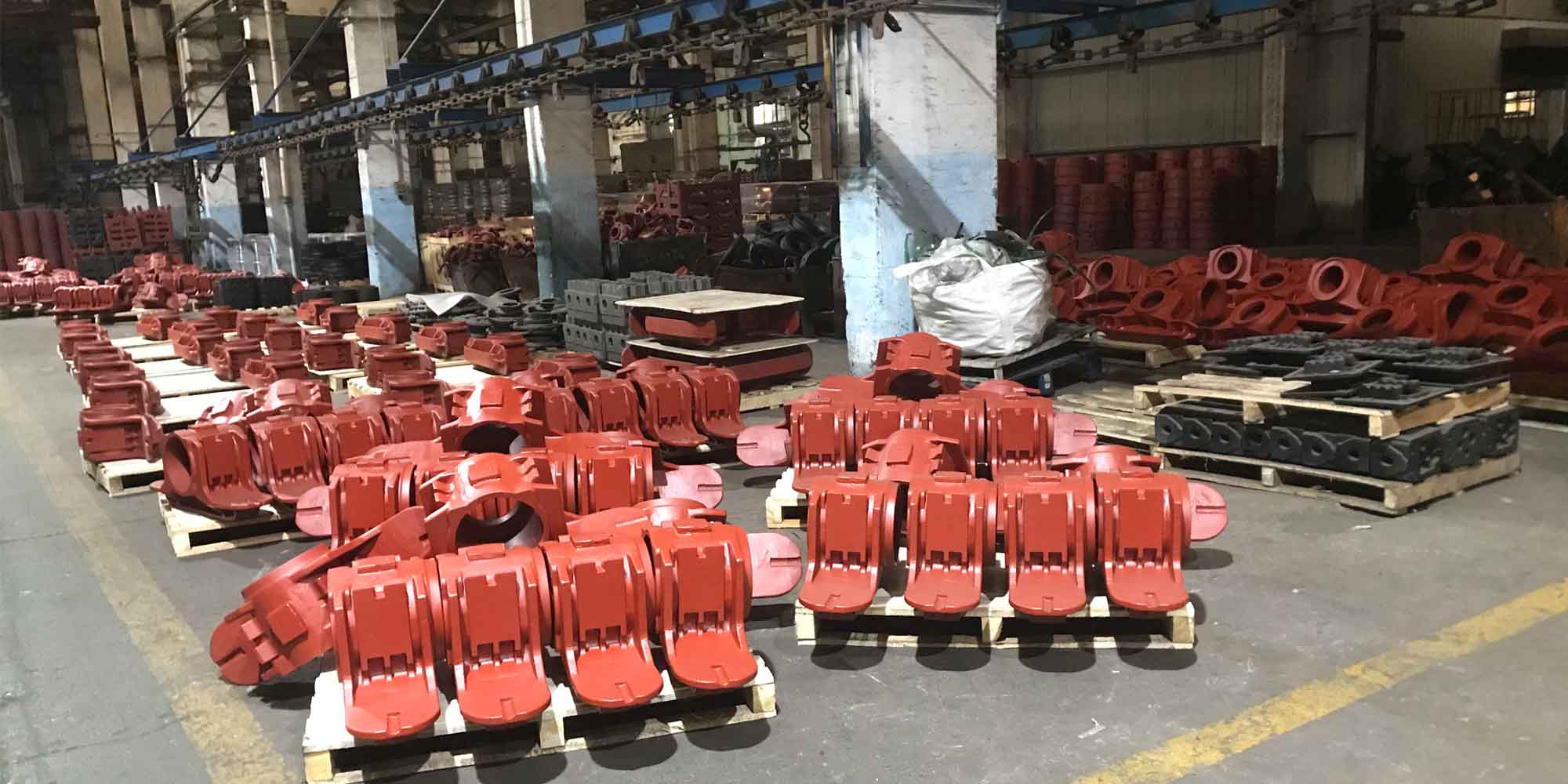
Sand casting remains a fundamental process in modern manufacturing despite the emergence of newer technologies like 3D printing and CNC machining. It offers unique advantages but also faces specific limitations, which influence its applicability across different industries. Here’s a closer look at the advantages and limitations of sand casting in contemporary manufacturing contexts.
Advantages of Sand Casting
- Cost-Effectiveness: Sand casting is generally more affordable than other casting methods, especially for small to medium production runs. The materials (sand and binders) and the equipment required are relatively inexpensive.
- Versatility in Materials: This method can be used with a wide range of metals, including iron, steel, aluminum, bronze, and more, making it very versatile in terms of material compatibility.
- Complex Geometries: Sand casting is capable of producing complex shapes that would be difficult or expensive to achieve with other manufacturing processes. The flexibility of sand molds allows for intricate designs and undercuts.
- Size Capability: It can accommodate very large parts — larger than those typically feasible with other forms of sand casting. This makes it ideal for heavy equipment, large art pieces, and industrial components.
- Small Quantity Production: It is suitable for small batch production or even one-off custom pieces without significant cost penalties, which is beneficial for custom or bespoke manufacturing.
Limitations of Sand Casting
- Surface Finish and Tolerance: One of the primary drawbacks of sand casting is the relatively rough surface finish and the lower dimensional accuracy compared to other casting methods like die casting or investment casting. Additional machining and finishing processes are often required to meet precise specifications.
- Mold Deterioration: Sand molds cannot be reused. Each new casting requires a new mold, leading to increased labor and material costs, especially across large production volumes.
- Porosity: Sand casting can lead to issues with porosity, especially if the sand contains moisture or if gases trapped during the pouring solidify inside the molten metal. This can weaken the final product.
- Labor-Intensive: The process can be labor-intensive, particularly in pattern making, mold preparation, and finishing steps. This reliance on manual labor can introduce variability in the final products’ quality.
- Environmental Concerns: The sand used in sand casting can contain silica, which poses health risks during handling. Moreover, the disposal of used sand and emissions from melting metals can have environmental impacts, requiring effective management and regulatory compliance.
Applications in Modern Manufacturing
Despite these limitations, sand casting remains indispensable in various sectors:
- Automotive: For producing engine blocks, cylinder heads, and manifolds where the size and complexity are well-suited to sand casting.
- Heavy Machinery: Large machinery parts such as housings and large gears are typically produced using this method.
- Art and Decor: Sculptures and decorative items benefit from the flexibility of sand molds.
- Construction: Cast metal components used in construction, like brackets and frames, are often made through sand casting due to the cost-effectiveness in producing large, robust parts.
Conclusion
In conclusion, while sand casting offers numerous benefits such as cost efficiency, versatility, and the ability to produce complex and large parts, it also requires consideration of its drawbacks like poor surface finish, labor intensity, and environmental impact. Understanding these trade-offs is crucial for manufacturers deciding whether sand casting is the right choice for their specific applications. As manufacturing technologies evolve, integrating traditional methods like sand casting with modern advancements can optimize production processes, enhancing efficiency and sustainability.