This article focuses on the design of the evaporative pattern casting process for ductile iron castings and the prevention of common shrinkage defects. Through structural analysis, process scheme design and simulation, process experiments, defect analysis, and improvement measures, a reasonable casting process is determined to improve the quality of ductile iron castings. The key is to select the appropriate pouring system and riser, and strengthen the control of the whole process.
1. Introduction
Ductile iron castings are widely used in various fields due to their excellent mechanical properties. However, in the evaporative pattern casting process, problems such as shrinkage porosity and shrinkage holes are prone to occur, which seriously affect the quality of castings. Therefore, it is necessary to conduct in-depth research on the casting process to improve the casting qualification rate.
2. Casting Structure Analysis
The ductile iron casting studied in this paper has a material of QT400 – 15, a contour size of 430mm×620mm×684mm, and a weight of 180kg. There are thick-walled areas in many parts of the casting. For example, an area with a size of 183mm×40mm×59mm is prone to shrinkage holes. In addition, there are two oil passages with a total length of 510mm, and the airtight leak detection pressure requirement is high, and no defects are allowed inside the oil passages.
Casting Information | Details |
---|---|
Material | QT400 – 15 |
Contour Size | 430mm×620mm×684mm |
Weight | 180kg |
Key Thick-walled Area Size | 183mm×40mm×59mm |
Oil Passage Total Length | 510mm |
3. Process Scheme Design and Simulation
3.1 Pouring System Design
Four pouring system schemes are designed: side-bottom injection, top injection, step injection, and bottom injection.
- Side-bottom injection: In the solidification process, thinner regions solidify first, and thick regions take longer to solidify. The intersection area of the parallel plate and the upper end face has a higher shrinkage porosity risk level. There is also a shrinkage porosity risk in the “U” – shaped boss on both sides of the casting and the dense area at the bottom.
- Top injection: The areas with a higher shrinkage porosity risk level are similar to those of the side-bottom injection scheme.
- Step injection: The shrinkage porosity risk areas are concentrated in the interior of the “U” – shaped bosses on both sides of the casting and the intersection area of the parallel plate and the upper end face. After the ingate solidifies, the upper end face cannot be fed.
- Bottom injection: During solidification, the hot spot area on the upper end face is fed by the riser, but before the feeding channel is closed, the feeding is not completed, resulting in shrinkage porosity or shrinkage holes in the hot spot area on the upper end face and inside the riser.
3.2 Simulation Results Comparison
Pouring System Scheme | Shrinkage Porosity Risk Areas | Problems |
---|---|---|
Side-bottom injection | Intersection of parallel plate and upper end face, “U” – shaped boss on both sides, bottom dense area | Small slag collection package has little effect on solidification process of upper end face, and slag collection effect needs experimental verification |
Top injection | Similar to side-bottom injection | – |
Step injection | Interior of “U” – shaped bosses on both sides, intersection of parallel plate and upper end face | Upper end face cannot be fed after ingate solidifies |
Bottom injection | Upper end face hot spot area and riser interior | Feeding is not completed before feeding channel is closed |
4. Process Experiment
Based on the analysis of the MAGMA simulation results, the bottom injection pouring system with a riser is selected for the process experiment.
5. Defect Analysis
5.1 Main Defects
There are shrinkage holes on the upper end face of the casting without a feeding riser, and the positions are concentrated at the intersection of the parallel plate structure and the upper end face.
5.2 Cause Analysis
5.2.1 Shrinkage Hole Formation Mechanism
During the solidification process of the casting, the thick region solidifies more slowly than the surrounding uniform thin-walled region. After the surrounding region solidifies, the solidification process in the thick region cannot be supplemented by the molten iron, resulting in shrinkage porosity or shrinkage hole defects. In the solidification process of ductile iron, there is no hard shell formed on the surface in the initial stage. With the precipitation of graphite, the eutectic expansion pressure will cause two phenomena: one is that the volume of the molten iron increases, the solidification range expands continuously with time, and the last solidified region forms shrinkage holes or shrinkage porosity. The volume shrinkage during the cooling process cannot change the formed shrinkage porosity or shrinkage hole defects, and may even increase the risk of shrinkage porosity; the second is that the expansion pressure directly acts on the surface of the mold, causing adverse phenomena such as mold wall migration, box expansion, and shrinkage porosity.
5.2.2 Role of Risers
In this experiment, the risers are divided into slag collection risers and feeding risers according to their uses. The feeding riser is mainly used to solve the shrinkage porosity defect, and its functions are to supplement the molten iron and control the pressure. There are three typical stages of pressure change in the riser: after the ingate solidifies, no more molten iron enters the mold, and the casting and the riser form a whole; when the liquid metal shrinks to the limit state, the pressure in the riser in the mold is the smallest; with the precipitation of graphite and the formation of austenite, the liquid metal expands, making the riser full again.
6. Improvement Scheme
6.1 Improvement of Riser Parameters
The modulus of the hot spot area of the casting is , the modulus of the riser is , and the modulus of the riser neck is . Referring to the design principle of the riser in the traditional sand casting process, two types of risers are set: for 1# riser, , ; for 2# riser, , . Except for the different sizes of the risers, the other controllable parameters are exactly the same. The two types of risers are respectively tested in the whole process, and process improvements such as anti-collision, anti-deformation, and pre-sand filling treatment are added to verify the improvement effect of different risers on the shrinkage holes in the hot spot position of the casting.
6.2 Improvement Effect
When the evaporative pattern casting selects the bottom injection and 1# riser pouring system, there are shrinkage hole defects in the hot spot area after the casting is roughly turned (inside the circle in Figure 9), and the rejection rate reaches 37%. When the evaporative pattern casting selects the bottom injection and 2# riser pouring system, there are no obvious defects on the upper end face of the casting after rough turning, and there is no shrinkage porosity defect in the hot spot area. There are discrete small point defects on the end face. After tracking and verification, the defects on the end face of the part are removed after the whole process processing.
7. Conclusion
- The pouring process of ductile iron castings in evaporative pattern casting should select the bottom injection and a riser matching the size of the evaporative pattern casting, and conduct comparative experiments combined with the product structure to obtain the best solution to solve the shrinkage porosity defect.
- After determining the pouring system of ductile iron castings in evaporative pattern casting, it is necessary to strengthen the control of the whole process, prevent collisions, and control various links such as coating drying, pouring negative pressure, and pressure maintaining, which is beneficial to improving the internal and external quality of the castings.
In the actual production process, continuous optimization and improvement should be carried out according to the specific situation of the castings to ensure the quality and performance of the ductile iron castings. At the same time, more advanced simulation software and testing methods can be introduced to improve the efficiency and accuracy of the research.
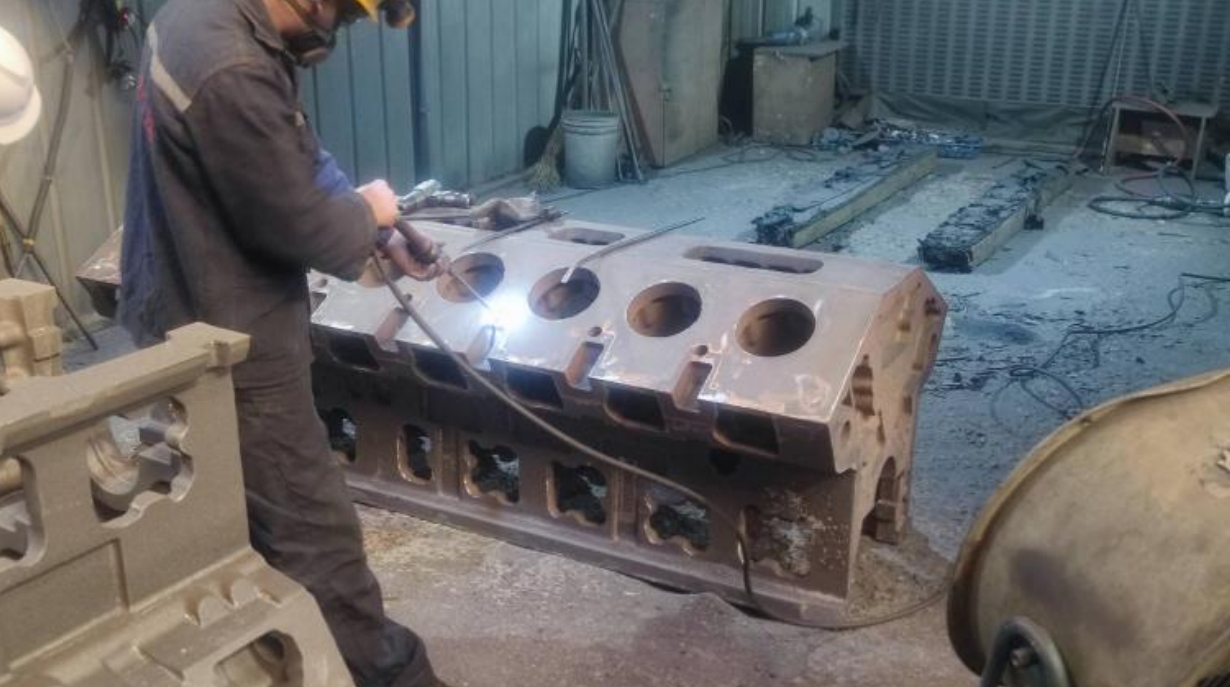