Due to its advantages of high strength, high hardness, and good plasticity toughness matching, high manganese wear-resistant lining plates have always been one of the main raw materials for wear-resistant lining plates in rock crushers. The service process of wear-resistant lining plates requires bearing severe friction and strong impact loads, with high consumption. Its service life has become the main factor affecting the crushing cost and construction efficiency. How to develop high manganese steel wear-resistant lining plates that are suitable for harsh service conditions and have excellent wear resistance has become one of the key core technologies in the field of rock crushers.
Regarding the research and development of high manganese wear-resistant lining plates for crushers and the improvement of wear performance, domestic scientific and technological workers have carried out a series of research work from different perspectives, mainly involving the optimization of wear-resistant high manganese steel alloy composition, microstructure and performance control, and the study of wear resistance mechanism. Peng Shiguang et al. developed a lightweight high manganese steel wear-resistant lining material, alloy composition system, and preparation process for cone crushers based on the design concept of high strength, high hardness, high toughness, and low density. They also conducted systematic research on the microstructure control and wear mechanism of the developed material; Tu Bin et al. studied the preparation process and microstructure properties of ultra-high manganese steel wear-resistant lining plates, and systematically studied the influence of heat treatment processes such as tempering and water toughening on the microstructure and mechanical properties of high manganese steel; Yan Xiaobo et al. studied the influence of modified alloy elements such as V and Ti on the microstructure and mechanical properties of high manganese steel, and further combined the microstructure characteristics to study the wear weight loss law of modified high manganese steel under different impact loads; In addition, Ouyang Zhengrong et al. discussed the plastic deformation mechanism and application analysis of high manganese steel, and explored the fundamental reasons for its excellent mechanical properties. Song Renbo et al. combined with the variation law of stacking fault energy, studied the deformation mechanism of high manganese steel under compression conditions.
In summary, domestic researchers have achieved relevant research results in the modification of high manganese wear-resistant lining plate alloy composition, control mechanism of microstructure and properties, and wear behavior law of high manganese wear-resistant lining plate. Due to technical confidentiality and other reasons, there have been no reports on the research and development of high manganese wear-resistant lining plates for rock crushers abroad. There are almost no reports on the deformation hardening behavior of high manganese wear-resistant lining plates under dynamic loads in the reported research on the development and wear mechanism of high manganese wear-resistant lining plates. The main reason for this lies in the limitations of experimental technology. Simulating the strong impact and severe friction during the service process of the lining plate has become a bottleneck in studying the mechanical behavior of high manganese wear-resistant lining plates under dynamic loads. Clarifying the mechanical behavior laws of high manganese wear-resistant cast steel under dynamic loads, especially the strain hardening laws, is of great theoretical research significance for a deeper understanding of the plastic deformation behavior and the metallurgical essence of wear resistance behavior of high manganese wear-resistant lining plate alloys.
Based on this, a typical high manganese wear-resistant cast steel component used for the wear-resistant lining plate of a rock crusher is taken as the research object, and a systematic study is carried out on the deformation hardening behavior of the high manganese wear-resistant lining plate under dynamic load using the mechanical field separated Hopkinson compression bar (SHPB) technology. In order to clarify the strain hardening law of high manganese wear-resistant lining plates under different dynamic loads, obtain the quantitative relationship between strain hardening behavior and dynamic loads, and provide experimental and theoretical references for the optimization of alloy composition and reasonable material selection of high manganese steel wear-resistant lining plates in crushers.
C | Si | Mn | Cr+Mo | P | S |
0.12~0.16 | 0.2~0.4 | 12.5~13.5 | 3.8~4.2 | <0.004 | <0.002 |
This study focuses on the typical high manganese wear-resistant lining plate Mn13Cr2Mo, and its specific alloy composition is shown in the table. Among them, the Mn content is about 12.5%, and the Cr and Mo content are about 2.8% and 1.4%, respectively. Mn is a stabilizing element for austenite, which not only stabilizes the austenite structure in the alloy, but also solidly dissolves in the alloy matrix by replacing atoms, playing a role in solid solution strengthening; Cr and Mo are both carbide forming elements that interact with carbon atoms to form M23C6 and MC type metal compounds. The above alloy composition design characteristics ensure that this type of alloy has good wear resistance potential.
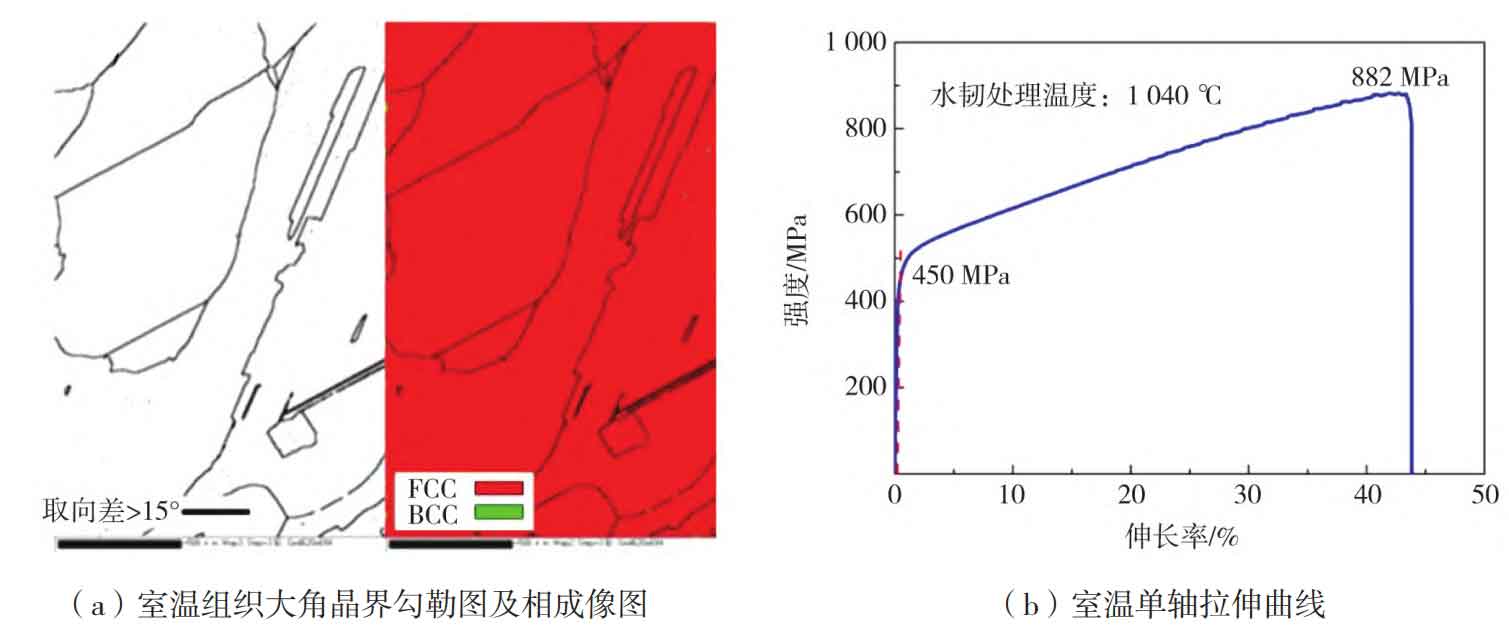
The experimental Mn13Cr2Mo wear-resistant lining plate was subjected to water toughening treatment at 1040 ℃ for 2 hours and used for subsequent SHPB tests. Figure 1 shows the large angle grain boundaries and phase imaging of Mn13Cr2Mo wear-resistant lining plate after water toughening treatment, as well as the uniaxial static tensile curve at room temperature. As shown in the figure, the room temperature microstructure of Mn13Cr2Mo used in the experiment is mainly composed of austenite with a face centered cubic (fcc) crystal structure, with an average austenite grain size of about 420 μ m. See Figure 1a. The room temperature yield strength (Rp0.2) of Mn13Cr2Mo used in the experiment is about 450 MPa, the tensile strength is about 882 MPa, and the elongation after fracture is about 49.6%, indicating that the alloy has good strength and plasticity matching under static tensile load, as shown in Figure 1b.
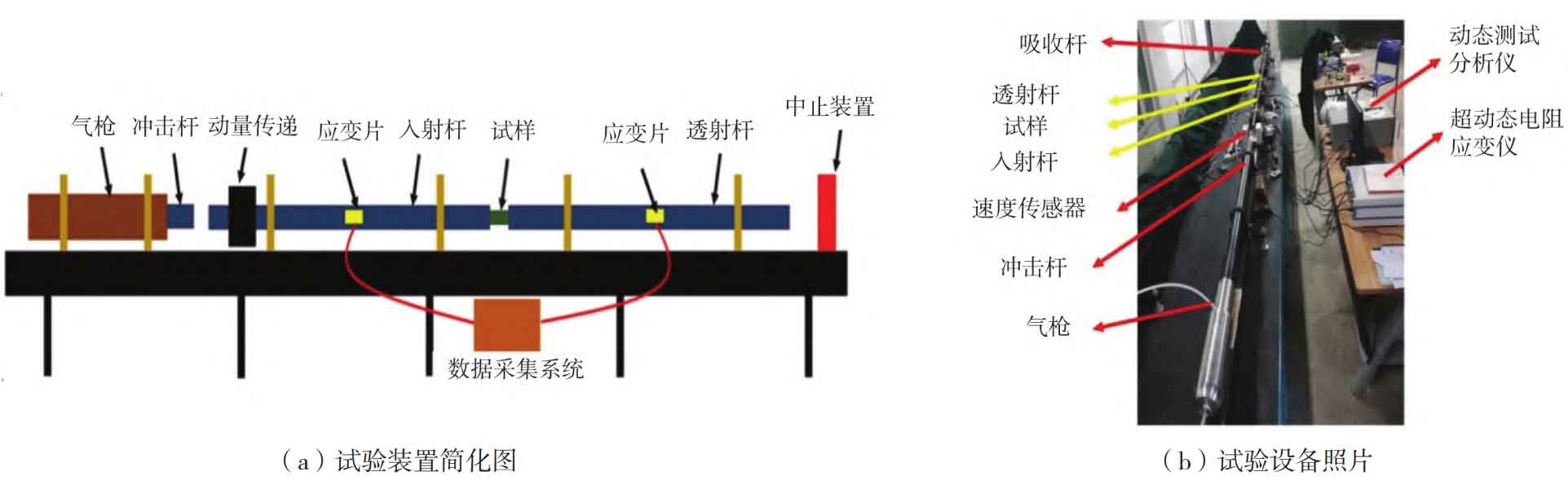
In order to systematically study the deformation hardening behavior of high manganese wear-resistant lining plate Mn13Cr2Mo under dynamic load, SHPB apparatus was used for the experiment. The working principle of SHPB is shown in Figure 2. The device mainly consists of a cylinder, an impact rod, an incident rod, and a transmission rod. High precision resistance strain gauges are placed at the incident rod and transmission rod to collect signals such as incident waves, reflected waves, and transmitted waves, in order to analyze the deformation behavior of alloys under different cylinder pressures. In this study, stress states under different impact loads were simulated by controlling the size of cylinder pressure. The cylinder pressures were selected as 0.2 MPa, 0.4 MPa, 0.6 MPa, and 0.8 MPa, respectively. The sample size used for SHPB testing is Φ A cylindrical specimen with a diameter of 6 mm x 7 mm. After the impact test, use transmission electron microscopy to analyze the microstructure of the samples obtained under different impact loads. After mechanical polishing, the sample is prepared into a thickness of 40 μ The thin slice sample of m was subjected to punching and double spraying (double spraying solution of 8% perchloric acid ethanol solution, double spraying temperature -30 ℃) for transmission observation. The transmission test was conducted on a Tecnai G2 F20 transmission electron microscope.