The solidification time of a steel casting depends on the ratio of its volume to surface area, which is called the “solidification modulus”, or simply “modulus”, and is expressed by a formula.
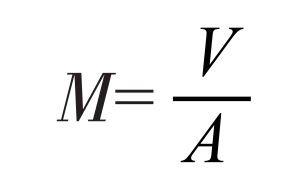
Where: M is the modulus, cm; V is the volume of the steel casting, cm ^ 3; A is the heat dissipation surface area of the steel casting, cm ^ 2.
Research has shown that, regardless of the shape of steel castings with different shapes, weights, and uses, as long as their modulus is equal, the solidification time is equal or similar. Steel castings with small modulus have a short solidification time, while steel castings with large modulus have a long solidification time.
The location of the shrinkage cavity in the steel casting is the final solidification position of the steel casting. The solidification time of each part of a steel casting depends on the ratio of volume to surface area at that part, that is, on the modulus at that part.
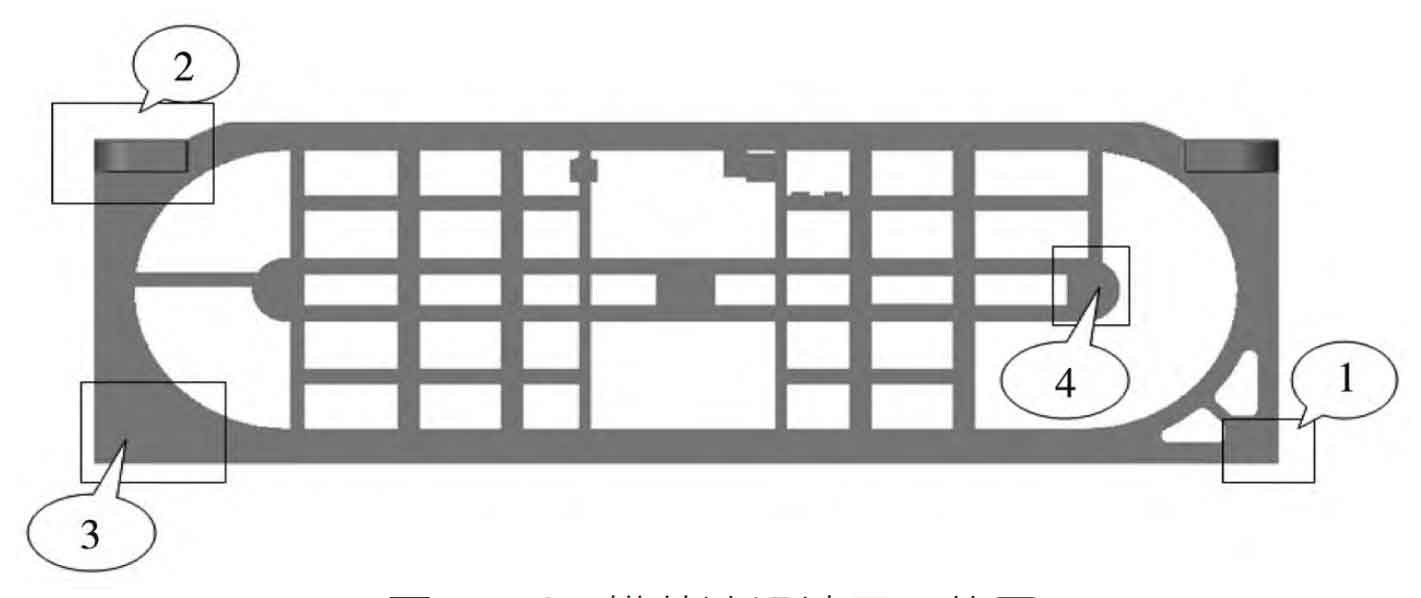
Based on the above theoretical knowledge, this study adopts modulus method and empirical method to design the riser. The modulus of each plate position of the steel casting was calculated using the Croe2.0 split function and analysis function. The selected position is shown in Figure 1, and the calculation results are shown in the table.
Project | Volume/cm^3 | Surface area/cm^2 | Modulus/cm |
Integral casting | 26 904.60 | 24 299.62 | 1.11 |
Zone 1 | 308.57 | 308.57 | 1.12 |
Zone 2 | 1 903.57 | 1 903.57 | 1.62 |
Zone 3 | 1 294.63 | 1 294.63 | 1.65 |
Zone 4 | 417.88 | 417.88 | 1.00 |
According to the modulus method calculation, there is no significant difference between the modulus of these four parts of the steel casting and the modulus of the entire steel casting, indicating that the solidification of each part of the steel casting is simultaneous, and sequential solidification cannot be achieved. It is only possible to achieve sequential solidification within the continuity range of the riser. Therefore, combining the calculated modulus and practical experience, a casting process as shown in Figure 2 was developed.
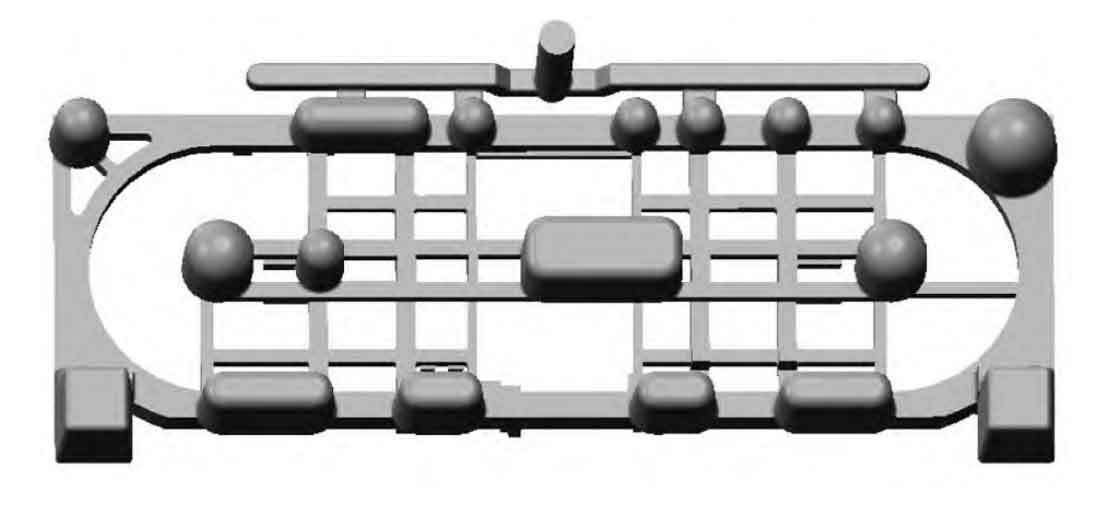
Calculate the pouring speed according to the casting process plan. According to the gating system design theory of casting technology, the open gating system should be adopted for steel castings poured in bottom pouring ladle. When the cross-sectional area of the ladle hole is used as the flow control area, the pouring time should be calculated according to the formula.
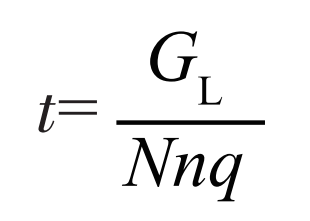
Where: t is the pouring time, s; GL is the weight of molten steel in the mold, kg; N is the number of casting bags poured simultaneously; N is the number of pouring holes for each missed package; Q is the average pouring speed, kg/s.
According to the characteristics of the process and tooling, GL=330 kg, N=1, n=1, and q=30 kg/s are substituted into the above formula, and t=11 s is calculated. According to the actual situation, the pouring time is taken as 10-14 s.