The sand casting process is a manufacturing method that has been practiced for centuries and continues to be widely used today. It is a unique combination of traditional craftsmanship and modern technological advancements. Here’s how the sand casting process balances tradition and technology:
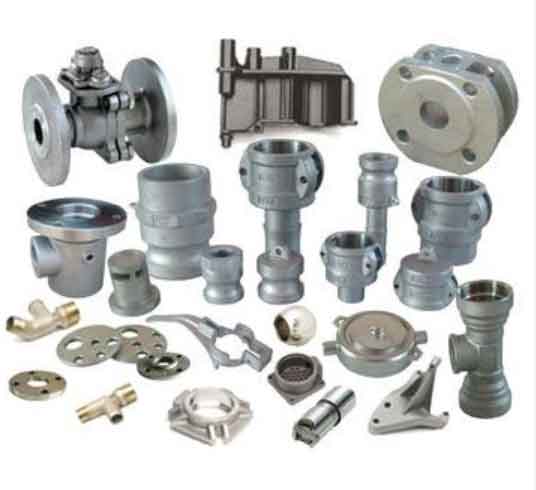
- Traditional Craftsmanship: Sand casting has a rich history and is rooted in traditional craftsmanship. Skilled craftsmen with extensive knowledge and experience in pattern making, mold preparation, and casting techniques play a crucial role in the process. Their expertise ensures the production of high-quality castings with intricate details and complex shapes.
- Pattern Making: Pattern making is a traditional aspect of sand casting that requires craftsmanship and precision. Patterns are typically made from wood, plastic, or metal and serve as the templates for creating molds. Pattern makers use their skills to create accurate and detailed patterns that capture the desired shape and features of the final casting.
- Mold Preparation: The process of preparing molds involves traditional techniques such as ramming sand around the pattern and creating gating and riser systems. Skilled molders employ their expertise to achieve proper compaction of the sand, ensuring good mold strength and dimensional accuracy.
- Technological Advancements: While the core principles of sand casting remain the same, technological advancements have greatly enhanced the efficiency and precision of the process. Computer-aided design (CAD) software is used to create digital models of patterns, allowing for precise geometry and complex shapes. This digital information can be directly translated to computer-aided manufacturing (CAM) systems for automated pattern production.
- Simulation and Virtual Prototyping: Advanced simulation software is used to predict and optimize the casting process before physical production. This includes analyzing mold filling, solidification, and cooling to identify potential defects and optimize process parameters. Virtual prototyping helps reduce time and costs by identifying potential issues and optimizing designs early in the process.
- 3D Printing and Rapid Prototyping: 3D printing and rapid prototyping technologies have revolutionized pattern making in sand casting. Instead of traditional pattern production, 3D printing allows for the direct production of complex patterns from digital designs. This enables faster prototyping, reduces pattern production time, and offers greater design flexibility.
- Process Automation: Automation has been introduced to various stages of the sand casting process, enhancing efficiency and consistency. Automated systems are used for sand mixing, mold compaction, and shakeout processes, reducing manual labor and improving productivity. Robotic systems can also be employed for tasks such as mold handling and pouring.
- Quality Control: Technology has significantly improved quality control in sand casting. Advanced inspection techniques such as 3D scanning, X-ray, and CT scanning can be used to ensure dimensional accuracy and detect internal defects in castings. This enables thorough quality assessment, reduces rework, and enhances overall casting quality.
By balancing traditional craftsmanship with technological advancements, the sand casting process combines the best of both worlds. It retains the artistry and expertise of skilled craftsmen while benefiting from the precision, efficiency, and quality control offered by modern technology. This balance allows for the production of high-quality castings with complex geometries and meets the demands of modern manufacturing.