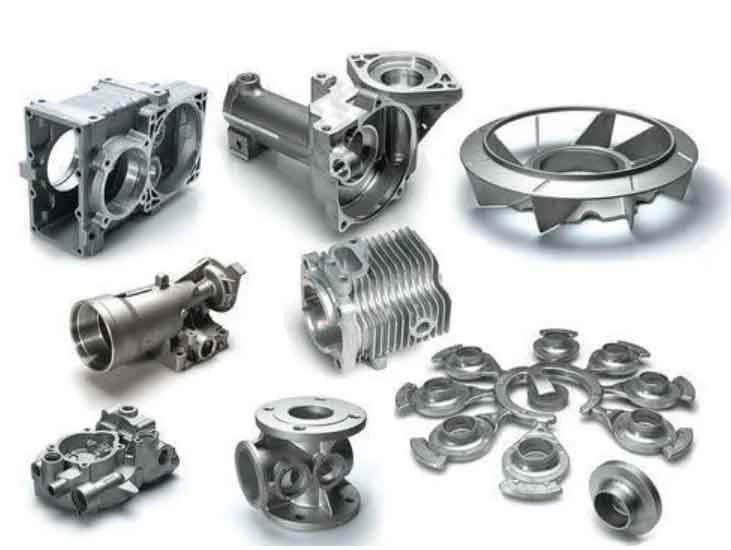
Resin sand casting has been a significant advancement in manufacturing practices within foundries. It has revolutionized the traditional sand casting process, bringing several benefits that enhance efficiency, accuracy, and overall productivity. Here are some ways resin sand casting has advanced manufacturing practices in foundries:
1. Improved Surface Finish and Dimensional Accuracy:
- Resin sand casting offers superior surface finish and dimensional accuracy compared to traditional green sand casting. This advancement ensures that castings meet tight tolerances and require minimal post-casting finishing.
2. Complex Geometries and Intricate Designs:
- Resin sand casting allows foundries to produce components with intricate designs, undercuts, and thin walls, enabling the manufacturing of complex geometries that were challenging with green sand casting.
3. Reduction in Defects and Scrap Rates:
- The use of resin-bonded sand and advanced mold preparation techniques in resin sand casting has resulted in a significant reduction in casting defects and scrap rates, leading to cost savings and higher productivity.
4. Optimization through Simulation:
- Foundries increasingly employ computer simulation software to analyze mold filling, solidification, and cooling processes. This helps optimize process parameters and prevent defects, leading to improved casting quality and reduced lead times.
5. Material and Alloy Versatility:
- Resin sand casting accommodates a wide range of materials and alloys, including ferrous and non-ferrous metals, high-temperature alloys, and metal matrix composites. This versatility allows foundries to serve diverse industries and applications.
6. Faster Prototyping and Time-to-Market:
- The ability to produce rapid prototypes with 3D printed patterns and cores in resin sand casting has shortened product development cycles, enabling faster time-to-market for new components.
7. Automation and Process Control:
- Resin sand casting has integrated automation into various stages of the process, enhancing consistency and reducing human error. Automation has also allowed for real-time process monitoring and control, leading to more reliable and repeatable results.
8. Environmental Friendliness:
- Resin sand casting generates less waste compared to traditional sand casting methods, contributing to a more environmentally friendly and sustainable manufacturing process.
9. Cost-Effectiveness for Medium to High Volumes:
- Resin sand casting strikes a balance between cost-effectiveness and quality for medium to high production volumes, making it an attractive option for foundries catering to various customer demands.
10. Enhanced Quality Assurance and Traceability:
- Advanced quality control and inspection methods, along with better traceability of materials and processes, ensure that the final castings meet the required specifications and comply with industry standards.
Resin sand casting has brought significant advancements to manufacturing practices in foundries. Its ability to produce high-quality castings with complex geometries, reduced defects, and efficient processes has made it a preferred casting method across various industries. As technology and materials continue to evolve, resin sand casting is expected to further contribute to the growth and innovation in the foundry industry.