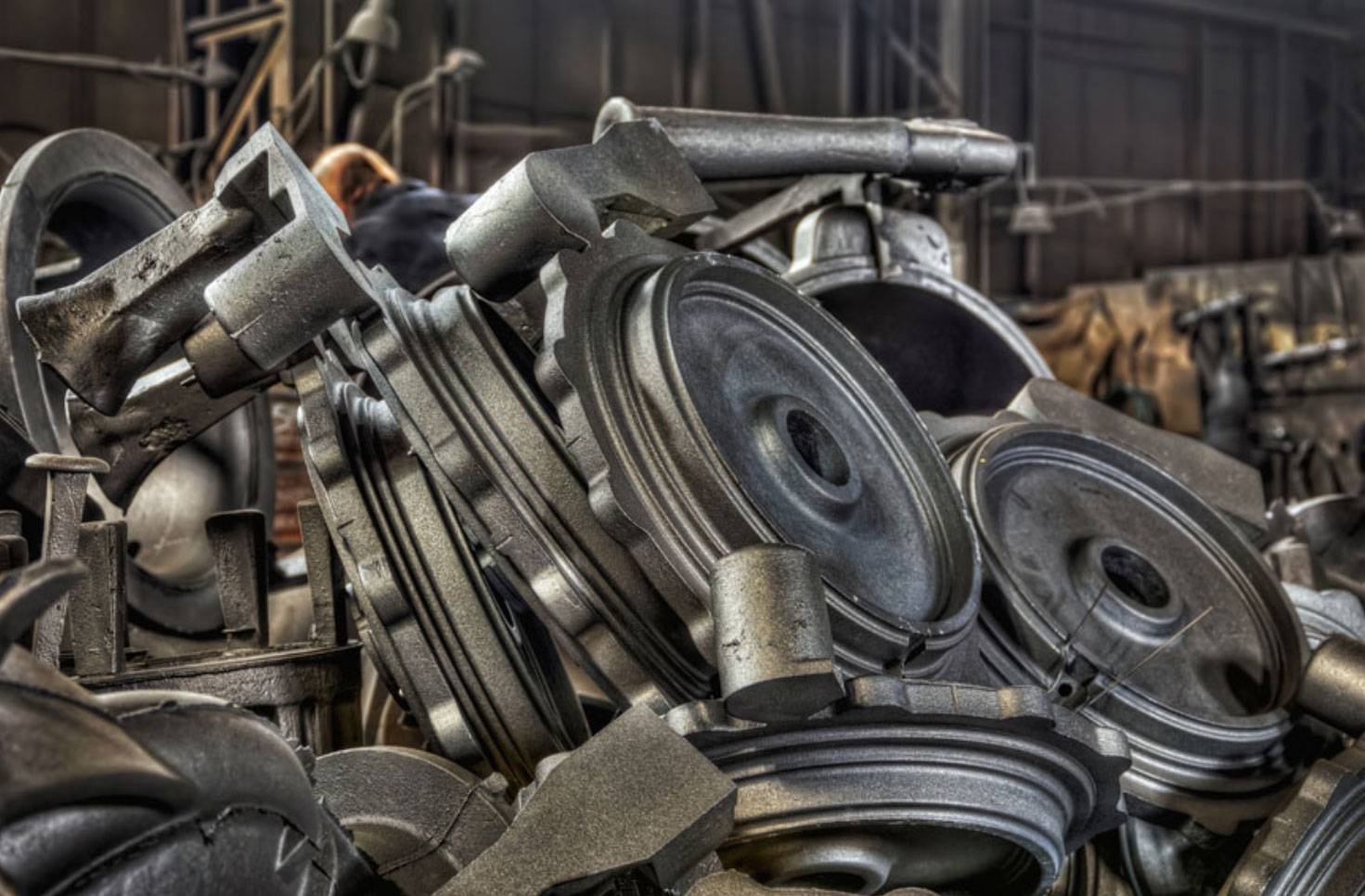
The ductile iron casting process is a method for producing iron-based alloys known for their excellent strength, ductility, and versatility. This process involves several techniques and offers numerous benefits, leading to its widespread applications in various industries. Here’s an overview:
Techniques
- Melting and Alloying: The process begins with melting iron, often using a cupola or electric arc furnace. Alloying elements like magnesium or cerium are added to the melt to help form spherical graphite structures, crucial for ductility.
- Inoculation: This involves adding materials to the molten iron to refine the microstructure and enhance mechanical properties. Inoculants like ferrosilicon can be used to promote graphite nucleation and control its shape and size.
- Nodulization: This is the process of transforming the shape of graphite within the iron from flakes (as in gray iron) to nodules. This transformation, achieved through the addition of magnesium or cerium, is what gives ductile iron its flexibility and strength.
- Casting: The molten iron is then poured into molds. These can be sand molds or other types for more precision casting. Computer-aided design (CAD) and manufacturing technologies enhance the complexity and precision of the molds.
- Cooling and Solidification: After pouring, the metal is allowed to cool and solidify. The cooling rate can affect the microstructure and, hence, the properties of the cast iron.
- Heat Treatment: Post-casting, the iron can undergo various heat treatments like annealing, normalizing, or tempering to achieve desired mechanical properties.
- Finishing and Quality Control: The final steps involve finishing processes like machining, and quality control checks such as X-ray or ultrasonic testing.
Benefits
- High Strength and Ductility: Ductile iron combines the high strength of steel with the high ductility, allowing it to withstand significant stress and deformation without failure.
- Excellent Wear Resistance: Due to its microstructure, it exhibits superior wear resistance, making it ideal for components subjected to constant friction.
- Good Impact and Fatigue Resistance: Ductile iron has a remarkable ability to absorb and withstand shocks and repeated loading cycles.
- Versatility in Applications: Its ability to be cast into complex shapes and sizes with a wide range of mechanical properties makes it extremely versatile.
- Cost-Effectiveness: Generally, it offers a more economical solution compared to steel in terms of both production and performance.
- Machinability: It is easier to machine than many steel grades, saving time and resources in the manufacturing process.
Applications
- Automotive Industry: Used in manufacturing gears, axles, crankshafts, and wheel hubs due to its strength and fatigue resistance.
- Pipeline and Fluid Flow Systems: Ideal for pipes and fittings in water, sewage, and gas distribution systems because of its corrosion resistance and strength.
- Construction: In structural applications like bridge components, where its strength and ductility are essential.
- Heavy Machinery: For components in tractors, oil well pumps, and mining machinery.
- Renewable Energy: In wind turbines and other renewable energy infrastructures, where reliability and durability are critical.
- Municipal Castings: Such as manhole covers and street furniture, where it needs to withstand heavy loads and environmental wear.
- Aerospace: Although less common, it’s used in specific aerospace applications for its high strength-to-weight ratio.
The versatility and performance advantages of ductile iron continue to drive innovation and new applications, making it a key material in modern manufacturing and engineering.