Sand casting is a popular and cost-effective manufacturing process used to produce a wide variety of metal parts. However, casting defects can often occur, compromising the quality and performance of the final product. This article explores common casting defects in sand casting parts, their causes, and strategies to minimize or eliminate these casting defects, thereby improving the overall quality and reliability of sand casting parts.
Introduction to Sand Casting
Sand casting involves creating a mold from a mixture of sand and a bonding agent, pouring molten metal into the mold, and allowing it to solidify. Once the metal has cooled, the sand mold is broken away to reveal the finished part. This process is highly versatile and can produce parts of varying sizes and complexities. However, casting defects can arise at various stages, affecting the integrity of the sand casting parts.
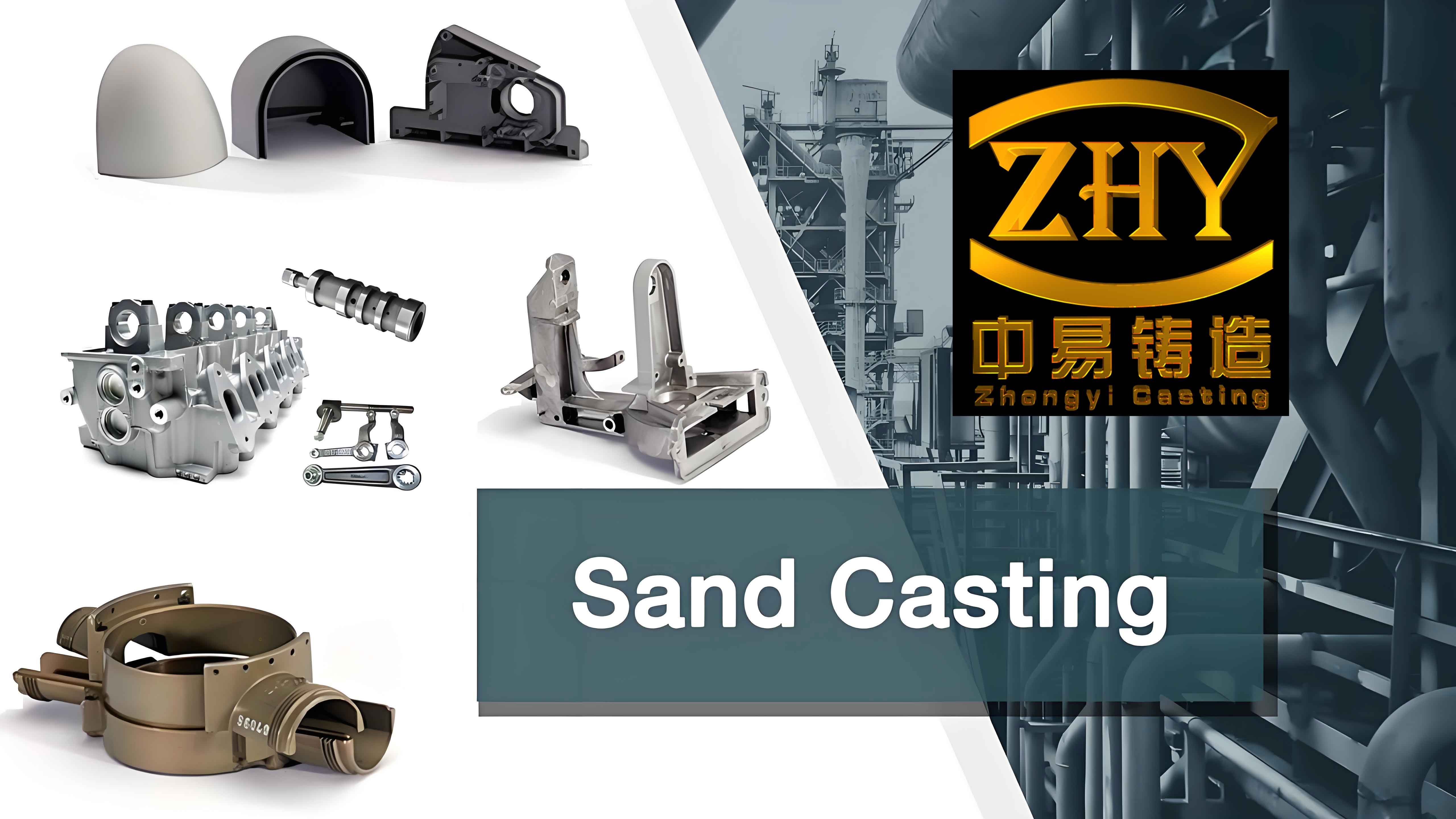
Common Casting Defects in Sand Casting Parts
Several types of casting defects can occur in sand casting parts. These casting defects can be broadly categorized into surface defects, internal defects, and dimensional defects.
1. Surface Defects
- Blowholes: These are cavities or holes on the surface of the casting caused by trapped gas or air.
- Scabs: These are rough, irregular projections on the surface caused by sand particles breaking away and becoming embedded in the metal.
- Cracks: Surface cracks can occur due to improper cooling or thermal stress.
2. Internal Defects
- Porosity: Small holes or voids within the casting caused by trapped gas or shrinkage.
- Inclusions: Non-metallic particles embedded within the metal, often from slag or sand.
- Hot Tears: Irregular cracks inside the casting caused by internal stresses during cooling.
3. Dimensional Defects
- Mismatches: Misalignment of mold halves leading to offset or shifted parts.
- Distortion: Warping or bending of the part due to uneven cooling or mold instability.
Causes of Casting Defects in Sand Casting Parts
Understanding the root causes of casting defects is essential for developing effective strategies to prevent them. Common causes include:
- Improper Mold Preparation: Poor mold construction or improper sand mixture can lead to casting defects such as scabs and cracks.
- Inadequate Venting: Insufficient venting can trap gases, leading to blowholes and porosity.
- Incorrect Pouring Temperature: Pouring metal at too high or too low a temperature can cause casting defects like hot tears and inclusions.
- Uneven Cooling: Inconsistent cooling rates can lead to cracks, distortion, and internal stresses.
Strategies to Reduce Casting Defects
Several strategies can be employed to reduce casting defects and improve the quality of sand casting parts.
1. Improved Mold Design and Preparation
- Use High-Quality Sand: Ensure the sand mixture has the correct grain size and bonding agent.
- Proper Mold Compaction: Ensure the sand mold is compacted uniformly to prevent weak spots.
- Adequate Venting: Design molds with sufficient vents to allow gases to escape.
2. Optimized Pouring Techniques
- Controlled Pouring Temperature: Maintain the correct pouring temperature to prevent thermal stress and hot tears.
- Steady Pouring Rate: Pour the molten metal at a consistent rate to avoid turbulence and gas entrapment.
- Use of Chills: Place metal chills in the mold to control the cooling rate and reduce internal stresses.
3. Enhanced Post-Casting Processes
- Heat Treatment: Apply heat treatment processes to relieve internal stresses and improve mechanical properties.
- Surface Finishing: Use surface finishing techniques such as grinding and polishing to remove surface casting defects.
- Non-Destructive Testing: Employ methods like X-ray inspection and ultrasonic testing to detect internal casting defects.
Table 1: Strategies to Reduce Casting Defects
Strategy | Actions | Benefits |
---|---|---|
Improved Mold Design and Preparation | Use high-quality sand, proper mold compaction, adequate venting | Reduces surface and dimensional defects |
Optimized Pouring Techniques | Control pouring temperature, steady pouring rate, use of chills | Minimizes internal defects and porosity |
Enhanced Post-Casting Processes | Heat treatment, surface finishing, non-destructive testing | Detects and eliminates internal and surface defects |
List: Key Actions to Improve Sand Casting Parts Quality
- Use high-quality sand with appropriate grain size and bonding agent.
- Ensure uniform compaction of the sand mold to prevent weak spots.
- Design molds with adequate venting to allow gas escape.
- Maintain correct pouring temperature and rate to prevent thermal stress.
- Apply heat treatment to relieve internal stresses and improve mechanical properties.
- Utilize surface finishing techniques to remove surface casting defects.
- Conduct non-destructive testing to detect and address internal casting defects.
Case Study: Improving Quality of Sand Casting Parts in Automotive Industry
Problem
An automotive parts manufacturer was experiencing high rejection rates due to casting defects such as porosity and cracks in their sand casting parts.
Solution
The manufacturer implemented the following measures:
- Improved mold design with high-quality sand and adequate venting.
- Optimized pouring temperature and rate to reduce turbulence and gas entrapment.
- Applied heat treatment to relieve internal stresses.
Result
The rejection rate due to casting defects decreased by 40%, and the overall quality and durability of the sand casting parts improved significantly.
Table 2: Case Study Results
Metric | Before Implementation | After Implementation | Improvement |
---|---|---|---|
Rejection Rate Due to Defects (%) | 15% | 9% | 40% reduction |
Average Tensile Strength (MPa) | 250 | 280 | 12% increase |
Customer Complaints | High | Low | Significant reduction |
Conclusion
Reducing casting defects in sand casting parts is essential for improving their quality, performance, and durability. By understanding the common casting defects and their causes, and by implementing effective strategies such as improved mold design, optimized pouring techniques, and enhanced post-casting processes, manufacturers can significantly reduce casting defects and produce high-quality sand casting parts. Continuous improvement and adoption of advanced technologies will further enhance the reliability and performance of sand casting parts in various applications.