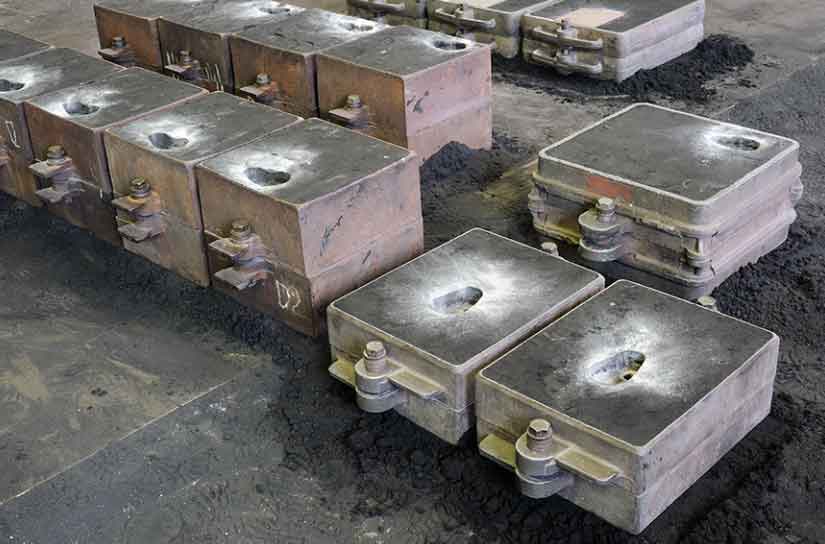
Customization is a key strength of resin sand casting, allowing foundries to tailor solutions to specific needs and requirements. Resin sand casting offers flexibility in design, material selection, and production processes, making it an ideal choice for producing custom-made components. Here are some ways resin sand casting enables customization:
1. Flexible Mold Design:
- Resin sand casting allows for the creation of molds with intricate shapes, undercuts, and complex geometries. This flexibility enables the production of custom components that may have unique design features.
2. Material Selection:
- Resin sand casting can accommodate a wide range of materials, including various metals and alloys. This allows foundries to choose materials that best match the specific performance and functional requirements of the custom parts.
3. Prototype Development:
- Resin sand casting enables the rapid production of prototypes using 3D printed patterns and cores. This allows for quick iteration and testing of custom designs before proceeding to full-scale production.
4. Small to Medium Batch Production:
- Resin sand casting is well-suited for small to medium batch production, making it economical for custom component manufacturing without the need for expensive tooling.
5. Material Properties Tailoring:
- Resin sand casting allows for the optimization of material properties through alloying and process control. Foundries can adjust the composition and treatment of the material to meet specific mechanical, thermal, or chemical requirements.
6. Optimization through Simulation:
- Advanced simulation tools in resin sand casting help optimize the casting process for custom components. This includes analyzing mold filling, solidification, and cooling to ensure the best possible outcomes for the specific design.
7. Adaptability for Diverse Industries:
- Resin sand casting serves diverse industries, from automotive and aerospace to architectural and artistic applications. The versatility of this casting method allows foundries to cater to various industry-specific needs.
8. Part and Assembly Integration:
- Resin sand casting allows for the integration of multiple parts or assemblies into a single casting. This consolidation can simplify assembly processes, reduce the number of components, and enhance overall part performance.
9. Tailored Finishing and Surface Treatments:
- Custom components can receive tailored post-casting finishing and surface treatments to achieve specific aesthetics, corrosion resistance, or other functional characteristics.
10. Client Collaboration:
- Close collaboration with clients is facilitated in resin sand casting to understand their specific needs and requirements. Foundries can work closely with customers to ensure the final custom components meet their expectations.
Resin sand casting’s customization capabilities make it an ideal choice for manufacturing custom components that meet unique design and performance requirements. It empowers foundries to provide tailored solutions to diverse industries and applications, catering to the individual needs of their customers effectively.