With the development of the times and the progress of technology, new energy vehicles have been widely promoted due to their many advantages such as energy conservation, environmental protection, and policy guarantees. Nowadays, more and more people choose to buy new energy vehicles. New energy vehicles not only meet people’s daily travel needs, but also play an important role in protecting the natural environment, reducing exhaust emissions, and other aspects. The battery end plates of new energy vehicles generally choose aluminum alloy, and the use of aluminum alloy materials Long life, flame retardant, smokeless, non-toxic, excellent explosion-proof and anti-aging performance. Through the development and research of battery end plates, production can be expanded more reasonably while improving the speed of technological research and development. The traditional low-pressure casting process can flexibly adjust the pouring pressure and filling speed to ensure smooth and stable filling of the metal liquid, resulting in smooth surface, dense microstructure, excellent mechanical properties, and economic efficiency of low-pressure casting castings. However, the low-pressure casting process involves multiple process parameters, and due to people’s increasing pursuit of aesthetics, the design of some components is becoming increasingly complex. Therefore, without optimization methods, researchers find it difficult to obtain reasonable process parameters. This article takes the aluminum alloy battery end plate of a new energy vehicle as the research object, and uses ProCAST software to conduct numerical simulation analysis of its low-pressure casting process. Based on orthogonal experiments and signal-to-noise ratio analysis method, multi-objective optimization of process parameters is carried out, aiming to obtain a set of standardized process design parameters, providing important reference for the research and actual production of low-pressure casting forming technology for aluminum alloy battery end plates of new energy vehicles.
Initial Process Analysis of Low Pressure Casting
A three-dimensional model of the end plate with a pouring system, the battery end plate is a rectangular structure, with a maximum contour size of 558 mm x 244 mm x 40 mm, and a volume of 0.003 m3, with a mass of 7.3 kg, the overall shape is relatively regular, and the wall thickness is relatively uniform, with an average wall thickness of 31 mm. Adding four slag pockets on the casting is beneficial for solidification and shrinkage of the surrounding areas. The design requirement of the low-pressure casting pouring system is to ensure the smoothness of the metal liquid in the casting cavity Filling is used to avoid any splashing and eddy currents, and to achieve sequential solidification for the best filling effect. Therefore, a bottom pouring single-sided runner pouring method is adopted, and the appropriate gate position is selected and the number of gates is determined. CATIA modeling software is used to establish a three-dimensional model with a pouring system, and then the model is imported into the MESH module of PROCAST for mesh division.
Optimization of low-pressure casting process parameters
The process parameters of low-pressure casting mainly include lifting pressure, lifting time, filling pressure, filling time, pouring temperature, and mold preheating temperature. Different combinations of process parameters have a significant impact on the forming quality of battery end plates, but due to the different values of each parameter Multiple different parameter combinations need to be considered. This article adopts the orthogonal experimental method to select three process parameters: pouring temperature, mold preheating temperature, and filling time. A 3-factor and 4-level experimental plan is set up, with a specific factor level table. The evaluation indicators are the volume value of shrinkage porosity, solidification time, and the size of secondary dendrite spacing. Shrinkage and porosity defects are important factors affecting the mechanical properties and fatigue life of castings. When the volume value of shrinkage and porosity at a certain location of the casting is greater than 1, shrinkage and porosity defects will appear at that location. The larger the volume value, the larger the defect. The actual production efficiency of castings will be affected by the solidification time, and the shorter the solidification time, the higher the production efficiency; The solidification time of castings is closely related to the size of the secondary dendrite spacing. The faster the solidification speed of the molten metal, the better the performance of the castings, and the smaller the secondary dendrite spacing. Therefore, in actual production, the alloy performance can be improved by appropriately shortening the solidification time. The concept of “signal-to-noise ratio” is a measure of the quality characteristics of three types: large, small, and large, introduced by Dr. Xuanyi Taguchi from Japan in the Taguchi test method to evaluate the combination of parameters. This article aims to optimize the process parameters of low-voltage casting for battery end plates, and obtain the minimum volume value of shrinkage porosity and secondary dendrite spacing, as well as the shortest solidification time.
Casting optimization plan and experimental verification
Based on the above analysis, numerical simulation verification was conducted to determine the optimal process parameter combination for low-pressure casting of aluminum alloy battery end plates. The numerical simulation results showed that the volume values of shrinkage porosity and porosity in all four schemes were less than 1, so there were no shrinkage porosity and porosity defects. In terms of secondary dendrite spacing and solidification time, Scheme 3 is the smallest. Therefore, after comprehensive analysis, Scheme 3 (A1B1C1) is determined as the optimal process parameter combination, which is a pouring temperature of 690 ℃, a mold preheating temperature of 330 ℃, and a filling time of 8 seconds.
The distribution of shrinkage and porosity in the optimal process plan is shown in Figure 3, with a volume value of 0.83 cm3; The distribution of secondary dendrite spacing, with the maximum value of secondary dendrite spacing being 43.94 μ m; The solidification time is 140.6 seconds, and the temperature distribution at the end of solidification. After optimizing the battery end plate, there are no macroscopic shrinkage porosity defects in the numerical simulation results. In order to verify the feasibility of this optimized process plan, production trial production was carried out according to the optimal process plan, and representative positions were selected for the extraction of metallographic samples during the trial production process. After a series of treatments such as rough grinding, fine grinding, and polishing, the sample is corroded with 5% volume fraction HF acid, then rinsed with alcohol and blown dry. The microstructure of the polished surface observed under a microscope. Observation shows that the internal structure of the aluminum alloy battery end plate is uniform, with small grains and no obvious shrinkage porosity defects. This result fully demonstrates the feasibility of this optimized process plan.
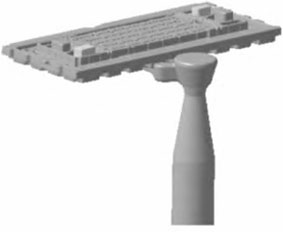
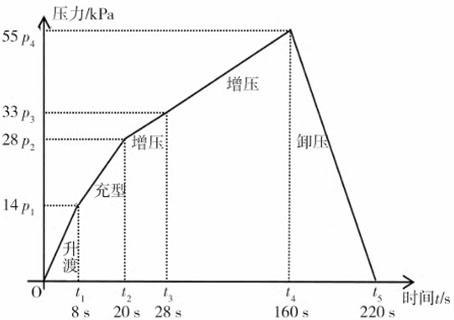
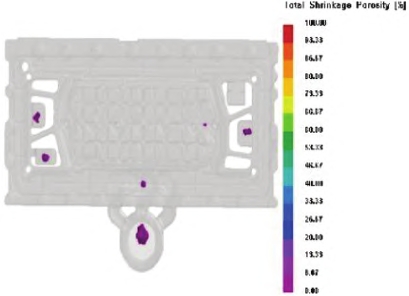
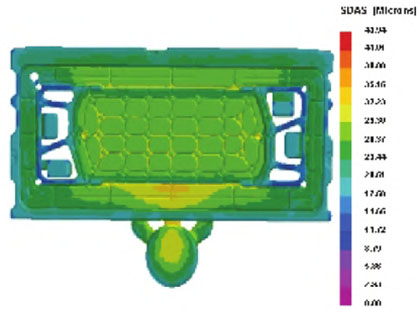
Conclusion
(1) Based on orthogonal experimental design, the influence of various process parameters on the quality evaluation indicators of battery end plates was explored. For the indicator of shrinkage porosity and pore volume, the most significant impact is on the filling time, followed by the pouring temperature and mold preheating temperature; For the secondary dendrite spacing, the mold The influence of preheating temperature is most significant, followed by filling time and pouring temperature; The effect of mold preheating temperature on solidification time is most significant, Next are the pouring temperature and filling time.
(2) After comprehensive analysis, the optimal process parameters for low-pressure casting of aluminum alloy battery end plates were determined as Scheme 3 (A1B1C1), which includes a pouring temperature of 690 ℃, a mold preheating temperature of 330 ℃, and a filling time of 8 seconds.
(3) Under the optimized plan, the casting has no shrinkage, porosity, and porosity defects, with the smallest secondary dendrite spacing and the shortest solidification time. The correctness of the optimization plan was ultimately verified through production trial production and metallographic analysis.