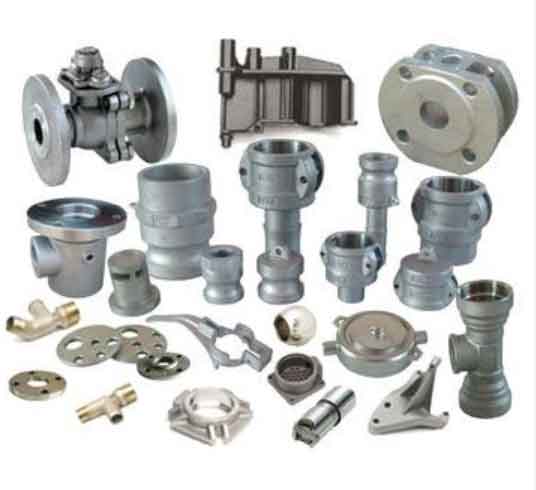
Designing a part for sand casting involves several considerations to ensure a successful and efficient casting process. Here are some key design considerations for sand casting projects:
- Draft angles: Incorporate draft angles on vertical surfaces to facilitate the removal of the pattern from the mold. A minimum draft angle of 1-2 degrees is typically recommended to prevent sticking and damage to the mold.
- Parting line and parting surfaces: Determine the parting line, which separates the mold into two halves. Minimize the complexity of parting surfaces to ease mold assembly and reduce costs. Avoid sharp corners and complex parting line geometries that can complicate the molding process.
- Wall thickness: Maintain uniform wall thickness throughout the part to promote solidification and minimize the risk of defects such as porosity and shrinkage. Avoid sudden transitions in wall thickness to ensure consistent cooling and prevent casting defects.
- Fillet and radius design: Incorporate fillets and generous radii at sharp corners and transitions to improve the flow of molten metal and reduce stress concentration points. Smooth transitions minimize the risk of casting defects and improve the overall strength of the part.
- Undercuts and features: Minimize undercuts and complex internal features that can impede the removal of the pattern and complicate the molding process. Consider incorporating cores or slides to accommodate necessary features and ensure successful casting.
- Gating and risering: Design appropriate gating and risering systems to facilitate the flow of molten metal, minimize turbulence, and promote even solidification. Properly positioned gates and risers help reduce the risk of casting defects, such as misruns and cold shuts.
- Pattern design: Create a robust pattern that can withstand the molding and casting processes. Use suitable materials for patterns, such as wood, metal, or plastic, depending on the expected production volume and complexity of the part.
- Machining allowances: Incorporate sufficient machining allowances to achieve the desired final dimensions and surface finish. Consider the shrinkage of the material during solidification and cooling when determining machining allowances.
- Material selection: Choose a suitable casting material based on the application requirements, including mechanical properties, corrosion resistance, and temperature resistance. Consult with material specialists or foundries to select the optimal material for your specific needs.
- Communication with foundry: Collaborate closely with the foundry throughout the design process. Seek their expertise and input to ensure the design is suitable for sand casting and can be efficiently produced.
By considering these design considerations, you can optimize your sand casting project for successful production, improved quality, and cost-effectiveness. Consulting with experienced design engineers and collaborating with the foundry can provide valuable insights and ensure a smooth transition from design to casting.