Detecting and correcting defects in lost foam casting requires a systematic approach and attention to detail. Here are some best practices to help in the detection and correction of defects in the lost foam casting process:
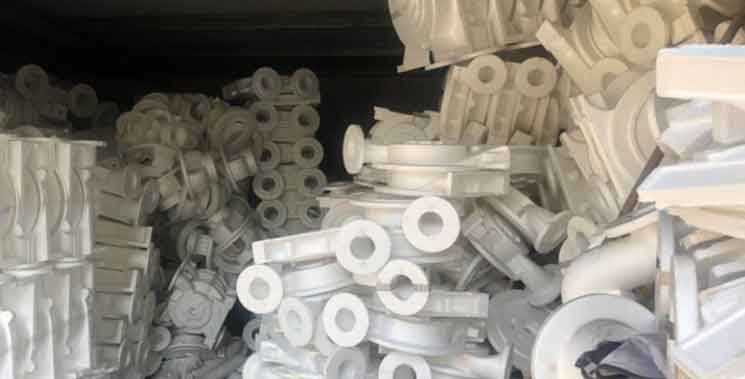
- Visual Inspection:
- Conduct a visual inspection of the castings to identify surface defects such as cracks, porosity, incomplete filling, and dimensional inconsistencies.
- Use proper lighting and magnification tools to ensure thorough inspection.
- Dimensional Inspection:
- Measure critical dimensions of the castings to ensure they meet the required specifications.
- Use precision measuring tools such as calipers, micrometers, or CMM (Coordinate Measuring Machine) for accurate measurements.
- Non-Destructive Testing (NDT):
- Employ NDT techniques such as X-ray, ultrasonic testing, or dye penetrant inspection to detect internal defects such as porosity, inclusions, or cracks.
- Train personnel in NDT methods and ensure proper equipment calibration and maintenance.
- Metallographic Analysis:
- Perform metallographic analysis by preparing samples, polishing them, and examining them under a microscope.
- Evaluate microstructural features, grain size, and the presence of any anomalies or defects.
- Defect Analysis and Root Cause Investigation:
- When defects are detected, conduct a thorough analysis to determine the root cause.
- Consider factors such as pattern quality, mold coating, pouring parameters, gating design, and metal quality to identify potential causes.
- Process Optimization:
- Based on the root cause analysis, make necessary adjustments to the casting process parameters.
- Optimize pattern design, mold coating, pouring temperature, pouring rate, and other variables to minimize defects.
- Pattern and Mold Maintenance:
- Regularly inspect and maintain foam patterns to ensure their dimensional accuracy and surface quality.
- Monitor and maintain the mold coatings to prevent degradation or erosion that can lead to defects.
- Quality Control Documentation:
- Maintain detailed records of the casting process parameters, inspection results, and corrective actions taken.
- Analyze the data to identify trends, patterns, and areas for improvement.
- Continuous Improvement:
- Implement a continuous improvement mindset, where feedback, data analysis, and lessons learned are used to refine the lost foam casting process.
- Encourage collaboration among team members to share insights and ideas for defect prevention and correction.
By following these best practices, manufacturers can effectively detect defects in lost foam casting, identify their root causes, and implement corrective actions to improve the overall quality and reliability of the castings.