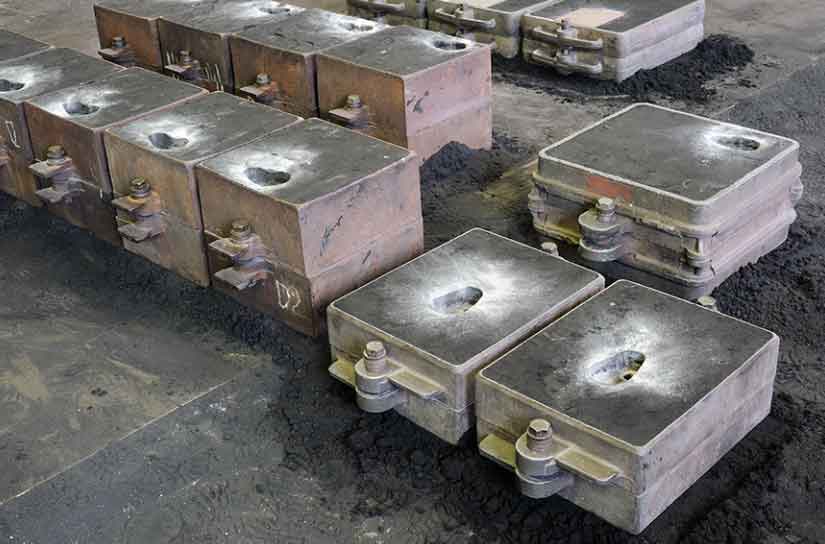
Creating complex metal parts with resin sand casting requires careful techniques and considerations to ensure successful outcomes. Here are some techniques and considerations to keep in mind:
1. Pattern Design:
The design of the pattern plays a crucial role in creating complex metal parts. The pattern should incorporate features that enable the formation of intricate shapes, thin walls, and internal cavities. It’s important to consider draft angles, undercuts, and features that facilitate the removal of the pattern from the sand mold.
2. Core Creation:
Cores are used to create internal features in the metal part. For complex parts, multiple cores may be required. Proper core design and fabrication techniques are essential to achieve accurate dimensions and desired internal geometries. Cores should be securely positioned within the sand mold to prevent displacement during the casting process.
3. Sand Mix Preparation:
The sand mix for resin sand casting should have the right combination of sand, resin, and additives to achieve optimal mold properties. The sand should have good flowability and compactability to accurately capture the intricate details of the pattern. The resin should provide sufficient strength for mold integrity during handling and pouring.
4. Mold Assembly and Venting:
Careful mold assembly is necessary to ensure precise alignment and proper venting. Venting channels allow gases to escape during the pouring process, preventing defects like porosity or gas entrapment. Strategic placement of vents is crucial to maintain dimensional accuracy and avoid casting defects.
5. Pouring and Solidification:
Proper pouring techniques are vital to achieve complete filling of the mold cavity without causing turbulence or defects. Molten metal should be poured at the appropriate temperature and with controlled speed to ensure proper flow and minimize the risk of defects. Understanding the solidification characteristics of the metal being cast is crucial to prevent shrinkage or hot spots.
6. Cooling and Solidification Control:
Controlling the cooling and solidification process is important for complex metal parts. Techniques like chills or controlled cooling rates may be employed to prevent cracking, shrinkage, or distortion. Strategic placement of risers and gating systems helps ensure proper metal flow and solidification throughout the part.
7. Post-Casting Processes:
After solidification, the casting undergoes post-casting processes such as shakeout, removal of gating system, and cleaning of residual sand. Depending on the complexity of the part, additional processes like machining, heat treatment, surface finishing, or assembly may be required to achieve the final desired specifications.
8. Quality Control and Inspection:
Implementing thorough quality control measures is crucial to ensure the dimensional accuracy and quality of complex metal parts. Inspection techniques like visual inspection, dimensional measurement, non-destructive testing, and material testing help identify any defects or deviations from specifications.
9. Iterative Design and Process Improvement:
Creating complex metal parts with resin sand casting often involves an iterative process of design refinement and process improvement. Each casting cycle provides an opportunity to learn and optimize the design, mold assembly, pouring parameters, and post-casting processes. Collaboration between foundries, design engineers, and casting experts facilitates continuous improvement and the achievement of the desired complex part specifications.
Creating complex metal parts with resin sand casting requires expertise, attention to detail, and a thorough understanding of the specific requirements of the part. By employing proper techniques, considering design complexities, optimizing the casting process, and implementing quality control measures, successful production of complex metal parts can be achieved.