Die casting and lost foam casting are two popular methods used in the metal casting industry. While they share some similarities, they also have distinct differences. Let’s compare them in terms of process, complexity, cost, material suitability, and surface finish.
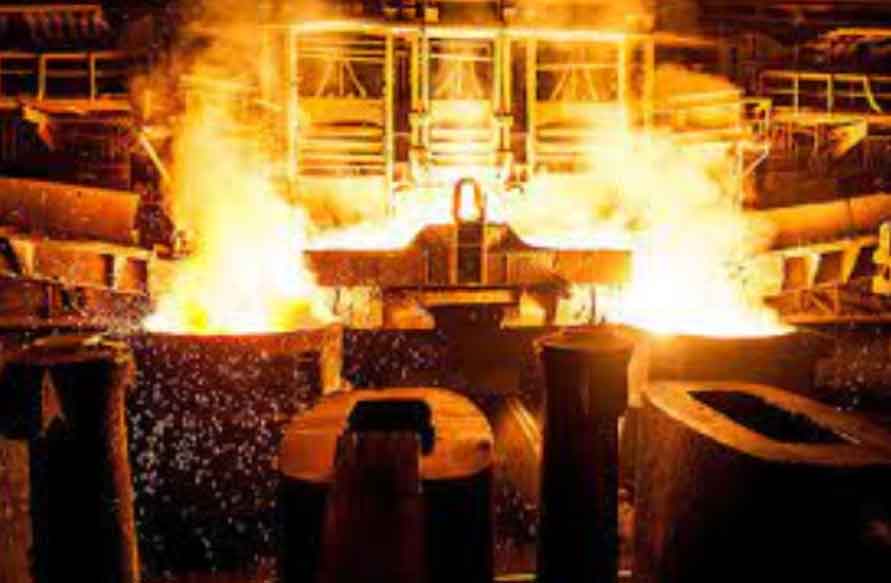
- Process:
- Die Casting: Die casting involves injecting molten metal, typically under high pressure, into a reusable metal mold called a die. The metal solidifies rapidly and takes the shape of the mold. The mold is then opened, and the casting is removed.
- Lost Foam Casting: In this process, a foam pattern of the desired object is created and coated with a refractory material. The coated pattern is then embedded in sand, and molten metal is poured into the mold. The heat of the metal causes the foam to vaporize, leaving behind the metal casting.
- Complexity:
- Die Casting: Die casting is a more complex process that involves the design and fabrication of the die, which must withstand high pressures and temperatures. The injection process requires precise control of variables such as temperature, pressure, and cooling.
- Lost Foam Casting: The process is relatively simple, requiring the creation of a foam pattern and the construction of a mold. However, the use of refractory coatings and the need for precision in creating the foam pattern can add complexity.
- Cost:
- Die Casting: Die casting involves higher initial costs due to the design and fabrication of the die. However, once the die is made, it can be used for a large number of castings, making it cost-effective for high-volume production.
- Lost Foam Casting: The initial cost of tooling for lost foam casting is typically lower compared to die casting since it doesn’t require the fabrication of expensive metal dies. However, the cost of foam patterns and refractory materials can accumulate over time.
- Material Suitability:
- Die Casting: Die casting is commonly used for non-ferrous metals like aluminum, zinc, and magnesium. These metals have favorable properties for die casting, such as low melting points and good fluidity.
- Lost Foam Casting: This method is suitable for a wide range of metals, including aluminum, iron, steel, and various alloys.
- Surface Finish:
- Die Casting: Die castings offer good surface finish, and the mold design can accommodate various details and features. However, die castings may require post-processing, such as machining or polishing, to achieve the desired surface quality.
- Lost Foam Casting: Lost foam castings generally have a good surface finish, with minimal parting lines or flash. The use of foam patterns allows for intricate details and complex shapes to be reproduced accurately.
Die casting is suitable for high-volume production with non-ferrous metals, offering excellent dimensional accuracy and faster production cycles. It requires higher initial costs but provides good surface finish. On the other hand, lost foam casting is cost-effective for small to medium production runs and offers the flexibility to work with a wide range of metals. It is well-suited for producing complex shapes with good surface finish. The choice between the two methods depends on the specific requirements of the project, production volume, material considerations, and desired surface finish.