The 7274 flywheel housing is a Weichai engine clay sand casting developed by the company in 2022, with a material grade of HT250 and a raw weight of 20.5 kg, as shown in Figures 1 and 2.
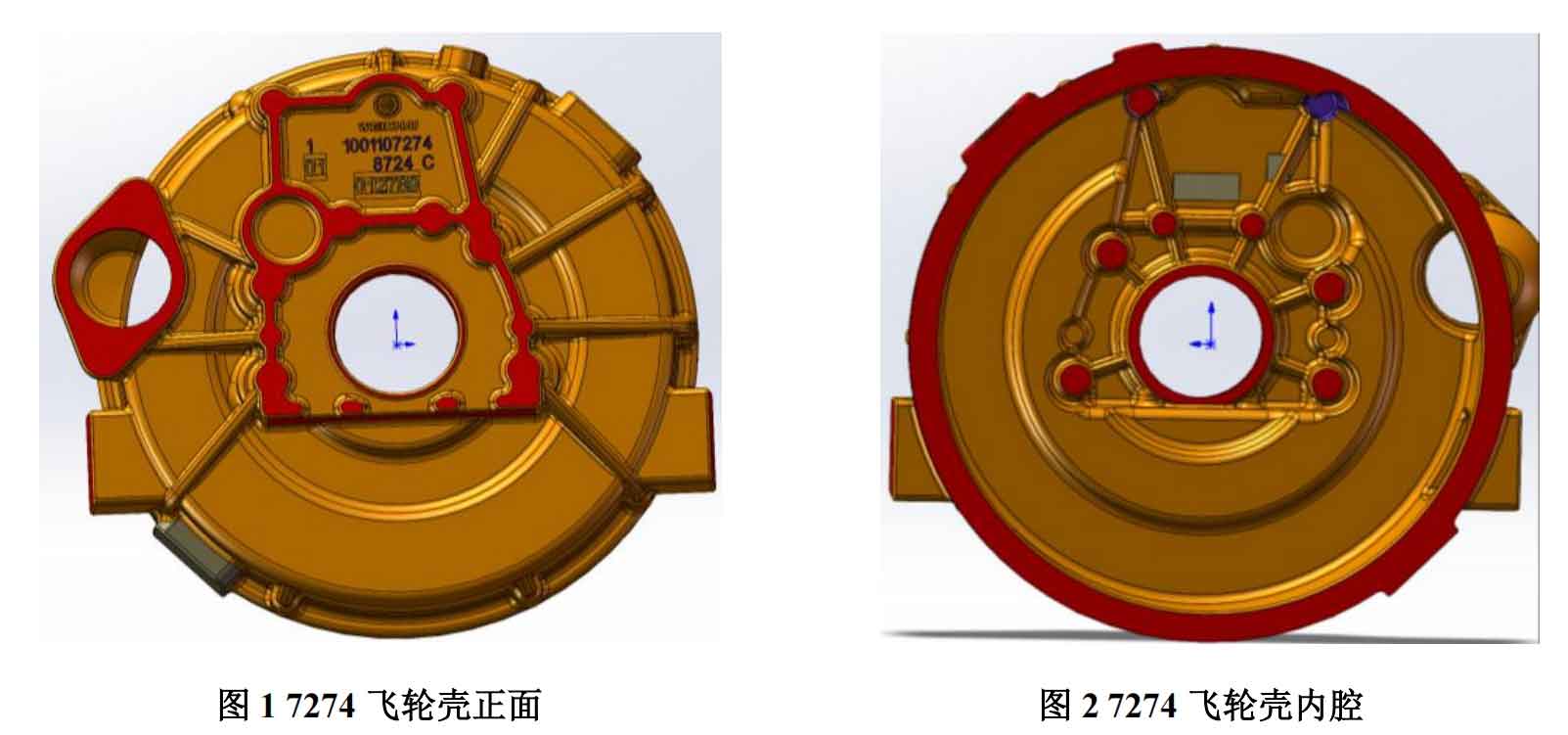
Using clay sand static pressure molding and laminating sand hot core production process (Figure 3, Figure 4, Figure 5).
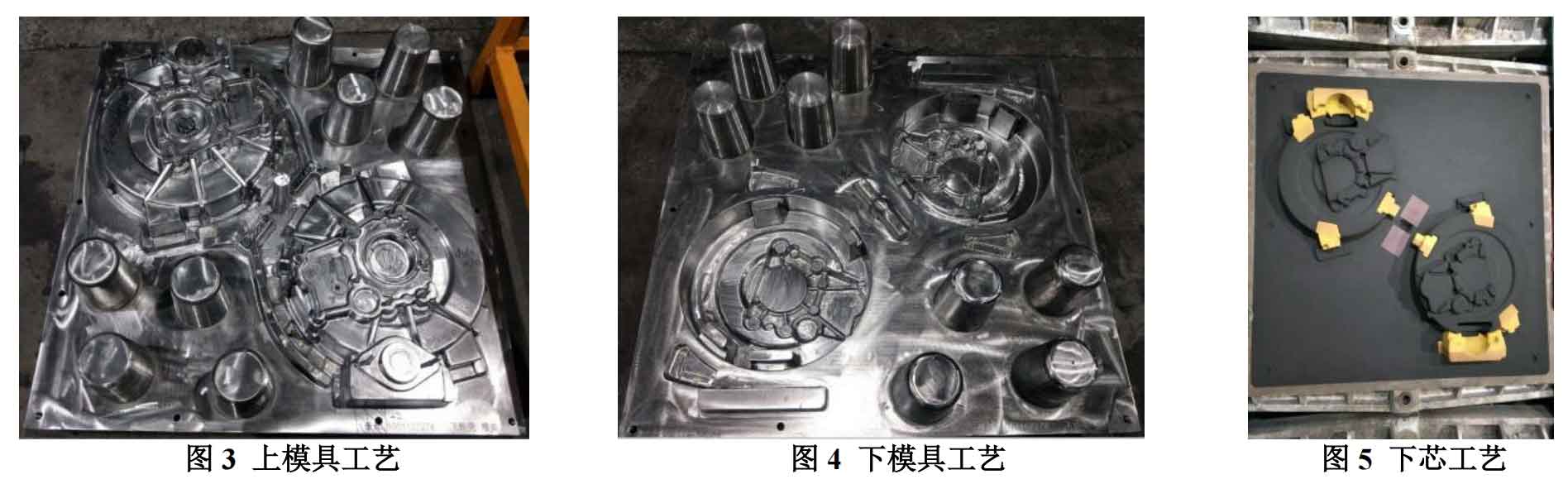
During the mass production process of clay sand castings, local surface sand sticking defects often occur (Figure 6, Figure 7), and even severe gas explosion sand sticking (Figure 8).
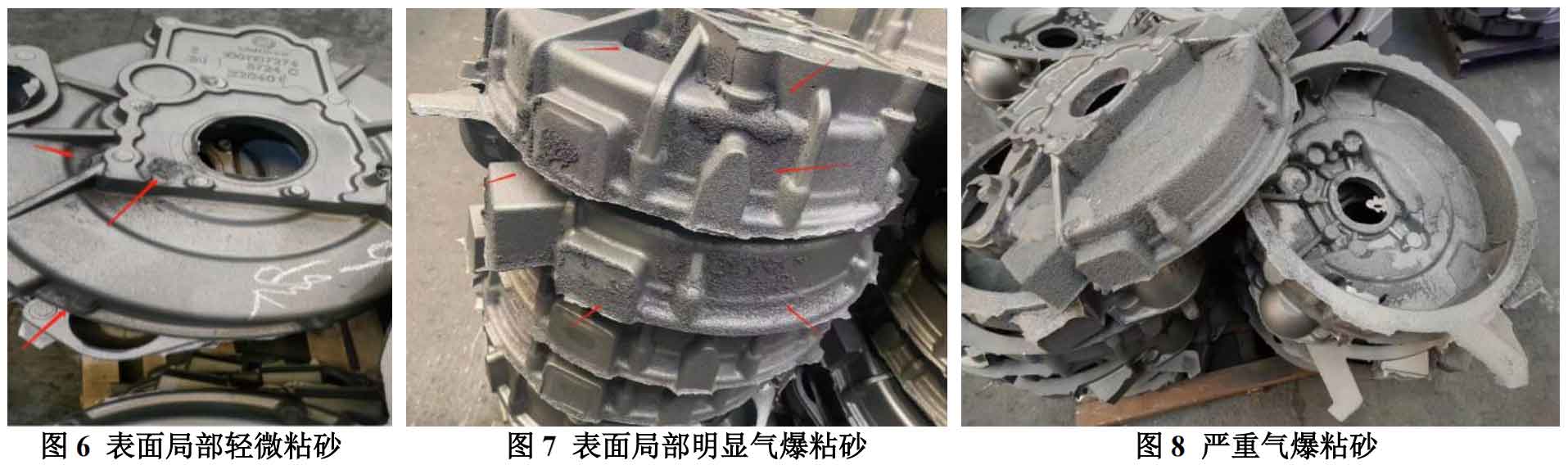
In response to the surface gas explosion and sand sticking problem of castings, the following improvement measures have been taken:
(1) Reduce the flow resistance area and extend the pouring time. Shorten the overlap length of the transverse runner with the minimum flow resistance section as much as possible while ensuring that there are no defects such as cold shuts or insufficient pouring, from 30mm on one side to 15mm, in order to delay the pouring speed, extend the exhaust time, and prevent gas explosion and sand sticking caused by rapid pouring and untimely exhaust;
⑵ Increase the area of the internal gate for diversion. The number of internal gates increased from 3 gates of 30 mm x 3 mm to 4 gates of 45 mm x 3 mm, reducing the occurrence of sand flushing and sticking caused by small internal gate area, overheating of molten iron, and severe splashing turbulence during pouring;
⑶ Increase exhaust holes. Install an air outlet needle at the core head to prevent gas explosion and sand sticking caused by large gas generation and poor exhaust of the sand core; Add a drilling sand mold vent at the highest point of the clay sand casting, replacing the original one Φ 14 mm x 6 pieces, increased to the maximum limit Φ 18 mm x 8 pieces;
Increase the dust removal air volume, reduce the mud content and burning reduction of the molding sand. The mud content of molding sand has decreased from 12% to 14% to 10% to 12%; The reduction in burn volume has been controlled from 4.5% to 6% to 3.5% to 4.5%. Reduce the gas explosion and sand sticking caused by high mud content and burning reduction, as well as poor permeability of molding sand;
(5) Reduce water content and the amount of bentonite and coal powder added, reduce the compaction rate of molding sand, effective bentonite content, and volatile content. The moisture content of molding sand has decreased from 3.4% to 3.6%, and is controlled at 2.95% to 3.15%; The effective bentonite content has decreased from 7.5% to 9% to 7% to 7.5%; The volatile content has decreased from 2.0% to 2.5% to 1.8% to 2.0%. Reduce gas explosion and sand sticking caused by high moisture, effective soil, and coal powder content, as well as high gas generation of molding sand.
After taking improvement measures, the problem of sand sticking on the surface of clay sand castings has been improved, but it is unstable, sometimes good and sometimes bad, seriously affecting order delivery and quality assurance.
1. MAGMA analysis of the formation of gas explosion sand sticking defects in clay sand castings
In order to identify the root cause of severe gas explosion and sand sticking in the flywheel shell clay sand casting, and thoroughly solve this problem, it has been decided to conduct MAGMA simulation process analysis. Through simulation analysis of the flow direction, distribution, and accumulation of gas during the pouring process, the cause of gas explosion and solutions have been found.
1.1 Analysis of filling speed (Figure 9)
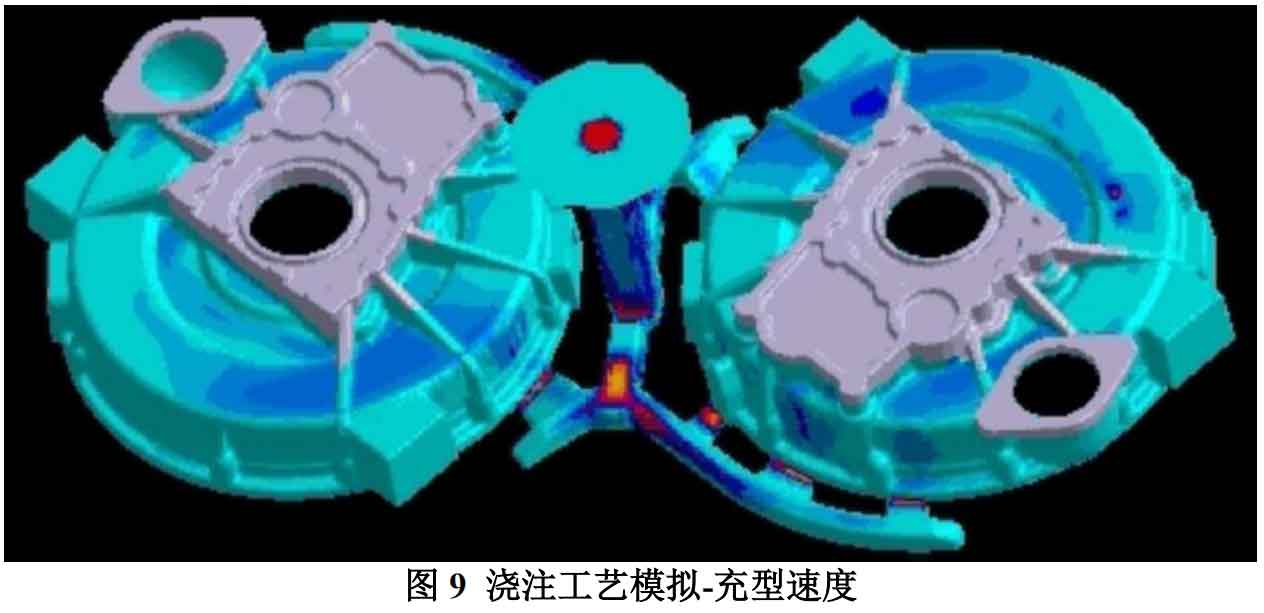
1.2 Analysis of Filling Temperature (Figure 10)
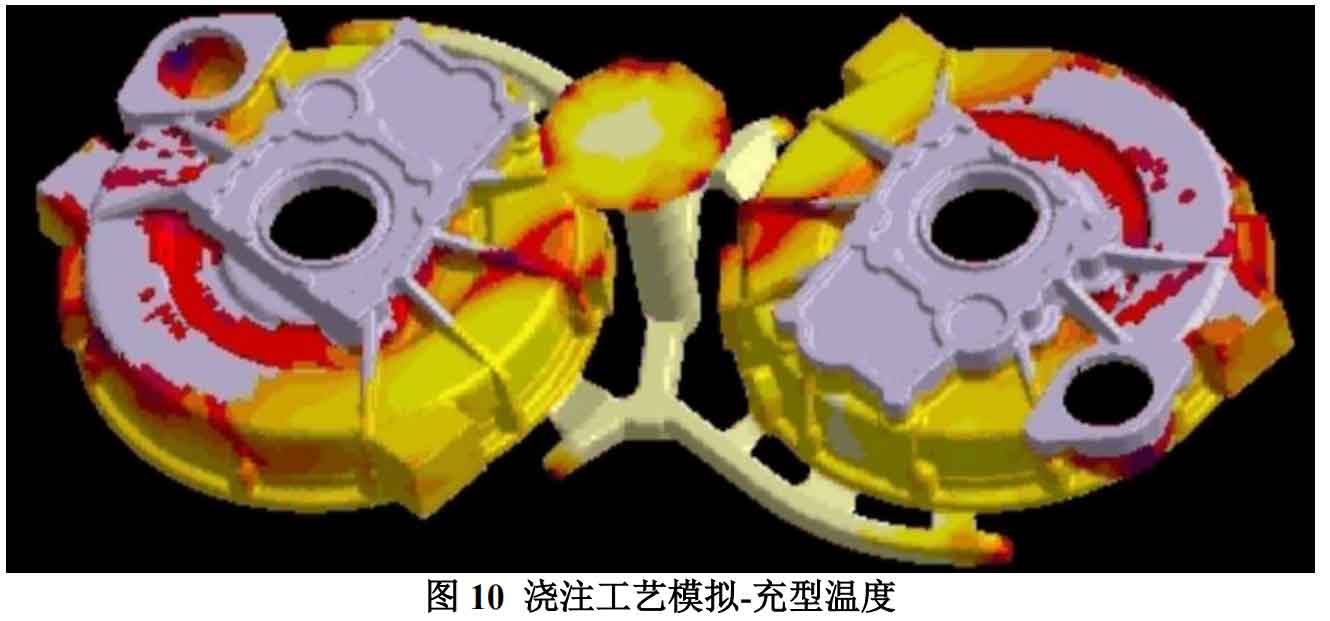
1.3 Analysis of Filling Pressure (Figure 11)
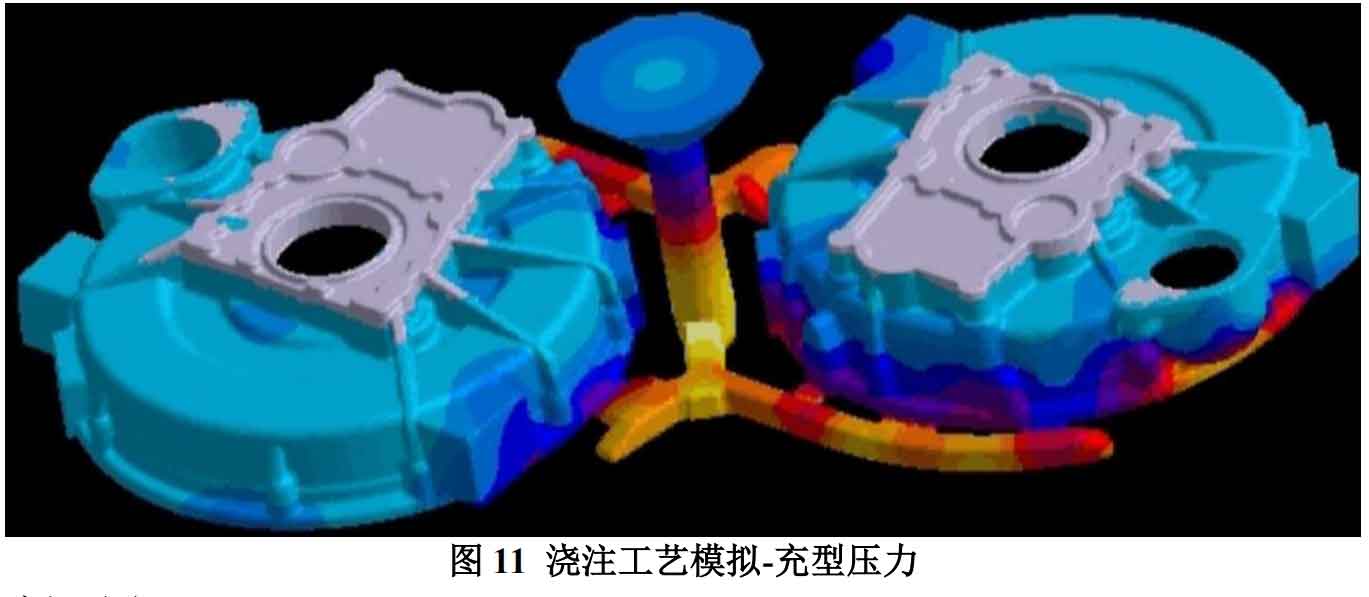
1.4 Analysis of Filling and Coiling (Figure 12)
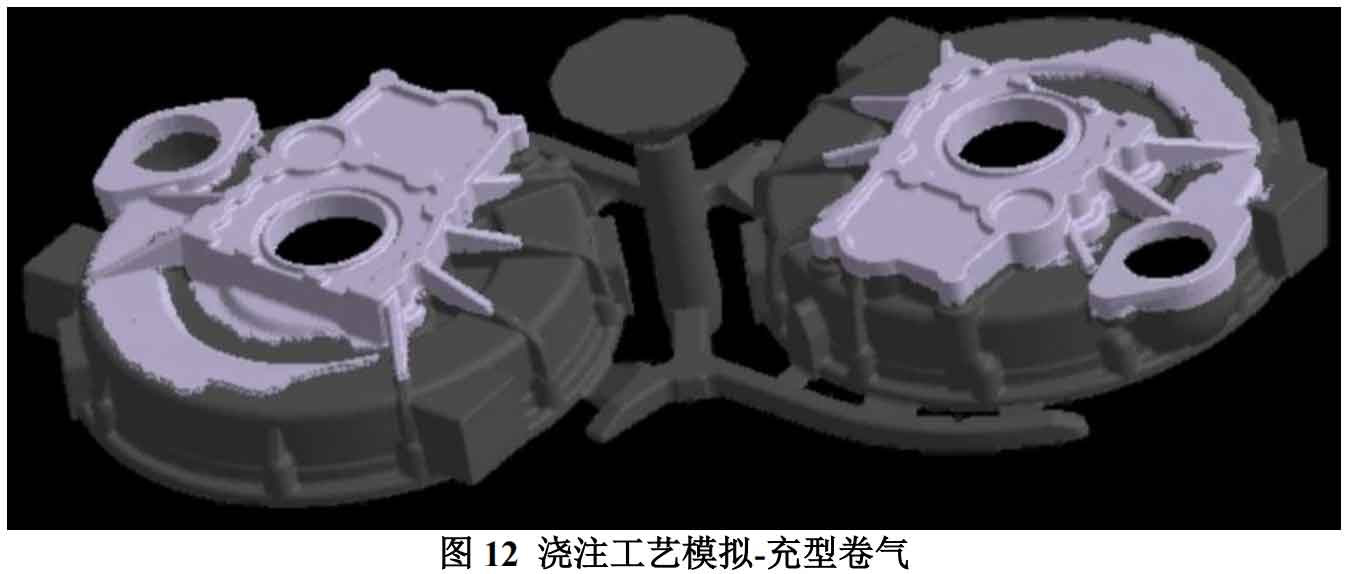
Through simulation analysis, it was found that the original mold casting process had uneven filling speed of molten iron and obvious local turbulence. The highest point of the clay sand casting had poor exhaust and severe air holding, which was the fundamental cause of severe air explosion and sand sticking in clay sand castings.
2. Verification of the effectiveness of new process improvements
Based on the problems identified through process simulation analysis, we have improved the mold process by adjusting the pouring system ratio to ensure smooth and uniform filling of molten iron; Improve the concave convex parting of the highest part and add an exhaust riser to facilitate smooth exhaust and prevent air stagnation (Figure 13, 14). After the improvement of the mold process, trial production verification was carried out, and the improvement effect was obvious. The surface of the clay sand casting was clean and tidy, and the problem of gas explosion and sand sticking was fundamentally eliminated (Figure 15, 16). It has now entered normal batch production.
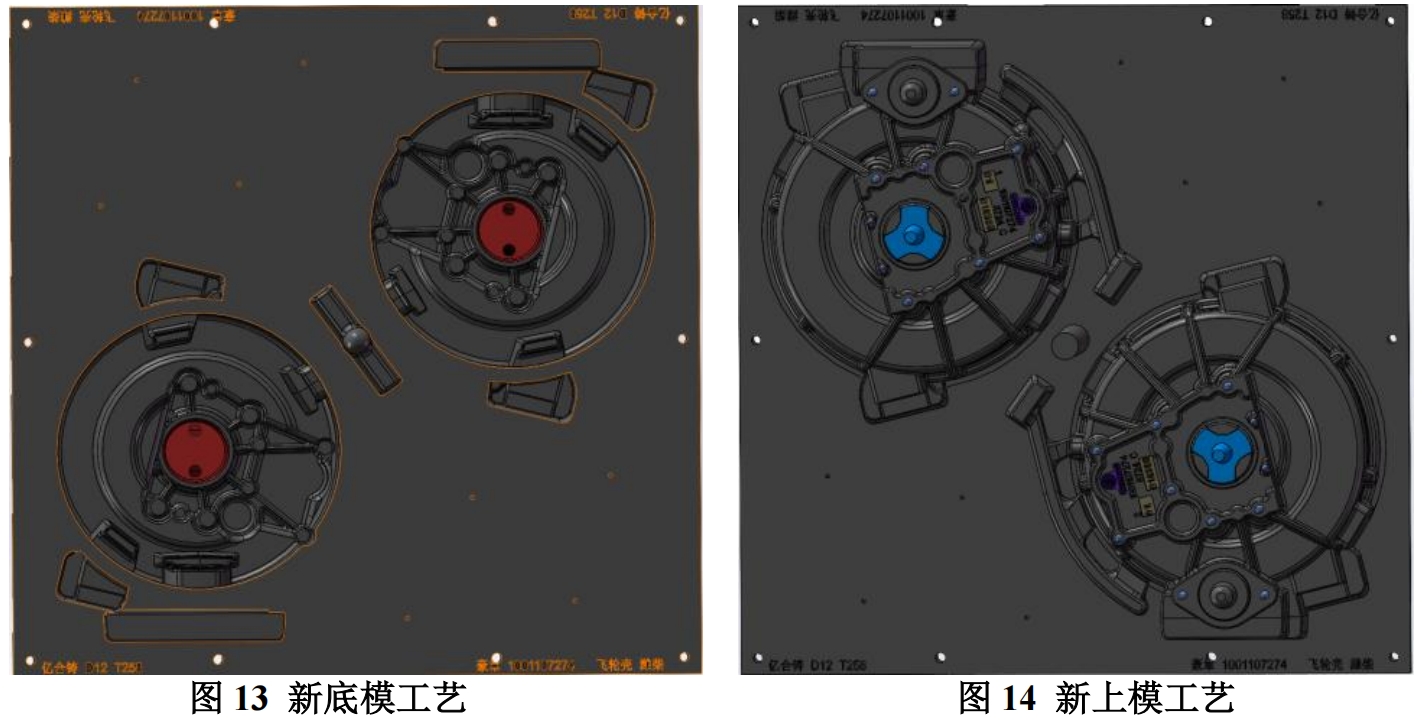
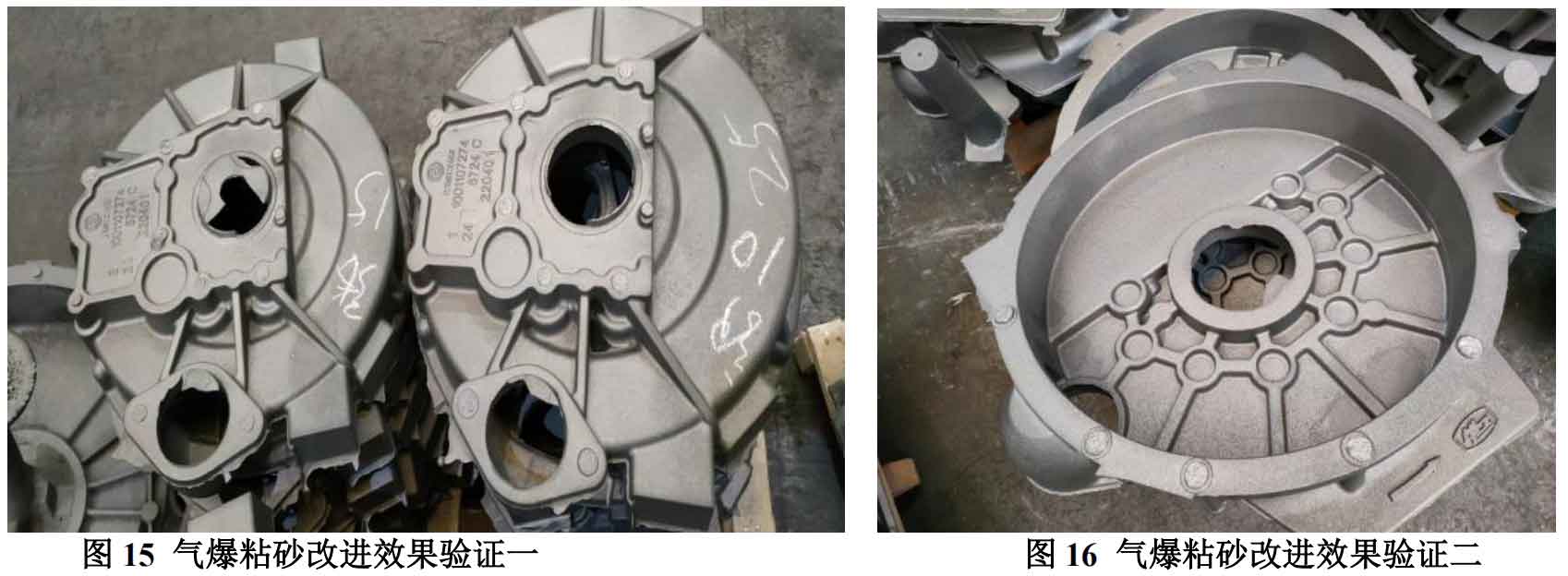
Drawing on the successful experience of MAGMA process analysis and improvement, corresponding improvement measures were also taken for the gas explosion and sand sticking problems in similar flywheel shells such as 8428 and 0415, and the results were verified to be good (Figure 17, 18, 19, 20).
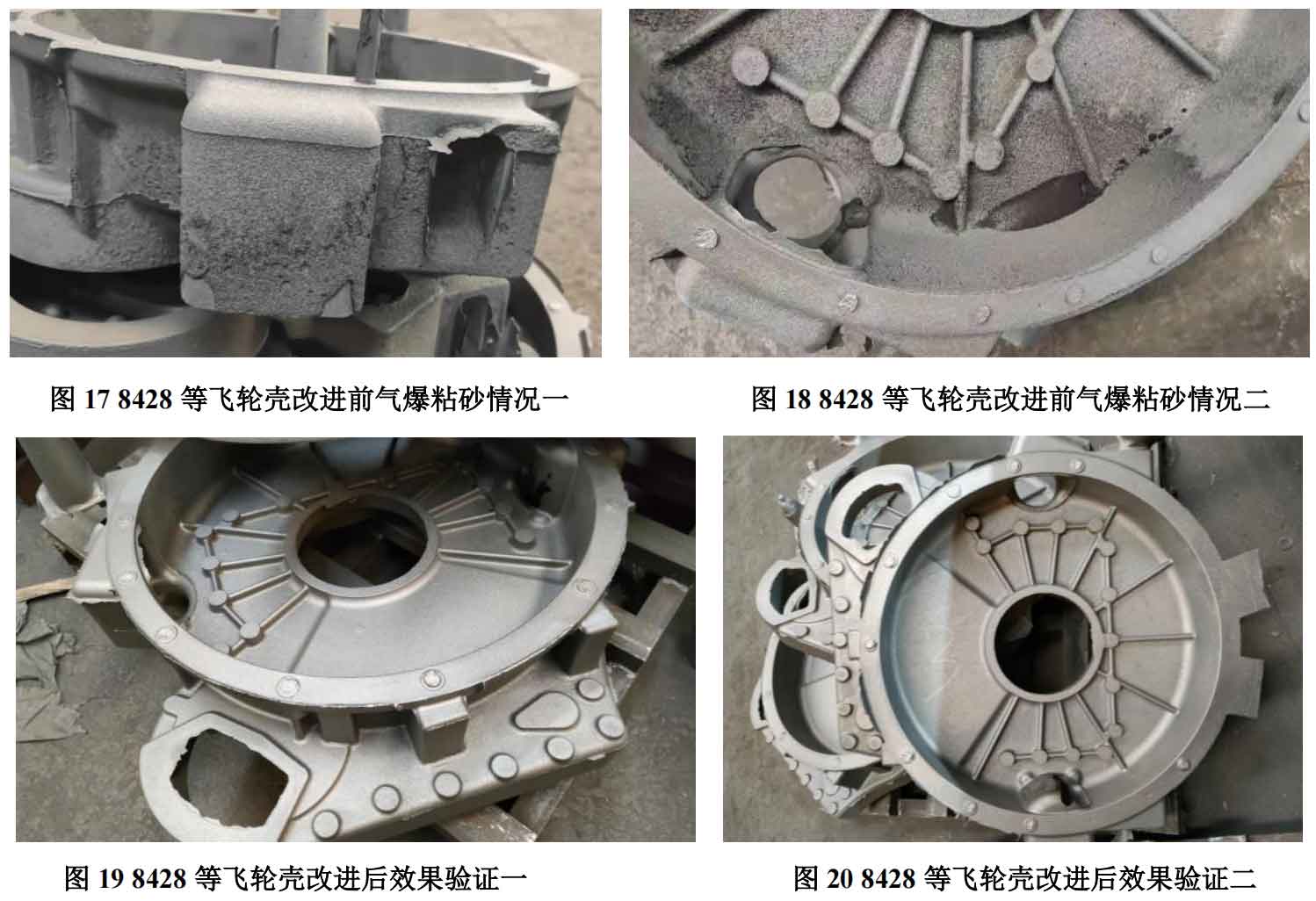
3. Conclusion
By using MAGMA software for simulation analysis of casting processes, deficiencies in casting process design can be identified in a timely manner, and improvement measures can be taken in a timely manner to avoid time and economic losses caused by problems in later clay sand casting trial production and further improvement. It is a powerful auxiliary tool for casting production and new product development, and is worth learning from and promoting.