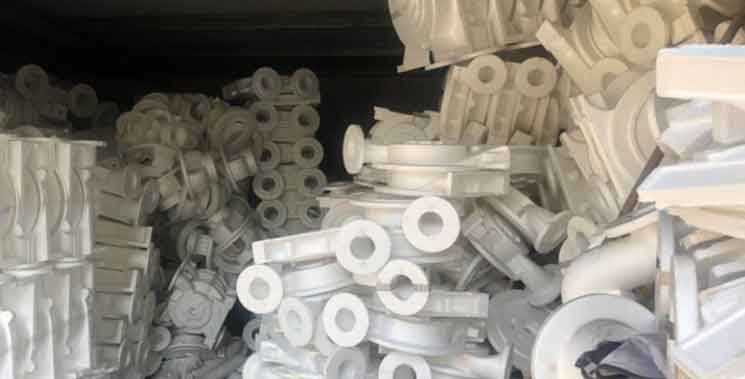
Lost foam casting offers several advantages and finds numerous applications in modern manufacturing. Here are some of the key advantages and applications of lost foam casting:
Advantages of Lost Foam Casting:
- Design Freedom: Lost foam casting allows for the production of complex and intricate shapes that may be challenging or costly to achieve with other casting methods. The foam patterns can be easily shaped, providing design flexibility and the ability to create intricate details and thin-walled sections.
- Cost-Effective: Lost foam casting can be cost-effective for the production of small to medium-sized quantities. The process eliminates the need for costly and time-consuming pattern-making and assembly steps required in other casting methods. Additionally, it minimizes material waste since the foam patterns are vaporized, reducing material costs.
- Excellent Surface Finish: Lost foam casting typically produces parts with excellent surface finish due to the smooth and high-quality foam patterns used. The absence of parting lines or draft angles on the final casting reduces the need for extensive post-casting finishing operations.
- Weight Reduction: The use of foam patterns allows for the creation of lightweight castings, making lost foam casting suitable for applications where weight reduction is desired, such as in the aerospace or automotive industries.
- Dimensional Accuracy: Lost foam casting can achieve high dimensional accuracy and tight tolerances due to the precise replication of the foam pattern in the casting process. This reduces the need for extensive post-casting machining or finishing.
Applications of Lost Foam Casting:
- Automotive Industry: Lost foam casting is widely used in the automotive industry for the production of engine blocks, cylinder heads, intake manifolds, exhaust manifolds, and other components. The process allows for the production of complex geometries, intricate cooling passages, and precise features.
- Aerospace Industry: Lost foam casting is employed in the aerospace industry for manufacturing components such as turbine blades, compressor housings, and structural parts. The process enables the production of intricate, lightweight, and high-performance parts for aircraft engines and structures.
- Pump and Valve Industry: Lost foam casting is utilized for producing pump and valve components that require complex internal passages, precise features, and high-quality surface finish. The process allows for the production of customized and efficient components for fluid handling applications.
- Energy and Power Generation: Lost foam casting finds applications in the energy and power generation sector for manufacturing components such as impellers, turbine parts, and heat exchanger components. The process enables the production of parts with intricate cooling channels, precise geometries, and superior performance.
- General Engineering: Lost foam casting is used in various general engineering applications for producing components with complex shapes, such as gearbox housings, gear blanks, and machinery parts. The process offers design flexibility, cost-effectiveness, and the ability to produce customized parts.
Lost foam casting is a versatile and cost-effective casting method that finds widespread use in various industries. Its advantages in design flexibility, cost-effectiveness, excellent surface finish, weight reduction, and dimensional accuracy make it an attractive choice for producing complex and high-quality metal components.