element is one of the most commonly used rare metal elements in the Al-Zn-Mg-Cu alloy; the most effective grain refiner is the Sc element, but due to its high price, it is usually only used in aerospace and military structural parts. However, during the solidification process, excessive grain refiners will aggregate, leading to quality problems in the alloy casting. Xu Yongtao tested the mechanical and casting properties of the Al-Zn-Mg-Cu alloy containing trace amounts of Sc and Zr. Through experiments on Al-Zn-Mg-Cu alloys with a high Zn/Mg ratio and different Zn, Mg, and Cu contents, the effects of different alloy compositions on the mechanical properties, ductility, fluidity, and hot cracking resistance of the alloy were analyzed, and finally, the Al-11Zn-1.8Mg-0.9Cu-0.15Zr-0.15Sc alloy was developed. This alloy has good hot cracking resistance. After melt treatment, the grains of the rheological squeeze casting parts are fine and uniform, the number and size of the coarse primary Al₃(Sc, Zr) phase and the low-melting-point eutectic phase at the grain boundaries are reduced. After T6 heat treatment, the low-melting-point eutectic phase almost completely dissolves into the matrix, and the mechanical properties of the casting are significantly improved. The average tensile strength reaches 565 MPa, and the average elongation is 7.5%. At the same time, the consistency and stability of the mechanical properties are significantly improved.
1.2 Research Status of Al-Zn-Mg-Cu Alloy Squeeze Casting
1.2.1 Squeeze Casting Technology
Squeeze casting technology, also known as liquid forging, is a near-net-shape casting process that combines casting and hot forging technologies. It has a series of outstanding advantages such as being green, high-quality, high-production efficiency, and short process flow. The schematic diagram of its process principle is shown in Figure 1. The alloy melt is directly poured into the lower mold cavity, and then the upper mold moves downward at a fixed pressing speed. The alloy melt completes the filling process under pressure. After the filling is completed, the same pressure as that during the downward movement is continuously applied to the upper mold, and the solidification and feeding processes are completed under pressure, and finally, a casting with fewer defects is obtained. During the filling process of squeeze casting, the alloy melt completes the process of filling the lower mold cavity under the uniform extrusion of the upper mold. The entire filling process is slow and the flow velocity of the alloy melt is stable, which can effectively avoid defects such as air entrainment in the alloy melt during the filling process, resulting in a decrease in the alloy quality. Moreover, pressure is always applied to the pressure head during the filling and solidification process, which increases the cooling rate of the alloy melt and at the same time reduces the critical nucleus size of nucleation, increasing the number of nuclei during the nucleation process, so that the grain size of the produced casting is significantly finer. Squeeze casting technology combines the characteristics of forging and casting technologies. After the squeeze casting melt solidifies under pressure, the casting and the mold cavity wall are closely fitted, the heat conduction and solidification speed are increased, and the grains are further refined, and the performance of the alloy is improved. Compared with traditional casting technologies, squeeze casting technology has the advantages of high material utilization rate, stable casting performance, and simple operation. At the same time, it can eliminate casting defects such as shrinkage porosity and is suitable for preparing castings such as hubs, valve bodies, and pistons. It is an alternative casting forming technology for low-cost preparation of large and high-strength complex components.
Squeeze casting technology was invented in the former Soviet Union in 1937 and was introduced to China and other countries in the 1950s and 1960s and has been widely used. In recent years, a large number of studies have been conducted on the squeeze casting forming of Al-Zn-Mg-Cu series ultra-high strength aluminum alloys at home and abroad, and castings with good strength and elongation have been cast. Hou Liqun applied squeeze casting technology to form 7A04 aluminum alloy. After 450°C/7h + 460°C/3h solution treatment and 120°C/24h aging treatment, the yield strength, tensile strength, and elongation of the casting reached 410 MPa, 475 MPa, and 7.5%,…
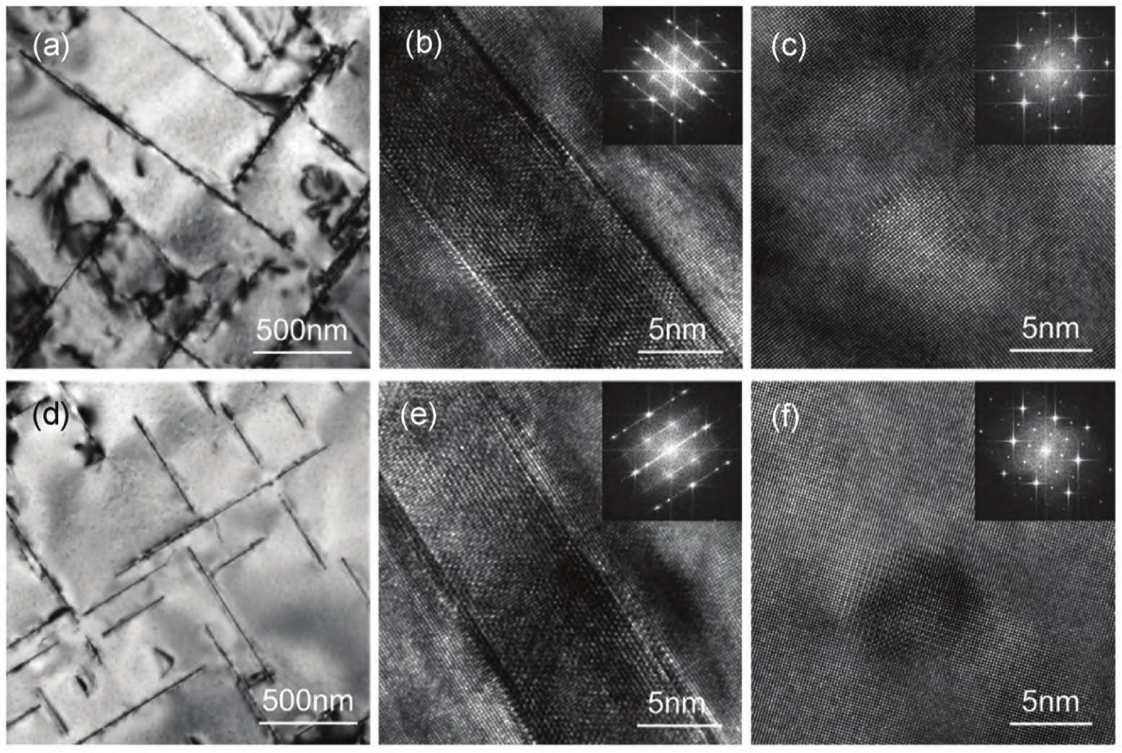