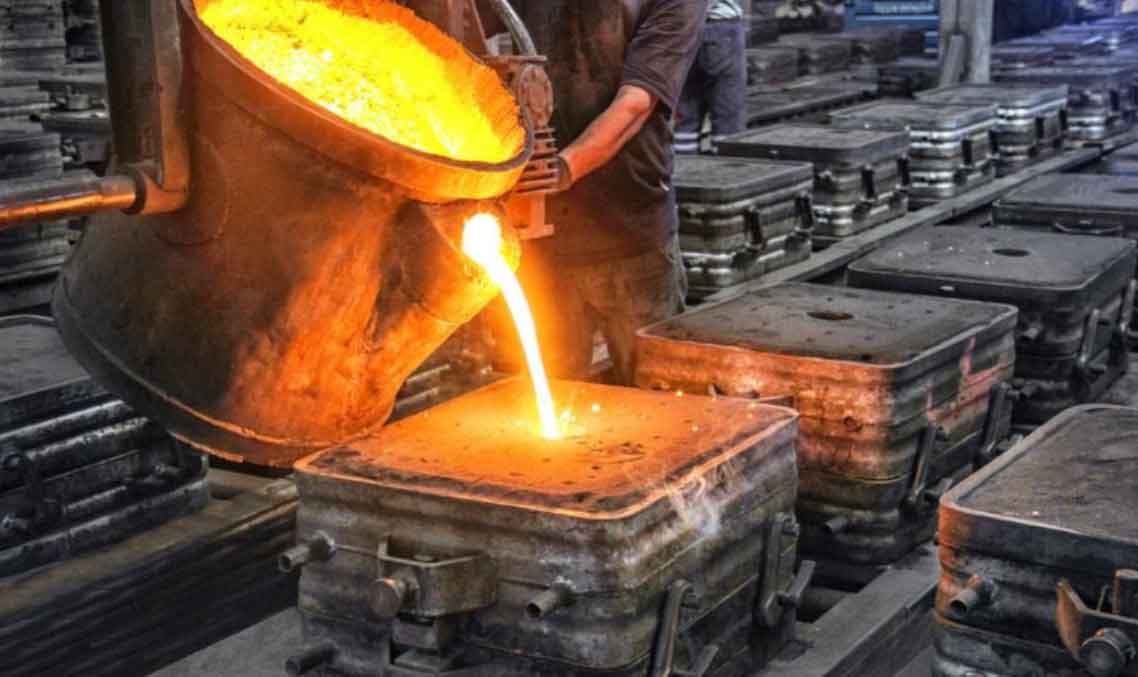
Customization and flexibility are key strengths of sand casting manufacturers, allowing them to meet unique requirements and deliver tailor-made solutions for their customers. Here’s how they achieve this:
- Design Support: Reputable sand casting manufacturers have experienced engineering teams that can work closely with customers to understand their specific needs and provide design support. They can assist in optimizing the design for manufacturability, ensuring the casting meets functional and performance requirements.
- Prototype Development: Sand casting manufacturers can create prototypes quickly and cost-effectively. This enables customers to evaluate and test the design before committing to full-scale production, ensuring the final casting meets their expectations.
- Material Flexibility: Sand casting can accommodate a wide range of materials, including various alloys of aluminum, iron, steel, bronze, and more. Manufacturers can advise on the best material choice based on the application’s mechanical properties, corrosion resistance, and cost considerations.
- Size and Complexity: Sand casting is versatile and can produce castings in various sizes, from small components to large parts. Complex shapes and intricate geometries can also be achieved with sand casting, making it suitable for a diverse range of applications.
- Batch Sizes: Sand casting manufacturers can cater to different batch sizes, from low-volume production for prototyping and small runs to high-volume production for mass manufacturing.
- Tooling Flexibility: Sand casting does not require expensive tooling like other casting methods. It allows manufacturers to modify and adapt the molds quickly and cost-effectively, making it ideal for producing customized castings.
- Secondary Operations: Sand castings can undergo various secondary operations, such as machining, heat treatment, surface finishing, and painting, to meet specific customer requirements and achieve the desired final product.
- Short Lead Times: The relatively simple setup of sand casting allows for shorter lead times compared to other casting methods, which can be beneficial for customers with time-sensitive projects.
- Quality Assurance: Despite the flexibility, sand casting manufacturers maintain strict quality control procedures to ensure that each customized casting meets the required specifications and standards.
- Cost-Effectiveness: Sand casting is cost-effective for both small-scale and large-scale production runs, making it a preferred choice for customers looking for cost-efficient solutions.
By leveraging their expertise in sand casting and their commitment to customer satisfaction, manufacturers can adapt their processes to meet the unique requirements of each project. Whether it’s a one-of-a-kind prototype or a high-volume production, sand casting offers the customization and flexibility needed to deliver optimal solutions for various industries.