Sand casting and semi-continuous casting are two different techniques used in metal casting. They have distinct characteristics and are suitable for different applications. Here’s a comparative analysis of sand casting and semi-continuous casting:
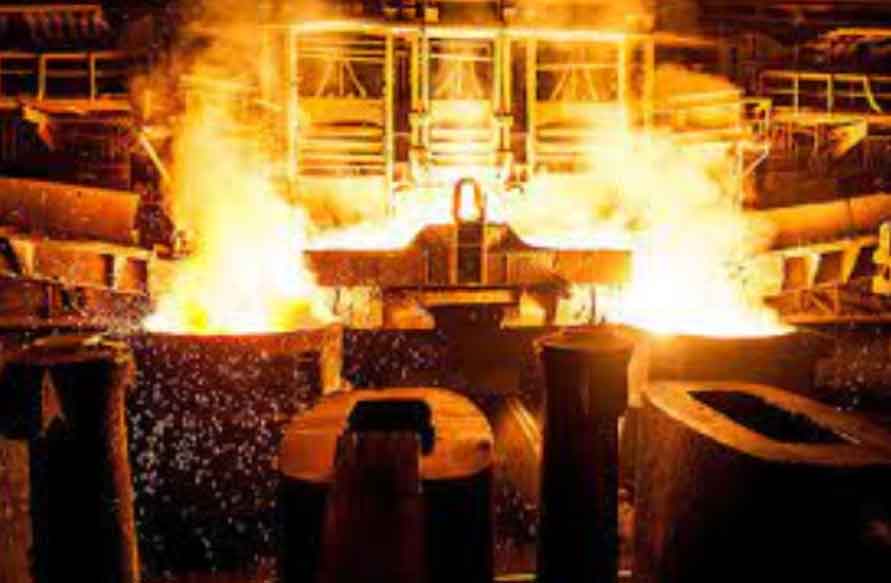
- Process Overview:
- Sand Casting: Sand casting involves creating a mold by packing a mixture of sand and a binder around a pattern. The mold cavity is formed by removing the pattern, and molten metal is poured into the mold. After solidification, the mold is broken to extract the casting. Sand casting is a batch process where each mold is made individually for each casting.
- Semi-continuous Casting: Semi-continuous casting, also known as strand casting or continuous casting, is a process where molten metal is continuously poured into a water-cooled mold to form a solidified strand. The strand is then cut into desired lengths to create individual castings. This process allows for a continuous flow of casting production.
- Efficiency and Productivity:
- Sand Casting: Sand casting is a versatile method that can accommodate various part sizes and shapes. However, it is a slower process compared to semi-continuous casting since each mold is created and cast individually. The cycle time for sand casting is longer, which can limit the production output.
- Semi-continuous Casting: Semi-continuous casting offers higher efficiency and productivity. The continuous flow of molten metal allows for faster production rates, reducing the overall cycle time. The process enables the production of a large number of castings in a shorter time frame.
- Surface Finish and Dimensional Accuracy:
- Sand Casting: Sand casting can produce a range of surface finishes, from rough to relatively smooth, depending on the mold quality and finishing operations. Achieving excellent dimensional accuracy may require additional machining or finishing processes.
- Semi-continuous Casting: Semi-continuous casting typically results in better surface finish and improved dimensional accuracy compared to sand casting. The controlled cooling process in semi-continuous casting helps minimize surface defects and distortion, resulting in more precise castings.
- Complexity and Detail:
- Sand Casting: Sand casting is suitable for casting complex shapes with intricate details. It allows for the incorporation of cores to create internal cavities or features. The flexibility of sand molds makes it possible to cast parts with varying wall thicknesses and intricate geometries.
- Semi-continuous Casting: Semi-continuous casting is generally more suitable for simpler shapes and parts with uniform wall thicknesses. It may not be as effective in reproducing highly complex and detailed geometries as sand casting.
- Casting Material:
- Sand Casting: Sand casting can accommodate a wide range of casting materials, including both ferrous and non-ferrous metals.
- Semi-continuous Casting: Semi-continuous casting is commonly used for non-ferrous metals such as aluminum, copper, and their alloys. It may not be as suitable for casting certain ferrous materials due to the higher cooling rates involved.
Sand casting is versatile and suitable for complex shapes, but it has a slower production rate and may require additional finishing operations. Semi-continuous casting offers higher efficiency, better surface finish, and improved dimensional accuracy, making it suitable for simpler parts with uniform wall thicknesses. The choice between the two methods depends on factors such as part complexity, surface finish requirements, production volume, and material selection.