Lost foam casting, also known as evaporative pattern casting, is a unique casting technique that involves the use of foam patterns to create intricate metal parts. The process is called “lost foam” because the foam patterns are vaporized or “lost” during the casting process. Here’s an overview of the lost foam casting technique:
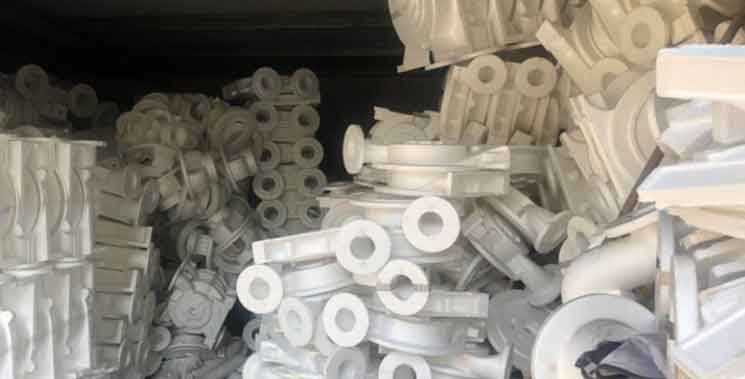
- Pattern Creation:
- The first step in lost foam casting is creating the foam pattern, which serves as a replica of the desired metal part.
- Foam patterns can be produced using various methods, including foam molding, CNC machining, or 3D printing.
- The foam material used is typically expanded polystyrene (EPS) or polyurethane foam due to their ability to withstand the casting process.
- Pattern Assembly:
- Once the foam patterns are created, they are assembled to form a cluster.
- The cluster consists of multiple foam patterns that will be cast together as a single unit.
- The patterns are connected using gating and riser systems, which allow the molten metal to flow into the mold and facilitate proper solidification.
- Pattern Coating:
- The foam pattern cluster is coated with a refractory material to create a shell around the patterns.
- The refractory material can be a ceramic slurry, a mixture of sand and binder, or a combination of both.
- The coating is applied in layers, allowing each layer to dry before applying the next to create a durable mold shell.
- Mold Preheating:
- Before casting, the mold is preheated to remove any moisture from the refractory coating and ensure proper mold strength and stability.
- The preheating process also helps eliminate the foam patterns within the mold by evaporating them during casting.
- Metal Casting:
- Once the mold is preheated, it is ready for the metal casting process.
- The mold is securely placed in a casting flask, and the molten metal is poured directly into the mold.
- The heat of the metal causes the foam patterns to vaporize, leaving behind a void that is filled with the molten metal.
- Solidification and Cooling:
- After the metal is poured, it solidifies within the mold cavity, taking the shape of the original foam patterns.
- The solidification and cooling process is carefully controlled to ensure proper metal solidification and prevent defects.
- Shakeout and Finishing:
- Once the metal has solidified and cooled, the mold is broken or “shaken out” to remove the casting.
- The casting is then cleaned and finished, which may involve removing any excess material, surface treatment, and dimensional inspection.
Lost foam casting offers several advantages, including the ability to produce complex and intricate part geometries, near-net shape castings, reduced material waste, and improved surface finish. It is widely used in various industries, including automotive, aerospace, and industrial manufacturing, where intricate and precise metal parts are required. Understanding the techniques involved in lost foam casting allows manufacturers to harness its capabilities and produce high-quality castings with intricate designs and complex features.