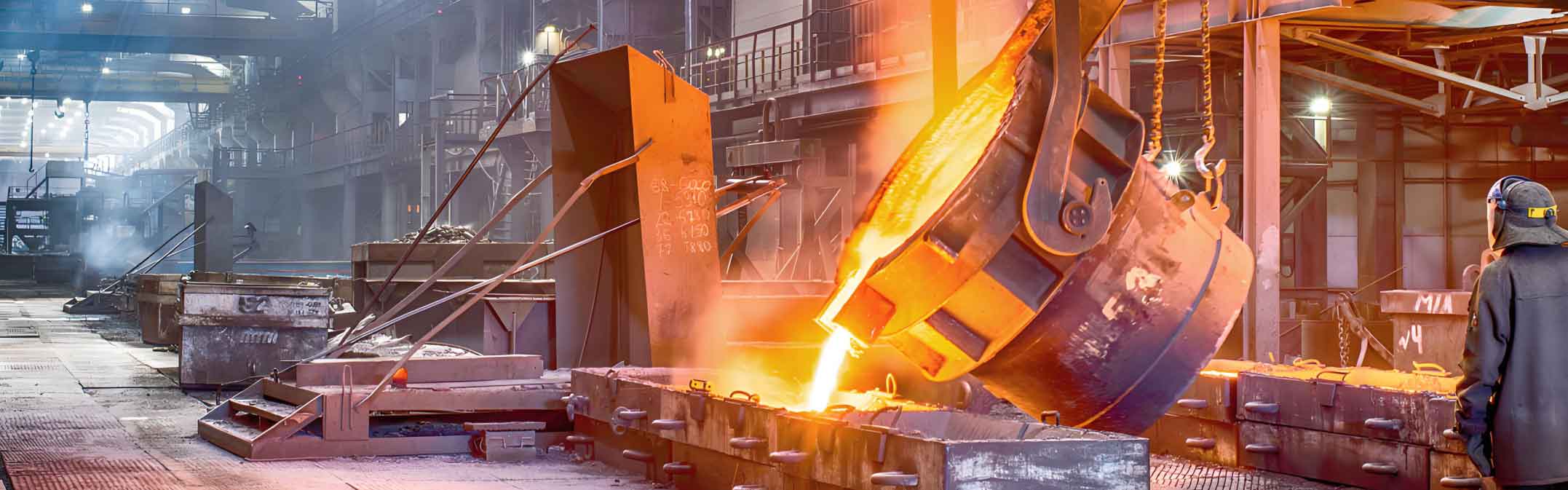
Sand casting is versatile and cost-effective manufacturing process widely used for producing metal components with complex geometries. Despite its advantages, traditional sand casting processes often produce parts with limited mechanical properties, particularly strength. For structural applications where high strength is crucial, it is essential to enhance the properties of sand castings through material selection, process optimization, and advanced techniques. This article explores the methods and strategies for developing high-strength sand casting suitable for structural applications.
Introduction to Sand Casting
Sand casting involves creating a mold from a sand mixture and pouring molten metal into the cavity formed by a pattern. Once the metal solidifies, the sand mold is broken away to reveal the final casting. This process is highly adaptable and economical, making it ideal for producing a wide range of metal components, from simple shapes to complex geometries.
Importance of High-Strength Sand Casting
High-strength sand castings are essential for structural applications that require components to withstand significant loads, stresses, and harsh operating conditions. These applications include construction machinery, automotive parts, aerospace components, and heavy equipment.
- Load-Bearing Capacity: Ensures components can support heavy loads without failure.
- Durability: Provides long-term performance and resistance to wear and tear.
- Safety: Enhances the safety and reliability of structural components.
Material Selection for High-Strength Sand Casting
Choosing the right material is the first step in developing high-strength sand castings. The material must offer a combination of strength, toughness, and ductility to meet the demands of structural applications.
Common Materials for High-Strength Sand Casting
Grey Cast Iron
Grey cast iron is widely used in sand casting due to its excellent castability, machinability, and vibration damping properties. However, its tensile strength is relatively low compared to other materials.
- Advantages: Good castability, machinability, and damping properties.
- Limitations: Lower tensile strength, brittleness.
Ductile Iron
Ductile iron, also known as nodular or spheroidal graphite iron, offers improved strength and ductility compared to grey cast iron. It is achieved by adding magnesium or cerium to the molten iron, resulting in spherical graphite inclusions.
- Advantages: High tensile strength, good ductility, and impact resistance.
- Applications: Automotive components, gears, crankshafts, and heavy machinery parts.
Alloy Steel
Alloy steels are steel alloys with additional elements such as chromium, nickel, and molybdenum, which enhance their mechanical properties. They offer high strength, toughness, and wear resistance.
- Advantages: Superior strength, toughness, and wear resistance.
- Applications: Structural components, heavy equipment, and high-stress applications.
Material | Advantages | Limitations |
---|---|---|
Grey Cast Iron | Good castability, machinability, damping properties | Lower tensile strength, brittleness |
Ductile Iron | High tensile strength, good ductility, impact resistance | More complex casting process, higher cost |
Alloy Steel | Superior strength, toughness, wear resistance | Higher cost, more challenging to cast |
Process Optimization for High-Strength Sand Casting
Optimizing the sand casting process is crucial for producing high-strength castings. This involves refining various aspects of the casting process, from mold materials to cooling techniques.
Mold Materials and Design
High-Quality Sand
Using high-quality sand with uniform grain size and appropriate binders ensures a strong and stable mold that can withstand the casting process without defects.
- Materials: Silica sand, zircon sand, olivine sand.
- Advantages: Reduces defects, improves surface finish, and enhances mold strength.
Advanced Binders
Binders hold the sand grains together, providing the necessary strength and stability to the mold. Advanced binders improve mold properties and reduce the risk of defects.
- Types: Organic binders (resins), inorganic binders (sodium silicate).
- Advantages: Improved mold strength, reduced gas generation, and better surface finish.
Mold Material | Advantages |
---|---|
High-Quality Sand | Reduces defects, improves surface finish, enhances strength |
Advanced Binders | Improved mold strength, reduced gas generation, better surface finish |
Optimized Cooling and Solidification
Controlling the cooling and solidification rates is essential for achieving the desired microstructure and mechanical properties in high-strength sand castings.
Directed Cooling
Directed cooling uses targeted cooling channels and systems to control the cooling rate and pattern within the mold, promoting uniform solidification.
- Advantages: Reduces thermal stresses, improves microstructure, and enhances mechanical properties.
Use of Chills
Chills are metal inserts placed within the mold to accelerate cooling and promote directional solidification, reducing shrinkage and improving strength.
- Advantages: Enhances grain structure, reduces defects, and improves strength.
Cooling Technique | Advantages |
---|---|
Directed Cooling | Reduces thermal stresses, improves microstructure |
Use of Chills | Enhances grain structure, reduces defects, improves strength |
Advanced Techniques for High-Strength Sand Casting
Incorporating advanced techniques into the sand casting process can further enhance the strength and quality of the final casting.
Heat Treatment
Heat treatment involves heating and cooling the casting in a controlled environment to alter its microstructure and enhance its mechanical properties.
Annealing
Annealing involves heating the casting to a specific temperature and then slowly cooling it, relieving internal stresses and improving ductility.
- Advantages: Reduces internal stresses, increases ductility, and refines grain structure.
Quenching and Tempering
Quenching involves rapidly cooling the casting from a high temperature to increase hardness, followed by tempering to reduce brittleness and enhance toughness.
- Advantages: Increases hardness and strength, improves toughness and ductility.
Heat Treatment | Advantages |
---|---|
Annealing | Reduces internal stresses, increases ductility |
Quenching and Tempering | Increases hardness and strength, improves toughness and ductility |
Grain Refinement Techniques
Grain refinement techniques improve the mechanical properties of castings by refining the grain structure and enhancing strength.
Electromagnetic Stirring
Electromagnetic stirring uses electromagnetic fields to stir the molten metal, promoting uniform grain structure and reducing segregation.
- Advantages: Refines grain structure, reduces segregation, enhances mechanical properties.
Addition of Grain Refiners
Adding grain refiners such as titanium or boron to the molten metal promotes the formation of fine, uniform grains, enhancing strength and toughness.
- Advantages: Refines grain structure, improves strength and toughness.
Grain Refinement Technique | Advantages |
---|---|
Electromagnetic Stirring | Refines grain structure, reduces segregation |
Addition of Grain Refiners | Promotes fine grains, improves strength and toughness |
Applications of High-Strength Sand Casting
High-strength sand castings are essential for various structural applications across multiple industries, providing the necessary mechanical properties and reliability.
Automotive Industry
- Engine Components: High-strength castings for engine blocks, cylinder heads, and crankshafts ensure durability and performance.
- Suspension Parts: High-strength suspension components provide better load-bearing capacity and impact resistance.
Construction and Heavy Machinery
- Structural Frames: High-strength castings for structural frames in construction machinery ensure stability and load-bearing capacity.
- Gears and Bearings: High-strength gears and bearings improve the performance and longevity of heavy machinery.
Aerospace Industry
- Turbine Blades: High-strength turbine blades withstand extreme temperatures and stresses in aerospace applications.
- Structural Components: High-strength castings for structural components provide reliability and safety in aerospace structures.
Industry | Applications |
---|---|
Automotive | Engine components, suspension parts |
Construction and Heavy Machinery | Structural frames, gears, bearings |
Aerospace | Turbine blades, structural components |
Conclusion
Developing high-strength sand castings for structural applications involves a combination of material selection, process optimization, and advanced techniques. By choosing the right materials, such as ductile iron and alloy steel, and optimizing the casting process with high-quality mold materials, advanced binders, and controlled cooling techniques, manufacturers can produce castings with superior mechanical properties. Incorporating advanced techniques like heat treatment and grain refinement further enhances the strength and quality of the castings, making them suitable for demanding structural applications in the automotive, construction, heavy machinery, and aerospace industries. These advancements ensure the production of reliable and high-performance sand castings that meet the stringent requirements of modern engineering and manufacturing.
Strategy | Purpose | Benefits |
---|---|---|
Material Selection | Choosing materials with high strength and ductility | Ensures load-bearing capacity, durability, safety |
Mold Materials and Design | Using high-quality sand and advanced binders | Reduces defects, improves surface finish, enhances strength |
Optimized Cooling | Controlling cooling and solidification rates | Reduces thermal stresses, improves microstructure |
Advanced Techniques | Incorporating heat treatment and grain refinement | Enhances strength, toughness, and overall quality |
By implementing these strategies, manufacturers can achieve high-strength sand castings that meet the rigorous demands of structural applications, ensuring reliable and long-lasting performance.