Custom solutions in ductile iron casting process are essential for meeting the specific needs of different industries. Each industry has unique requirements based on the application, environment, and performance expectations of the iron cast components. Here’s how the ductile iron casting process can be tailored for various industry needs:
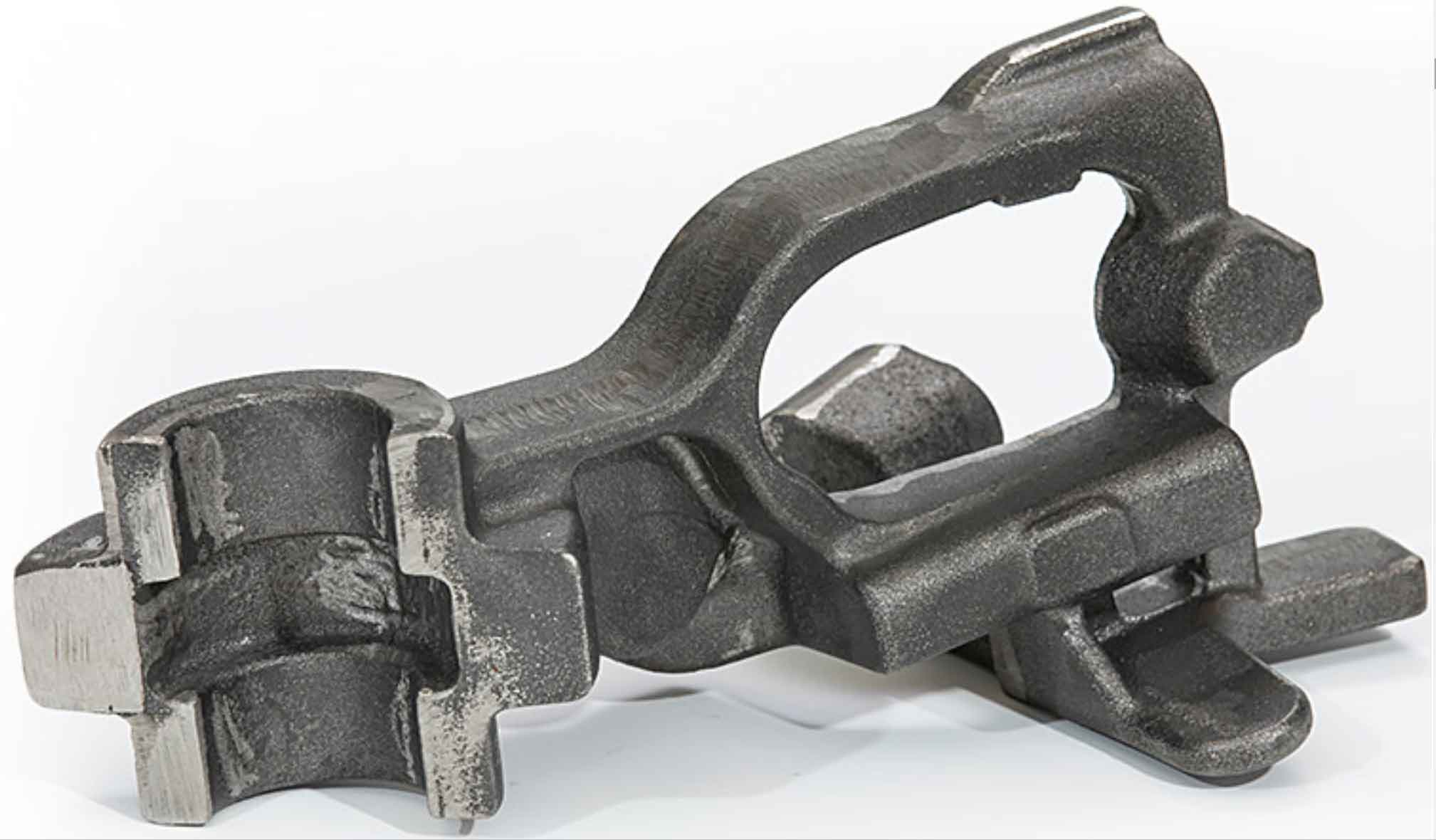
- Automotive Industry: For automotive applications, ductile iron must possess high strength, wear resistance, and toughness. Modifications in ductile iron casting process can include alloying to improve heat resistance and fatigue strength, ideal for engine blocks, gears, and suspension components.
- Construction and Infrastructure: In these sectors, ductile iron is valued for its durability and strength. Ductile iron casting process might be tailored to enhance corrosion resistance and weatherability, particularly important for outdoor applications like pipes, manhole covers, and structural supports.
- Agricultural Machinery: Agricultural equipment demands cast iron that can withstand rough handling and variable weather conditions. Adjustments in ductile iron casting process could focus on achieving a balance between toughness and machinability, crucial for components like tractor parts and irrigation systems.
- Energy Sector: Whether in traditional or renewable energy sectors, the requirements can be stringent, demanding ductile iron casting process that can withstand high temperatures and pressures. Tailoring in this context might involve precision ductile iron casting process techniques and specialty alloys to ensure durability under extreme conditions.
- Rail and Heavy Transportation: Here, the focus would be on producing ductile iron with excellent impact resistance and the ability to endure heavy loads. Process modifications could include specific heat treatments to enhance these properties.
- Marine Applications: Ductile iron used in marine settings must resist saltwater corrosion. Ductile iron casting process might be adapted by incorporating elements like nickel or chromium to enhance corrosion resistance.
- Custom Machinery and Equipment: For bespoke machinery, ductile iron casting process can be adapted to produce complex shapes with specific mechanical properties, depending on the machine’s intended use.
- Consumer Products: When used in consumer goods, aesthetics can be as important as functionality. Ductile iron casting process might be adjusted for a smoother surface finish or to allow for intricate designs.
In all these cases, the key aspects to consider include the choice of raw materials, control of the melting process, mold design, cooling rate, and post-casting treatments like heat treatment or surface finishing. Each step can be adjusted to meet the specific mechanical and physical properties required by the industry application. Collaboration between foundries and clients is crucial to achieve the desired outcome, often involving a trial-and-error approach to refine the process.