The process parameters of forging and quenching have a great influence on its strengthening effect. The main process parameters include: forging heating temperature, forging deformation, residence time after forging, forging quenching temperature, tempering after quenching with forging waste heat, etc.
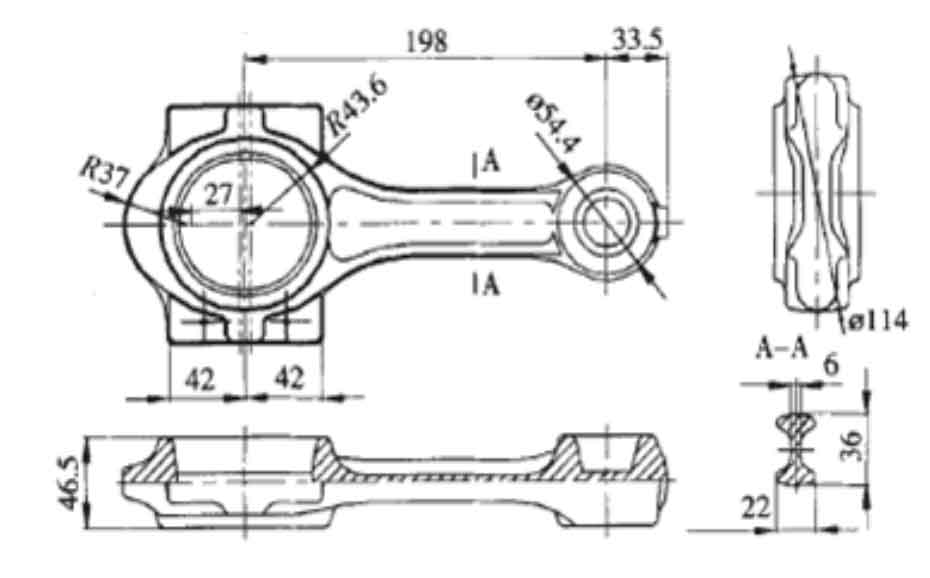
1) Forging heating temperature (initial forging temperature): since the deformation temperature of steel is much higher than the recrystallization temperature of deformed austenite, the initial forging temperature should not be too high from the perspective of forging residual heat quenching and deformation effect, and the process of dynamic and static recrystallization and growth of defects in deformed austenite crystals under high temperature should be slowed down as far as possible. At the same time, it is also necessary to prevent the internal friction during the deformation process from making the forging temperature too high and promoting the austenitic grain coarsening. On the premise of ensuring the forging forming, the initial forging temperature should be slightly lower than the normal forging process. When the final forging temperature is higher than 950 ℃, the lower limit of the initial forging temperature shall be taken. When the final forging temperature is lower than 900 ℃, the upper limit of the initial forging temperature shall be taken. In principle, as long as the surface temperature of the workpiece during deformation quenching is not lower than the transformation critical point A3 temperature, and no non martensitic structure is produced during quenching.
2) Forging deformation variable: jb/t4202 stipulates that the optimal deformation variable during deformation quenching is about 25%-40%, because only when the deformation variable exceeds 20%, although dynamic and static recrystallization occurs, obvious deformation strengthening effect is still retained, such as substructure refinement, but toughness is significantly improved. Once the deformation is less than 20%, the austenite grain size has been coarsened during high temperature heating, and the small deformation causes local deformation, resulting in uneven grain size, which has no good effect on the strength and toughness of the steel. However, the higher deformation, the easier the recrystallized grains to grow due to the increase of thermomechanical deformation, which will affect the final strengthening and toughening effect.
3) Residence time after forging: after high-temperature plastic deformation, subsequent processes such as trimming and finishing are generally required, and the final forging temperature is higher than the recrystallization temperature of austenite. In the period of time before quenching after forging, the internal structure and composition of forgings will change, which will inevitably affect the properties of forgings after quenching with residual heat.
The longer residence time after forging will lead to the dynamic multilateralization, recrystallization and further growth of dislocation network of deformed austenite. Due to the reduction of dissolved carbon in austenite during deformation, the precipitated carbides will re dissolve in residence time and cause the redistribution of alloy elements, thus affecting the strength and toughness effect of steel. The above process is faster for carbon steel and slower for medium and high alloy steel. If the alloy steel is in the hot work hardening state at the end of deformation, the recovery and recrystallization process is slow, and the residence time is too long, it will cause obvious growth of austenite grain, or ferrite will be separated from austenite, and its strength and toughness will be lower than the normal quenching and tempering state. It is recommended that the retention time of carbon steel after forging shall not be greater than 60s, and that of alloy steel after forging shall not be greater than 20S-60S.
4) Quenching temperature of forging heat, that is, the surface temperature of workpiece before entering quenching cooling medium after forging. The temperature is closely related to the initial forging temperature, deformation method, deformation variable, deformation rate, residence time after forging and environmental temperature and humidity. Generally, die forging has a high deformation rate, and most of them are formed by one-time heating. The forging and quenching temperatures of the workpieces are higher than 950 ℃. However, roll forging has low deformation rate and large deformation, which requires multi pass rolling. Generally, the quenching temperature is about 900 ℃.
When the quenching temperature is high, the hardenability of the steel can be improved, which is of practical significance to carbon structural steel. However, it is disadvantageous from the view of strengthening and toughening effect of forging heat quenching. At lower quenching temperature, as long as appropriate quenching medium is used, the effect of forging heat quenching can also be brought into full play.
According to the requirements of steel type, forging shape, size and mechanical properties, the quenching temperature shall be a certain temperature value between the transformation critical point Ar3 and ARCM or arcm-ar1 of the steel.
5) Tempering after quenching by forging waste heat. There is forging stress during quenching by forging waste heat. Tempering shall be carried out in time to prevent distortion and cracking of quenched parts.
The rigorous decarburization layer requirement of connecting rod has always been a very difficult problem in the heat treatment and quenching process. Although gas carburizing well type electric furnace is selected, methanol and kerosene titration devices are configured, and controllable atmosphere is implemented to prevent its oxidative decarburization, two problems are difficult to solve: one is that the carbon potential in the furnace cannot be measured, so the accurate input amount of methanol cannot be determined; Second, it is unscientific to rely solely on people to measure the drops of methanol and kerosene, which leads to serious out of control decarbonization in the heat treatment process.
Whether the forging heat quenching process can be implemented normally depends on two aspects, one is the final forging temperature, the other is the deformation degree. Because there are still some problems in the forging process, such as heating, blank making, forming and edge cutting, the oil inlet temperature of forgings can be guaranteed only by making the beat fixed and the operation rhythm accelerated. Moreover, it is determined that the overall deformation of the connecting rod after trimming and punching is small, which promotes the popularization of this process. Of course, this process can be closely connected with the forging process, and the quenched connecting rod can be transferred to the heat treatment workshop for batch tempering in time. The quality assurance shall be operated by experienced heat treatment workers, monitored by infrared measuring instruments, and supervised by quality inspectors according to special processes.