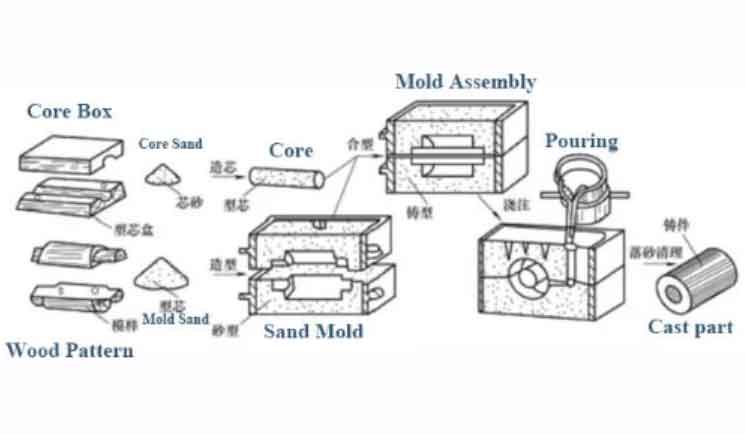
Sand casting is a widely used method for manufacturing metal parts. It offers several advantages, including cost-effectiveness, flexibility in design, and the ability to produce complex shapes. Sand casting allows for the production of both small and large components, making it suitable for a wide range of applications.
The process of sand casting involves creating a mold made of sand, into which molten metal is poured. The sand mold is typically formed by packing sand around a pattern, which is a replica of the desired part. Once the metal solidifies, the mold is removed, and the finished part is obtained.
Sand casting bridges the gap between design and production in several ways:
- Design Flexibility: Sand casting allows for great design flexibility. The sand molds can be easily customized to accommodate complex shapes, undercuts, and intricate details. This flexibility enables designers to create parts with creative and functional features.
- Prototyping: Sand casting is an excellent method for prototyping. It allows designers to quickly produce a physical model of their design, enabling them to evaluate its form, fit, and function. Prototyping with sand casting helps identify potential design flaws early in the process, reducing costly modifications in later stages.
- Cost-Effectiveness: Sand casting is a cost-effective manufacturing method, particularly for low to medium volume production. The tooling costs are relatively low compared to other methods like die casting or injection molding. It is particularly advantageous for large and heavy parts, where the cost of alternative methods would be prohibitively high.
- Material Selection: Sand casting supports a wide range of materials, including various metals and alloys. This versatility allows designers to choose materials that meet specific performance requirements for their parts. From aluminum and iron to brass and steel, sand casting can accommodate a diverse array of materials.
- Production Scalability: Sand casting is scalable for both small and large production runs. Whether it’s a single prototype or thousands of parts, the sand casting process can be adjusted to meet the required production volume. This scalability makes it a suitable choice for industries with varying production demands.
- Tooling Modifications: Another advantage of sand casting is the ease of modifying the molds. If design changes are necessary, alterations to the pattern or mold can be made relatively quickly and cost-effectively. This flexibility allows for iterative improvements and adjustments during the production process.
Despite its advantages, sand casting also has limitations. It may not be suitable for parts with very tight tolerances or intricate internal geometries. Additionally, the surface finish of sand cast parts may not be as smooth as that achieved through other manufacturing methods. However, secondary operations like machining can be employed to refine the surface finish and achieve tighter tolerances if required.
Overall, sand casting is a valuable manufacturing process that bridges the gap between design and production. Its design flexibility, cost-effectiveness, and scalability make it an attractive choice for producing a wide range of metal parts, contributing to the realization of innovative designs and efficient production processes.