Dual phase stainless steel refers to stainless steel with ferrite and austenite accounting for about 50% each, and generally requiring at least 30% of the lower phase content. Since its appearance in the United States in the 1940s, duplex stainless steel has developed to the third generation.
Its main feature is that the yield strength can reach 400-550 MPa, which is twice that of ordinary stainless steel, so it can save materials and reduce equipment manufacturing costs. In terms of corrosion resistance, especially in harsh media environments (such as seawater with high chloride ion content), the resistance of duplex stainless steel to pitting corrosion, crevice corrosion, stress corrosion, and corrosion fatigue is significantly better than ordinary austenitic stainless steel, and can be comparable to high alloy austenitic stainless steel.
Dual phase stainless steel contains high Cr, Ni, Mo, and N. According to ASTM A995/A995M Castings Austenitic Ferrite Duplex Stainless Steel statistics, Cr: 21.0%~27.0%; Ni: 4.0%~11.0%; Mo: 1.7%~5.0%; N: 0.10%~0.33%, castings are prone to formation σ Preventing cracks in castings is crucial. Cr is a key element, and higher chromium can increase strength and reduce ductility, increase ferrite, and promote σ The generation of phases keeps nitrogen in a solid solution state; Ni can increase austenite, toughness, ductility, and corrosion resistance, with a suitable target in the middle of the composition range; Mo can increase the corrosion resistance of chromium compounds, and the target value is more appropriate in the middle of the composition range. According to the chemical composition analysis (Table 1), higher chromium, suitable Ni and Mo are more suitable for producing such castings.
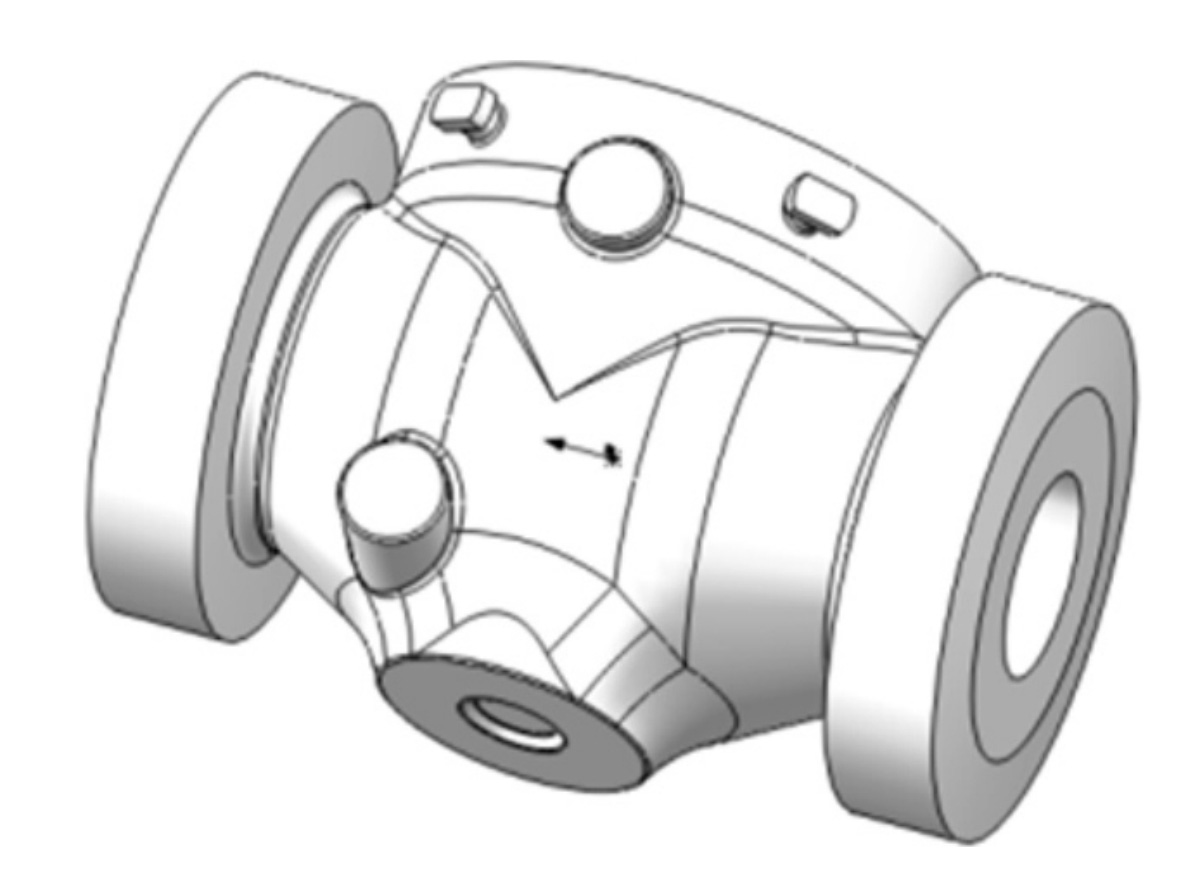
Sand casting manufacturers need to purchase 1500LBS valve bodies in bulk (Figure 1), made of duplex stainless steel A995-5A (Table 1), with a maximum casting thickness of 170mm and a rough weight of approximately 2200kg. Castings require strict PT (penetration testing), RT (radiographic testing), metallographic testing, ferrite testing, corrosion testing, hydrostatic testing, etc., with high quality requirements.
1. Examples of cracks and analysis of their causes
1.1 Examples of crack defects
The crack defects caused by the failure of cooling process control in pump castings are shown in Figure 2. Cracks and defects discovered during PT testing of castings: Sometimes during the production of dual phase steel castings, due to incomplete cooling process control, a certain proportion of cracks are produced during the cooling process σ Organized in this proportion σ The microstructure will not cause visible cracks, but there are already crack defects in the casting body. These crack defects can be found during PT, as shown in Figure 3, which is a typical example.
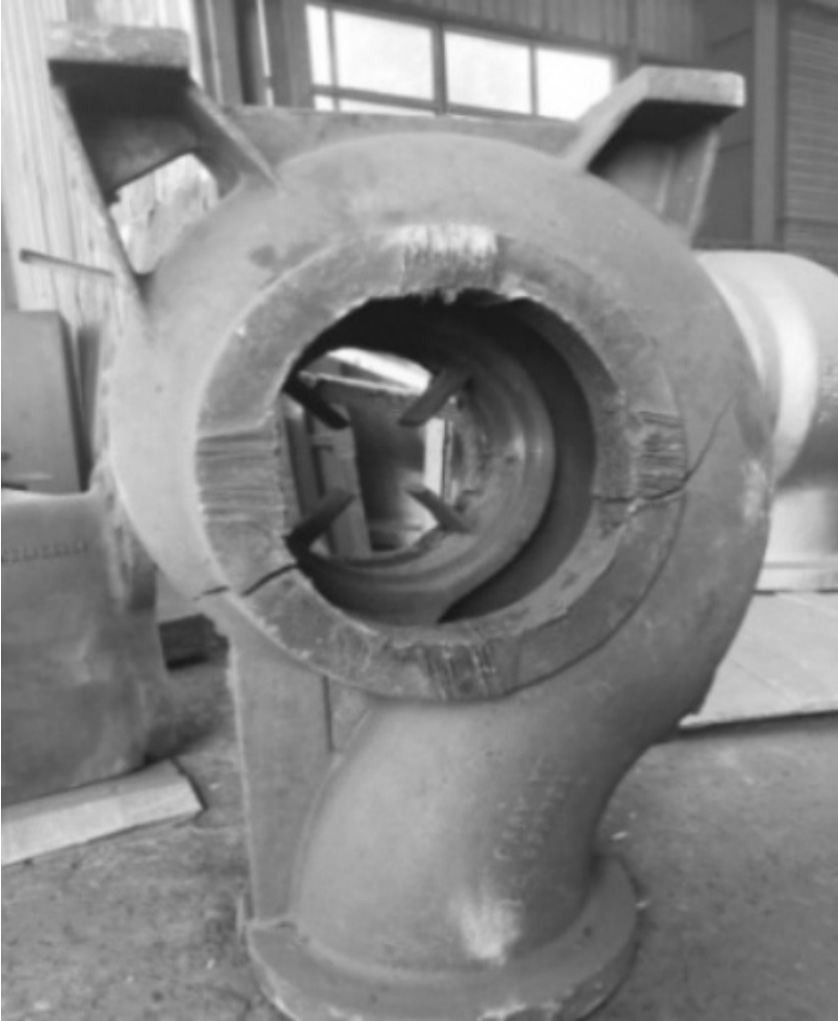
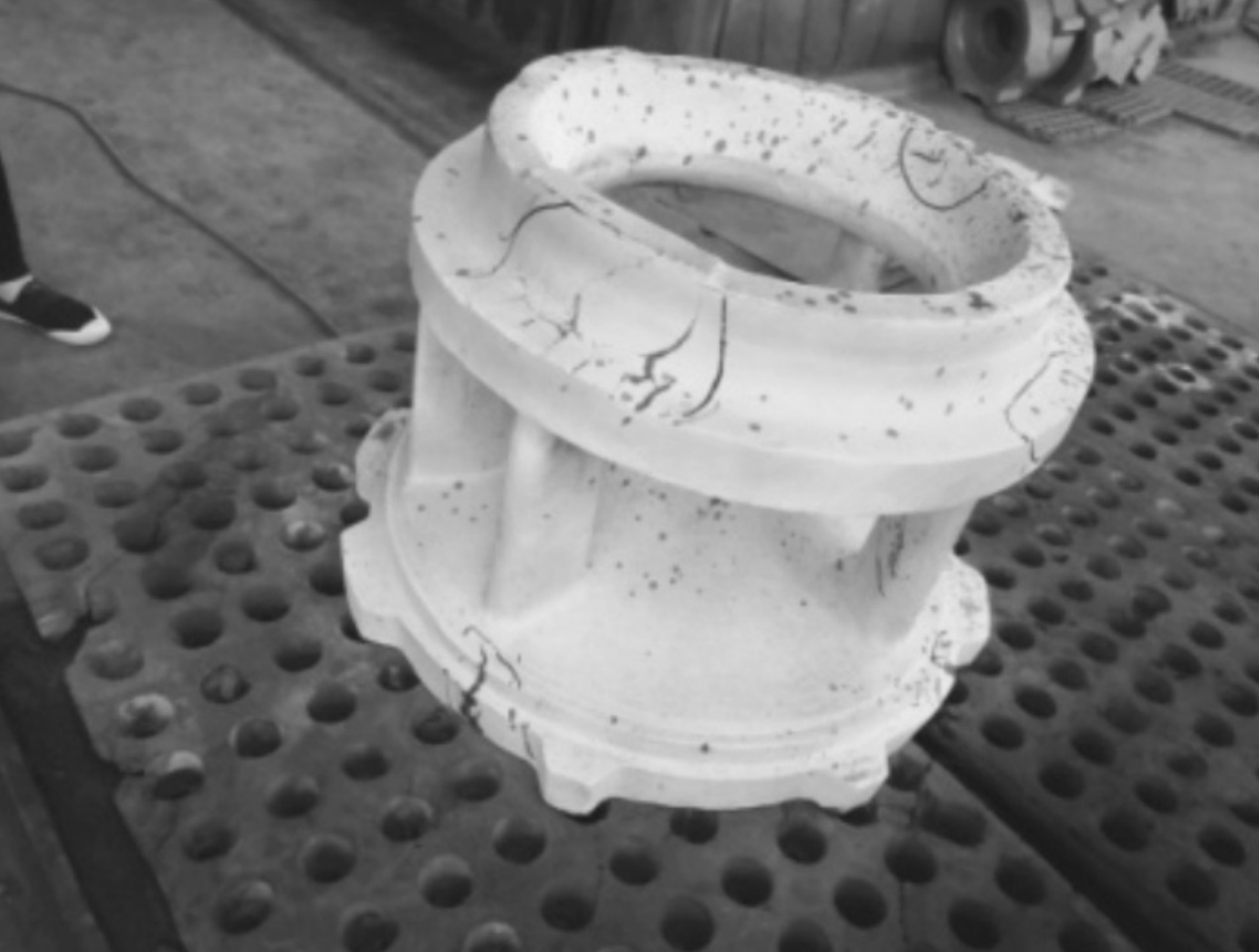
1.2 Analysis of the causes of crack defects in dual phase steel during cooling process
(1) Duplex stainless steel is prone to precipitate some brittle intermetallic compounds at 600-1000 ℃, especially those rich in Cr and Mo σ Xiang. σ Phase tendency occurs during the formation and processing of duplex stainless steel materials. Due to σ High phase hardness, high brittleness, and σ During the phase formation process, there is significant volume expansion, which leads to a decrease in the plasticity and toughness of the casting body, making it prone to cracking of the casting.
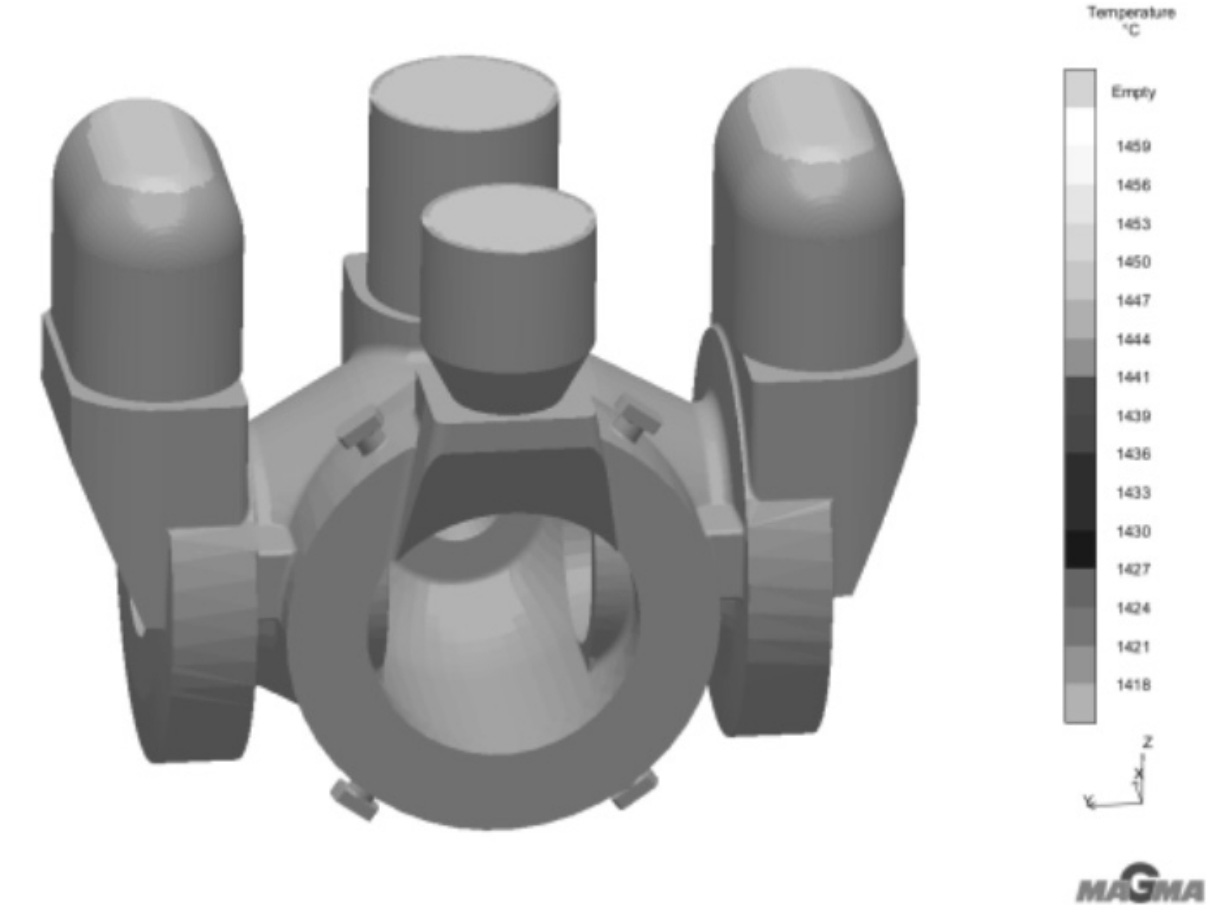
(2) High chromium ferritic austenitic duplex stainless steel also exhibits a tendency towards brittleness at 475 ℃. The brittleness is due to precipitation on the ferrite matrix σ Resulting from.
2. Take measures
2.1 Reduction σ Phase precipitation
Based on the analysis of the reasons for the formation of cracks in duplex stainless steel mentioned above, it is mainly necessary to reduce the temperature range of 600~1000 ℃ σ Phase precipitation requires controlling the brittleness at 475 ℃.
There are currently four effective methods for crack defects generated during the cooling process of castings, which are: direct water quenching after high-temperature boxing; Directly enter the furnace for heat treatment after high-temperature boxing; Cool to around 100-150 ℃ and heat treat in the furnace, then cut the pouring riser after heat treatment; Open the box at high temperature, and conduct forced air cooling or spray+forced air cooling on the casting after proper sand cleaning. Below is an analysis and explanation of the advantages and disadvantages of various methods.
2.1.1 Direct water quenching after high-temperature boxing
When the maximum riser on the casting has solidified, the casting is boxed. At this time, due to the short cooling process, the sand and core sand on the surface of the casting are not fully burned and dispersed, making it very difficult to remove the sand and core of the casting. Especially when the casting structure is complex and the sand core is thick, the temperature of the casting and core sand is also high. The sand and core sand cleaning cannot be very clean, and the cold iron cannot be removed. When entering the water, the temperature of the casting is generally above 900 ℃ (infrared thermometer can be used to measure the temperature of the casting surface), so as to quickly pass through the temperature range of 600~1000 ℃ and reduce the need for cleaning of sand and core sand σ The precipitation of phases also reduces brittleness at 475 ℃, avoiding cracks in castings.
The 1500LBS valve body castings produced by sand casting manufacturers were analyzed using Magma software. After pouring for 3 hours, 21 minutes, and 41 seconds, both the castings and the riser had solidified. At this time, the sand cleaning and water injection operation can be carried out.
This method has the following problems: ① Due to incomplete cleaning of castings, explosions of molding sand and core sand may occur when entering water, and cold iron may sometimes fly out, which is very dangerous and not suitable for mass production by enterprises; ② It is very difficult to clean at high temperatures, and workers find it difficult to accept such high-temperature operation methods, which can also lead to burns.
Due to the lack of security guarantees, the use of this method has now been eliminated; But for small precision castings or sand castings with simple structures, this method is also feasible.
2.1.2 Directly enter the furnace for heat treatment after high-temperature boxing
When the casting has solidified, it is boxed and directly heat treated after boxing. After the insulation time of the casting heat treatment is completed, when the casting cools down to 1045 ℃ with the furnace, it is quickly discharged from the furnace and directly subjected to quenching treatment. This method also has the problem of difficulty in high-temperature sand cleaning operation, as well as the explosion of molding sand and core sand when the casting is immersed in water. However, the explosion power is smaller and the danger is lower. Currently, this method is also prohibited. In addition, two issues need to be noted when directly entering the furnace for heat treatment after high-temperature boxing: ① The temperature at which the casting enters the furnace should be greater than 800 ℃; ② The temperature of the heat treatment furnace should be greater than 700 ℃; If these two points cannot be achieved, there is a high tendency for cracks to occur in the casting.
2.1.3 Cut the pouring riser after heat treatment
For castings with a thickness not exceeding 50 mm and relatively small thickness changes, the castings can be directly cooled to 100-150 ℃, and then heat treated in the furnace before cutting the sprue.
This method is not suitable for thick steel castings, such as castings produced by sand casting manufacturers with a thickness of 170 mm. Originally, the above method was used, but after cooling, no obvious cracks were found on the surface and riser visually. After heat treatment and cutting of the riser, the cracks were also not obvious visually. However, after processing, large cracks were found during PT, directly leading to the scrapping of the castings. Please refer to Figure 5 for details.
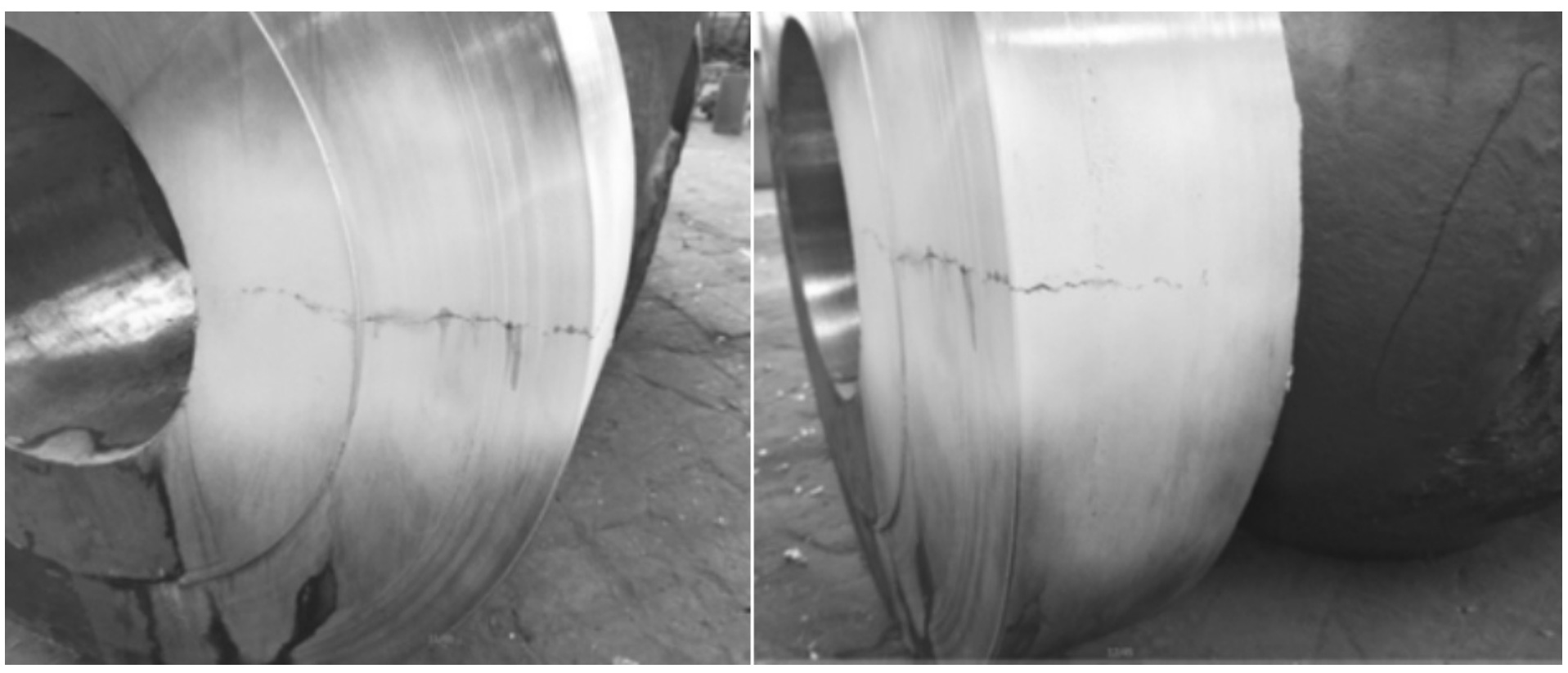
This method has the following problems: ① Due to the direct cooling of the casting to 100-150 ℃, there is a large amount of σ Due to its high brittleness, special care should be taken during sand cleaning. If the collision strength is high, the casting may be scrapped due to cracks; ② When conducting heat treatment on castings, the heating rate should be specially controlled, and the heating process should also be adjusted. It is not possible to uniformly heat up to the insulation temperature at once; ③ Due to the fact that castings need to be insulated to 100-150 ℃ after casting, the insulation time is longer, especially in summer, which leads to a significant extension of the production cycle and long-term occupation of factories and sand boxes, affecting the normal production arrangement of the enterprise This method is not suitable for thick and large castings.
2.1.4 Forced air cooling or spray after sand cleaning
The castings shall be forced air cooling or spray after proper sand cleaning after high temperature boxing (Fig. 6). The 1500LBS valve body castings produced by sand casting manufacturers are simulated using Magma software. After 2 hours, 58 minutes, and 5 seconds of pouring, the castings have all solidified. At this time, the sand cleaning operation can be carried out. After appropriate sand cleaning, the castings are forced to cool with two fans. After the air cooling reaches an appropriate temperature range, the pouring and riser can be directly cut. This method can avoid crack defects in duplex stainless steel castings, is easy to operate, and is suitable for mass production by sand casting manufacturers. The casting is 170 mm thick, which is a thick steel casting. If the casting thickness is further increased, a fan with spray can be selected for forced cooling, which can also avoid crack defects. During the use of this method, attention should be paid to aligning the thicker part of the casting with the air outlet of the fan as much as possible. If the casting is placed on the frame for air cooling, the effect will be better.
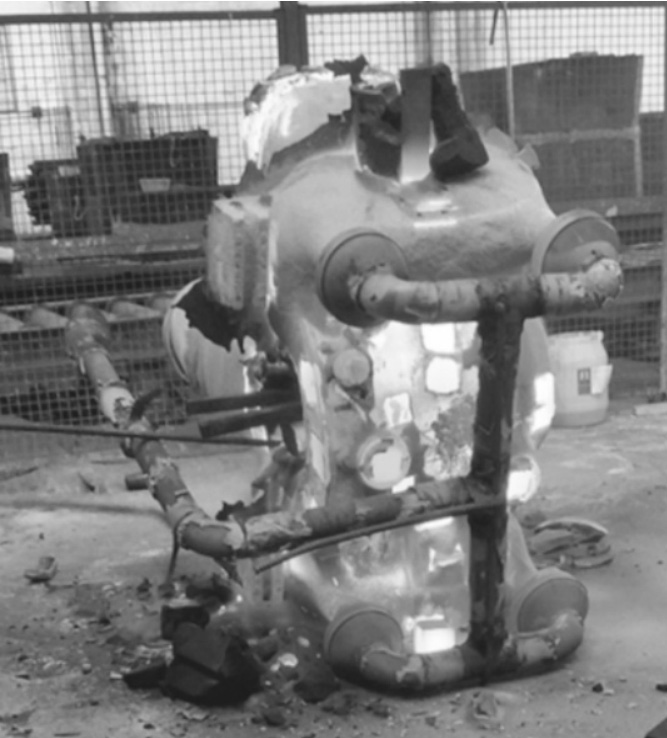
3. Conclusion
(1) For duplex stainless steel A995-5A castings, forced air cooling after high-temperature boxing is a good method to avoid crack defects during the cooling process, especially for thick and large parts, which has a significant effect. According to this cooling plan, there are no visual crack defects, and the cracks found by the final PT of the casting are also very few. There are very few crack defects in the casting during the processing, and the quality of the casting is very stable.
(2) The use of high-temperature box making for direct water quenching or high-temperature box making for solid solution treatment can solve the problem of cracks in castings. However, this method poses significant safety hazards and labor intensity during the production process, making it unsuitable for mass production by sand casting manufacturers.
(3) Cooling the castings to room temperature before heat treatment is also feasible for some castings, but the requirements for the heat treatment process are relatively strict, suitable for sand castings with simple structures or small precision castings. The heat treatment process must strictly control the heating rate.