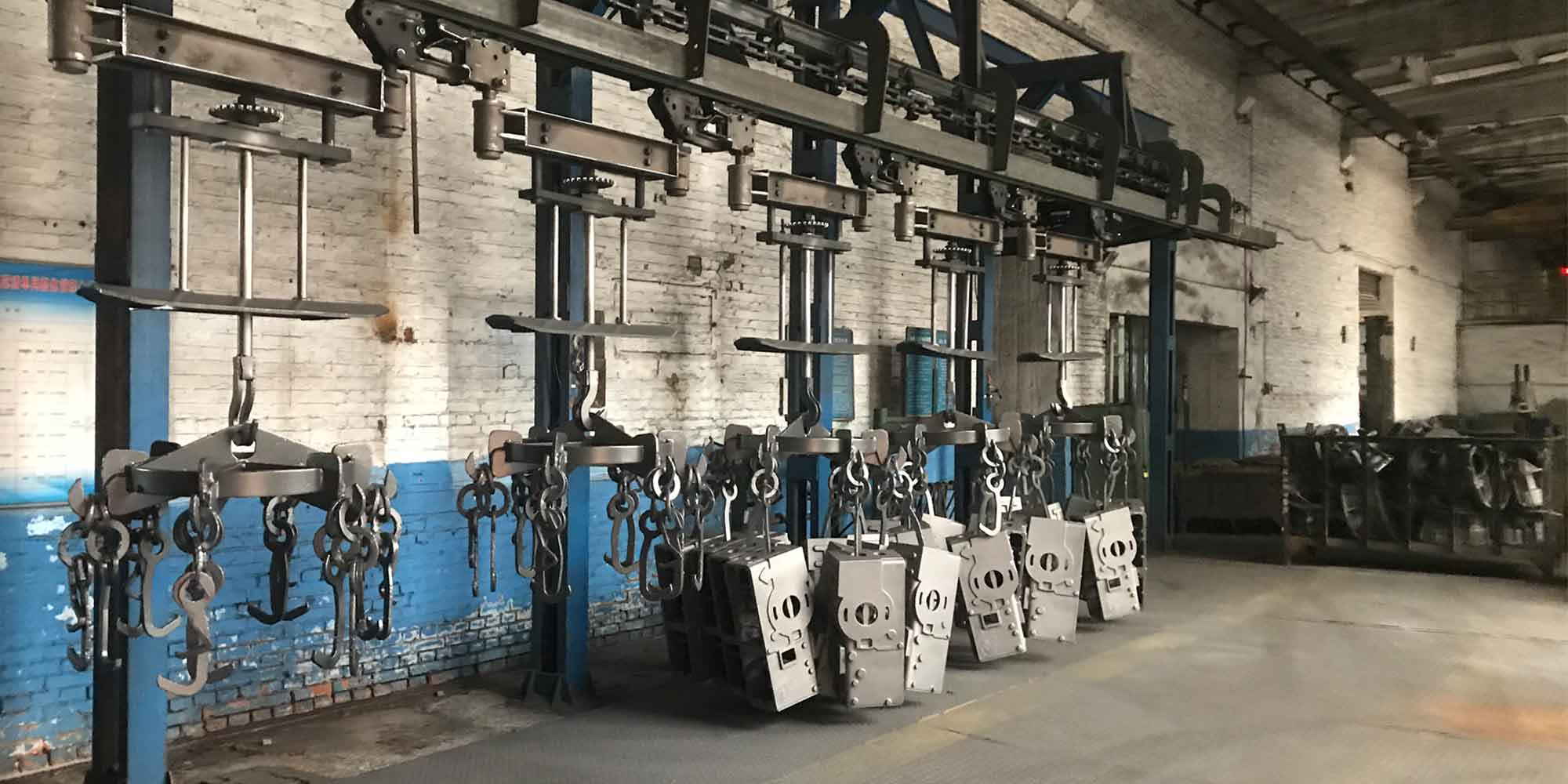
Troubleshooting in sand casting is crucial for maintaining the quality of the cast parts and the efficiency of the production process. Common issues in sand casting can lead to defects in the final product, increased production costs, and delays. Here’s a guide to identifying and troubleshooting some of the most frequent problems encountered in sand casting operations:
1. Misruns and Cold Shuts
Issue: Misruns occur when the molten metal fails to fill the mold cavity completely, resulting in incomplete castings. Cold shuts happen when two streams of molten metal meet but do not fuse properly, creating a weak spot.
Causes:
- Low pouring temperature.
- Inadequate gating system.
- Too fast or too slow pouring rates.
Solutions:
- Adjust the molten metal temperature to ensure it remains fluid enough to fill the mold.
- Redesign the gating system to facilitate a smoother and more adequate flow of metal.
- Modify pouring rates to optimal levels, ensuring consistent metal flow.
2. Sand Inclusions and Blowholes
Issue: Sand inclusions are pieces of sand or dirt that become trapped in sand casting, while blowholes are small cavities or pores in sand casting caused by trapped air or gases.
Causes:
- Poor sand condition or contamination.
- Insufficient venting in the mold.
- High moisture content in the sand.
Solutions:
- Regularly check and maintain the quality of the sand. Ensure it is clean and properly prepared.
- Improve venting in the mold to allow gases to escape more effectively.
- Control the moisture content of the sand to prevent steam generation during sand casting.
3. Shrinkage Defects
Issue: Shrinkage defects manifest as depressions or internal voids in sand casting, caused by the metal contracting as it cools.
Causes:
- Insufficient material feeding into certain areas of the mold.
- Inadequate gating system.
- Improper cooling rates.
Solutions:
- Implement risers to supply extra molten metal to areas prone to shrinkage.
- Review and modify the gating system to ensure a more uniform and controlled fill and solidification.
- Adjust cooling rates and use controlled cooling practices to manage the shrinkage more effectively.
4. Mold Shifts and Mismatch
Issue: This occurs when the cope and drag sections of the mold do not align properly, leading to a displacement in the sections of sand casting.
Causes:
- Improper securing of the mold halves.
- Inaccurate alignment of the cope and drag.
Solutions:
- Ensure that the flask and other supporting structures are stable and robust.
- Check and adjust the alignment mechanisms regularly to maintain precision in mold assembly.
5. Hot Tearing
Issue: Hot tearing or cracking occurs when the metal is restrained from contracting freely during cooling, leading to tears or cracks.
Causes:
- Inflexible mold design.
- Rapid or uneven cooling rates.
Solutions:
- Design molds to accommodate the contraction of metal, especially in areas where hot tears commonly occur.
- Manage cooling rates and ensure even cooling to minimize stresses in the metal.
Conclusion
Effective troubleshooting in sand casting involves a comprehensive understanding of the molding process, materials used, and the behavior of molten metal. Regular monitoring, timely maintenance of equipment, and adherence to best practices in mold design and operation are critical to minimizing defects and enhancing the quality and efficiency of sand casting process. By addressing these common issues proactively, manufacturers can reduce waste, improve productivity, and deliver higher-quality cast products.