In the past, riser design basically followed the principle of sequential solidification, which needs to meet the following three conditions:
(1) . the solidification time of molten iron in the riser shall not be less than the solidification time of the feeding position.
(2) There is enough iron water in the riser to supplement the shrinkage of the gray iron casting and fill the expanded volume of the cavity after German injection.
(3) In the solidification stage, there is a feeding channel between the riser and the position being fed, and the expanding angle is opposite to the riser.
The location and size of riser are determined by these three rules. The riser location is generally designed near the hot spot of gray iron casting and the highest and thickest position of gray iron casting, while the size design requires that riser should be later than casting solidification.
However, there is a defect in this principle, that is to say, for some risers with large wall thickness, they are usually designed with large caliber and high height, thus reducing the process yield. Not only that, for some gray iron castings with larger wall thickness than ordinary castings, although the riser design is very large, the feeding effect is still poor. For example, zhycasting used to make the worktable casting of milling machine. The relative height and wall thickness at a certain position above the mold are more than 140mm. According to the principle of sequential solidification, the gray iron casting process is designed to place the riser at this position. However, there are serious shrinkage and porosity defects at this position in several finished gray iron castings. The riser diameter is 160mm – up to 200mm, and still exits continuously Now shrinkage is a problem. At last, shrinkage and porosity are reduced by placing insulation riser. It can be seen from this example that the riser does not have to follow the principle of sequential solidification at some times.
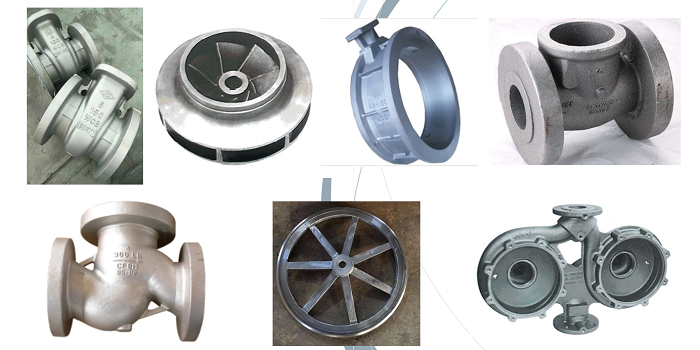
In recent years, the theory of balanced solidification has been put forward, that is, when the gray iron casting cools and solidifies to , the shrinkage of the casting itself must be supplemented by the riser and spot injection system. When the equilibrium point is reached, the molten iron in the cavity will no longer contract. No matter whether the feeding channel exists or not, the casting no longer needs the molten iron in the riser. At this time, the riser does not need feeding. Therefore, the molten iron in the riser of the casting does not need to solidify later than the body.
Therefore, ten technological principles of balanced solidification are put forward
(1) Since the shrinkage of gray iron castings is uncertain, the riser composition cannot be determined by the composition and brand of molten iron, but other factors, including metallurgical factors, casting shape, mold conditions and injection plan, must be considered comprehensively.
(2) , thin-walled parts should pay attention to feeding, but the requirements for feeding of gray iron castings with large wall thickness are not important, and even the riser free process can be used.
(3) The riser of cast iron should not be later than the gray iron casting solidification, and the riser can be smaller than the casting in size and modulus.
(4) . the riser of the gray iron casting shall not be set on the hot spot of the casting to prevent the thermal interference of the riser to the gray iron casting. The root of the two positions of the internal sprue and riser shall not coincide with the hot spot position of the casting.
(5) . the pouring riser shall be arranged to prevent the formation of contact hot spot.
(6) . the riser of gray iron castings shall be specially designed.
(7) , the position of the thick wall hot spot of the gray iron casting is placed below the Shaoxing injection position. When the wall thickness changes greatly, the cold iron is placed at the thick wall position, and the riser may not be placed on the casting.
(8) Adopt cold iron to eliminate hot spot, which can also reduce riser size, at the same time, it can increase the self feeding capacity of the whole casting. The quality of cold iron is better than common cast iron, and the use times of cold iron should be standardized.
(9) The same technological effect can be obtained for the heat preservation in the position with smaller wall thickness and the cold iron in the position with larger wall thickness.
(10) Top injection process is recommended. The best way to place the inner gate of round casting is to introduce it radially and axially.
From the process design principles of the above two theories, we can see the differences between them:
(1) In terms of feeding time, the principle of sequential solidification emphasizes that the molten iron in the riser should be solidified in the gray iron casting body, while the principle of balanced solidification is no longer emphasized, which determines that the principle of sequential solidification requires the riser to be placed in the hot spot of the gray iron casting, while the principle of balanced solidification avoids the hot spot;
(2) , riser size. In the principle of sequential solidification, the riser size and modulus must be larger than the gray iron casting body, while in the principle of balanced solidification, the riser size is smaller.
At present, the principle of sequential solidification is generally adopted for some gray iron castings with small wall thickness, while the principle of uniform solidification is generally used for the design of some thick wall castings.