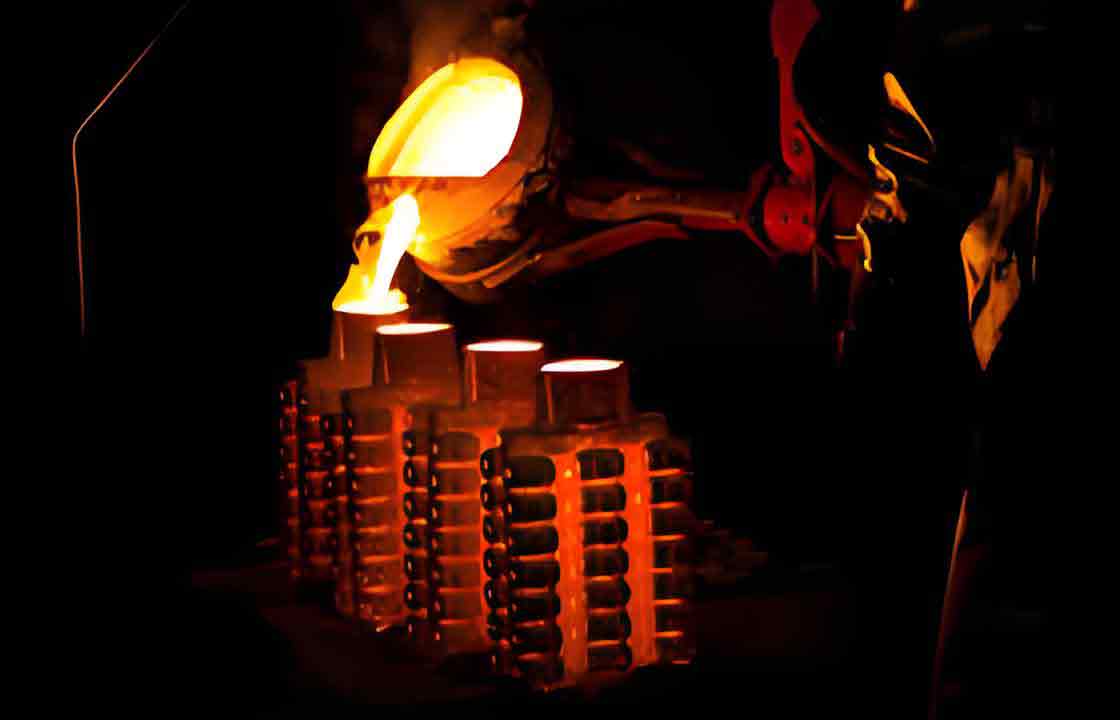
Lost wax casting is highly versatile and precise manufacturing process widely used for producing complex and intricate metal components. This method is particularly advantageous for high-volume production due to its ability to create parts with excellent dimensional accuracy and surface finish. However, achieving cost-effectiveness in high-volume lost wax casting requires careful planning and optimization of various production strategies. This article explores several cost-effective production strategies, highlighting their benefits and addressing common casting defects.
Introduction to Lost Wax Casting
Lost wax casting involves creating a wax pattern of the desired part, coating it with a ceramic shell, and then melting out the wax to leave a cavity. Molten metal is then poured into this cavity, and once it solidifies, the ceramic shell is removed to reveal the metal casting. This process is particularly advantageous for producing components with complex geometries and fine details.
Key Steps in Lost Wax Casting
- Pattern Creation: A wax model of the desired part is created using injection molding or hand carving.
- Assembly: Multiple wax models can be assembled onto a wax tree to create multiple parts in a single batch.
- Shell Building: The wax assembly is repeatedly dipped into a ceramic slurry and coated with fine sand to build a ceramic shell.
- Dewaxing: The ceramic shell is heated to remove the wax, leaving a hollow cavity.
- Metal Pouring: Molten metal is poured into the ceramic mold.
- Shell Removal: Once the metal has solidified, the ceramic shell is broken away to reveal the casting.
- Finishing: The casting is cleaned, and any excess material is removed to achieve the final product.
Cost-Effective Strategies in High-Volume Lost Wax Casting
To achieve cost-effectiveness in high-volume lost wax casting, manufacturers need to optimize various aspects of the production process. The following strategies can significantly reduce costs while maintaining high quality.
1. Efficient Wax Pattern Production
Efficient production of wax patterns is crucial for high-volume lost wax casting. Using high-quality wax and automated injection molding machines can increase the speed and consistency of pattern production.
- Benefits: Reduces production time, improves pattern consistency, and minimizes defects.
- Strategies: Use high-quality wax, invest in automated injection molding machines, and optimize pattern designs for ease of molding.
2. Optimized Shell Building Process
Optimizing the ceramic shell building process can reduce material costs and improve production efficiency. This involves using high-quality ceramic materials and ensuring uniform application and drying.
- Benefits: Reduces material waste, improves shell strength, and minimizes shell-related defects.
- Strategies: Use high-quality ceramic materials, ensure uniform slurry application, and maintain proper drying conditions.
3. Controlled Metal Pouring Parameters
Controlling metal pouring parameters, such as temperature and pouring speed, can reduce casting defects and improve yield rates. Proper control ensures consistent quality and minimizes scrap rates.
- Benefits: Reduces casting defects, improves yield rates, and enhances overall quality.
- Strategies: Monitor and control metal temperature, maintain consistent pouring speed, and use degassing techniques to remove trapped gases.
4. Advanced Inspection and Quality Control
Implementing advanced inspection and quality control measures can detect defects early in the process, reducing rework and scrap rates. Non-destructive testing methods, such as X-ray and ultrasonic testing, can identify internal defects.
- Benefits: Reduces rework and scrap rates, improves overall quality, and enhances customer satisfaction.
- Strategies: Use non-destructive testing methods, implement automated inspection systems, and establish strict quality control protocols.
5. Efficient Post-Casting Finishing
Efficient post-casting finishing processes, such as grinding, polishing, and surface treatment, can improve the final product quality and reduce costs associated with rework.
- Benefits: Enhances surface finish, reduces rework costs, and improves product aesthetics.
- Strategies: Use automated finishing equipment, implement standardized finishing procedures, and train workers in efficient finishing techniques.
Addressing Common Casting Defects
Casting defects can significantly impact the cost-effectiveness of high-volume lost wax casting. The following are common casting defects and strategies to mitigate them.
Common Casting Defects
- Surface Roughness: Caused by improper wax pattern quality or ceramic shell application.
- Inclusions: Foreign particles trapped in the casting surface.
- Porosity: Small voids or cavities caused by trapped gases or shrinkage.
- Shell Cracking: Cracks in the ceramic shell that transfer to the casting surface.
Mitigation Strategies
Defect | Cause | Mitigation Strategies |
---|---|---|
Surface Roughness | Poor wax pattern quality, improper ceramic shell application | Use high-quality wax, precise pattern-making techniques, uniform slurry application |
Inclusions | Foreign particles in casting surface | Ensure clean working environment, filter molten metal before pouring |
Porosity | Trapped gases, shrinkage | Control metal pouring temperature, use degassing techniques, optimize risers and feeders |
Shell Cracking | Improper shell building, thermal stresses | Apply slurry uniformly, proper drying between layers, control cooling rates |
Cost-Benefit Analysis of Optimized Strategies
Implementing optimized strategies for high-volume lost wax casting can lead to significant cost savings. The following table provides a cost-benefit analysis of the key strategies discussed.
Strategy | Initial Investment | Cost Savings | Benefits |
---|---|---|---|
Efficient Wax Pattern Production | High | High | Reduces production time, improves pattern consistency, minimizes defects |
Optimized Shell Building Process | Moderate | Moderate to High | Reduces material waste, improves shell strength, minimizes shell-related defects |
Controlled Metal Pouring Parameters | Moderate | High | Reduces casting defects, improves yield rates, enhances overall quality |
Advanced Inspection and Quality Control | High | High | Reduces rework and scrap rates, improves overall quality, enhances customer satisfaction |
Efficient Post-Casting Finishing | Moderate to High | Moderate to High | Enhances surface finish, reduces rework costs, improves product aesthetics |
Conclusion
Achieving cost-effectiveness in high-volume lost wax casting requires a strategic approach that focuses on optimizing various aspects of the production process. By implementing efficient wax pattern production, optimizing the shell building process, controlling metal pouring parameters, adopting advanced inspection and quality control measures, and ensuring efficient post-casting finishing, manufacturers can significantly reduce costs while maintaining high quality.
Addressing common casting defects through improved processes and quality control further enhances the cost-effectiveness of lost wax casting. By focusing on these advanced strategies, manufacturers can continue to leverage lost wax casting for a wide range of applications, delivering high-quality components at a competitive cost.