Die casting is a highly efficient manufacturing process that is widely used to produce complex metal parts with high precision and excellent surface finish. However, achieving the desired precision in die casting parts requires meticulous planning and optimization of the process parameters. Advanced simulation technologies have emerged as powerful tools to enhance the precision of die casting parts by predicting potential defects, optimizing the die design, and improving overall process efficiency. This article explores the role of advanced simulation in enhancing the precision of die casting parts, highlighting key techniques, benefits, and applications.
Introduction to Die Casting
Die casting involves injecting molten metal into a mold cavity under high pressure. The molds, or dies, are typically made from high-grade steel and are capable of producing a wide range of parts with intricate geometries and tight tolerances. Common materials used for die casting include aluminum, zinc, and magnesium alloys. The process is known for its ability to produce high-quality parts with excellent mechanical properties and minimal post-processing.
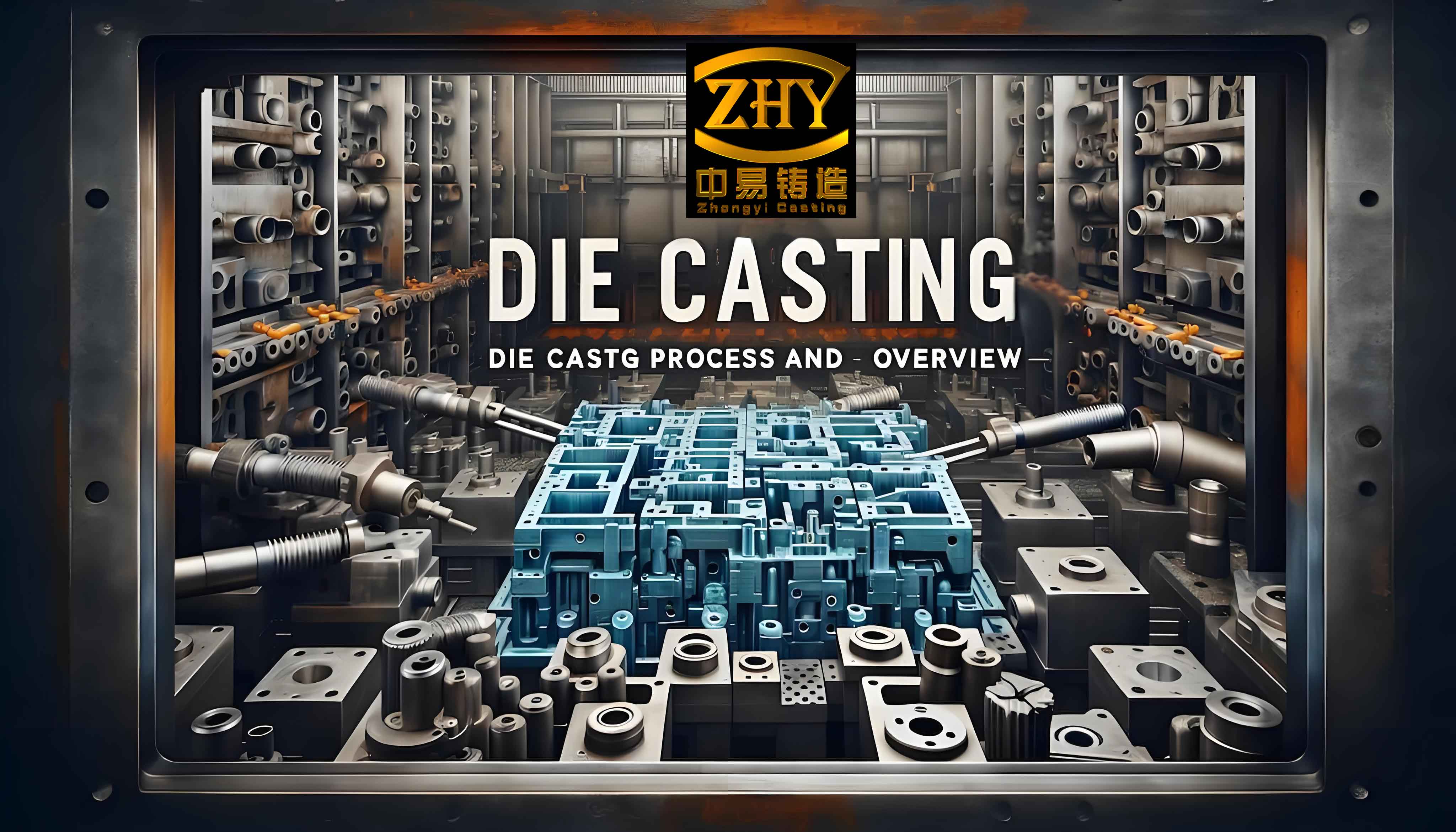
The Need for Precision in Die Casting Parts
Achieving high precision in die casting parts is critical for ensuring their functionality and performance in various applications. Precision in die casting parts is influenced by several factors, including:
- Die Design: The geometry and quality of the die directly affect the final dimensions and surface finish of the die casting parts.
- Process Parameters: Variables such as injection speed, pressure, and temperature must be carefully controlled to avoid defects.
- Material Properties: The choice of alloy and its behavior during solidification impact the precision and quality of the die casting parts.
Table 1: Factors Affecting Precision in Die Casting Parts
Factor | Description |
---|---|
Die Design | Geometry, quality, and maintenance of the die |
Process Parameters | Injection speed, pressure, temperature, and cooling rate |
Material Properties | Alloy selection and solidification behavior |
Role of Advanced Simulation in Die Casting
Advanced simulation technologies have revolutionized the die casting industry by enabling manufacturers to predict and address potential issues before physical production begins. These simulations use computational models to mimic the die casting process, providing valuable insights into various aspects that affect precision.
Benefits of Advanced Simulation
- Defect Prediction and Reduction: Simulation tools can identify potential defects such as porosity, shrinkage, and cold shuts, allowing engineers to adjust parameters and die design to minimize these issues.
- Optimized Die Design: By simulating the flow of molten metal and the solidification process, engineers can optimize the design of the die to ensure uniform filling and reduce stress concentrations.
- Process Optimization: Simulations help in fine-tuning process parameters such as injection speed, pressure, and cooling rates, leading to improved precision and consistency in die casting parts.
- Cost and Time Savings: Advanced simulations reduce the need for multiple physical prototypes and trial runs, saving both time and cost in the development process.
Key Simulation Techniques
- Finite Element Analysis (FEA): Used to predict the behavior of materials and components under various conditions, helping in optimizing die design and process parameters.
- Computational Fluid Dynamics (CFD): Simulates the flow of molten metal within the die cavity, ensuring proper filling and minimizing defects.
- Thermal Analysis: Evaluates the heat transfer during the die casting process, aiding in the design of effective cooling systems and minimizing thermal stresses.
Table 2: Advanced Simulation Techniques
Technique | Description |
---|---|
Finite Element Analysis | Predicts material behavior and optimizes die design |
Computational Fluid Dynamics | Simulates molten metal flow and minimizes filling defects |
Thermal Analysis | Evaluates heat transfer and designs effective cooling systems |
Applications of Advanced Simulation in Die Casting
Advanced simulation technologies are applied across various industries to enhance the precision and quality of die casting parts. Some key applications include:
- Automotive Industry: Precision die casting parts such as engine components, transmission housings, and structural parts benefit from optimized die design and process parameters.
- Consumer Electronics: Housing components, connectors, and heat sinks are produced with high precision to meet the stringent requirements of electronic devices.
- Aerospace Industry: Complex and lightweight components for aircraft and spacecraft are manufactured using advanced simulation to ensure reliability and performance.
- Medical Devices: High-precision parts for medical equipment and implants are produced with minimal defects, meeting the stringent standards of the medical industry.
List: Key Industries Utilizing Advanced Simulation in Die Casting
- Automotive Industry
- Consumer Electronics
- Aerospace Industry
- Medical Devices
Case Study: Enhancing Precision in an Automotive Component
Problem
An automotive manufacturer needed to produce a highly precise and complex engine component using die casting. The initial prototypes showed defects such as porosity and dimensional inaccuracies.
Solution
The manufacturer implemented advanced simulation tools to optimize the die design and process parameters:
- Defect Prediction: Simulations identified areas prone to porosity and shrinkage, allowing for adjustments in the die design.
- Optimized Die Design: The die was redesigned to improve metal flow and reduce stress concentrations.
- Process Optimization: Injection speed, pressure, and cooling rates were fine-tuned to enhance precision and reduce defects.
Result
The use of advanced simulation resulted in significant improvements in the precision and quality of the die casting parts. The final components met the stringent requirements of the automotive industry, with reduced defects and improved mechanical properties.
Table 3: Case Study Results
Criteria | Before Simulation | After Simulation |
---|---|---|
Defects (Porosity) | High incidence of defects | Significant reduction |
Dimensional Accuracy | Inconsistent | High precision achieved |
Mechanical Properties | Variable | Improved consistency |
Production Time | Longer due to trial runs | Reduced due to optimized parameters |
Conclusion
Advanced simulation technologies play a crucial role in enhancing the precision of die casting parts. By predicting potential defects, optimizing die design, and fine-tuning process parameters, these simulations enable manufacturers to produce high-quality parts with minimal post-processing and reduced costs. The integration of advanced simulation in the die casting process ensures that parts meet the stringent requirements of various industries, driving innovation and efficiency in manufacturing.