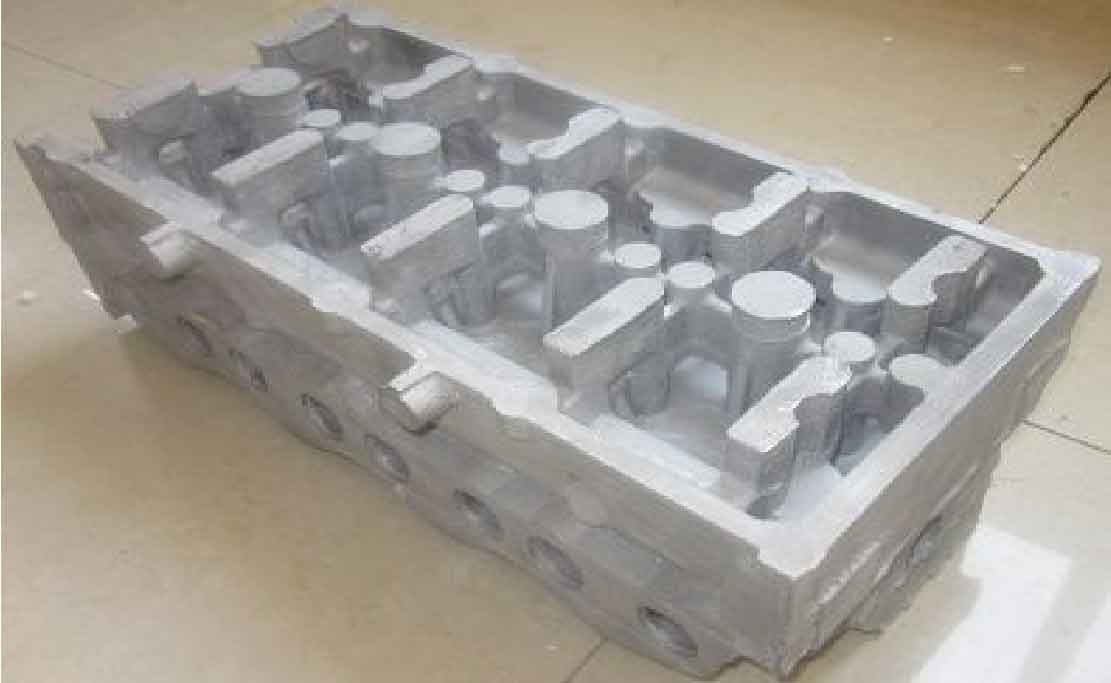
Intelligent manufacturing and green manufacturing are the development direction of China’s manufacturing industry. As the foundation of machinery manufacturing industry, the foundry industry firmly adheres to the concept of “green manufacturing”. The intelligent and green cleaning process of castings has always been a difficult problem for the casting industry. Casting practitioners pay more and more attention to the cleaning and grinding of castings. They have developed non-standard automatic grinding machines and their moulds, which have improved the casting environment and production efficiency to a certain extent. However, there are still some deficiencies in the development of non-standard equipment and its tires and fixtures, which requires many practitioners to continue to optimize the design. Taking the grinding mould of an automatic grinding line of our company as the research object, the design optimization development is carried out. The optimized mould has the advantages of high generalization, simple replacement and strong structural reliability, and can be applied and popularized in practical production.
Compared with the prior art scheme, the optimized mould has the following advantages:
(1) The dynamic adjustment of the grinding positioning clearance of the cast cylinder head can be realized by adjusting the thickness of the gasket, so as to avoid the inaccurate positioning caused by the wear of the grinding mould in the use process, resulting in uneven grinding or even scrapping of the casting.
(2) The overall reliability of the mould bottom plate sink + insert block structure is high. It is easy to replace when grinding different cast cylinder heads. The positioning column is not limited by the shape of the valve seat hole of the cast cylinder head. It can be designed according to the shape of the product. The design freedom is large, which maximizes the sharing of the mold when grinding different cast cylinder heads.