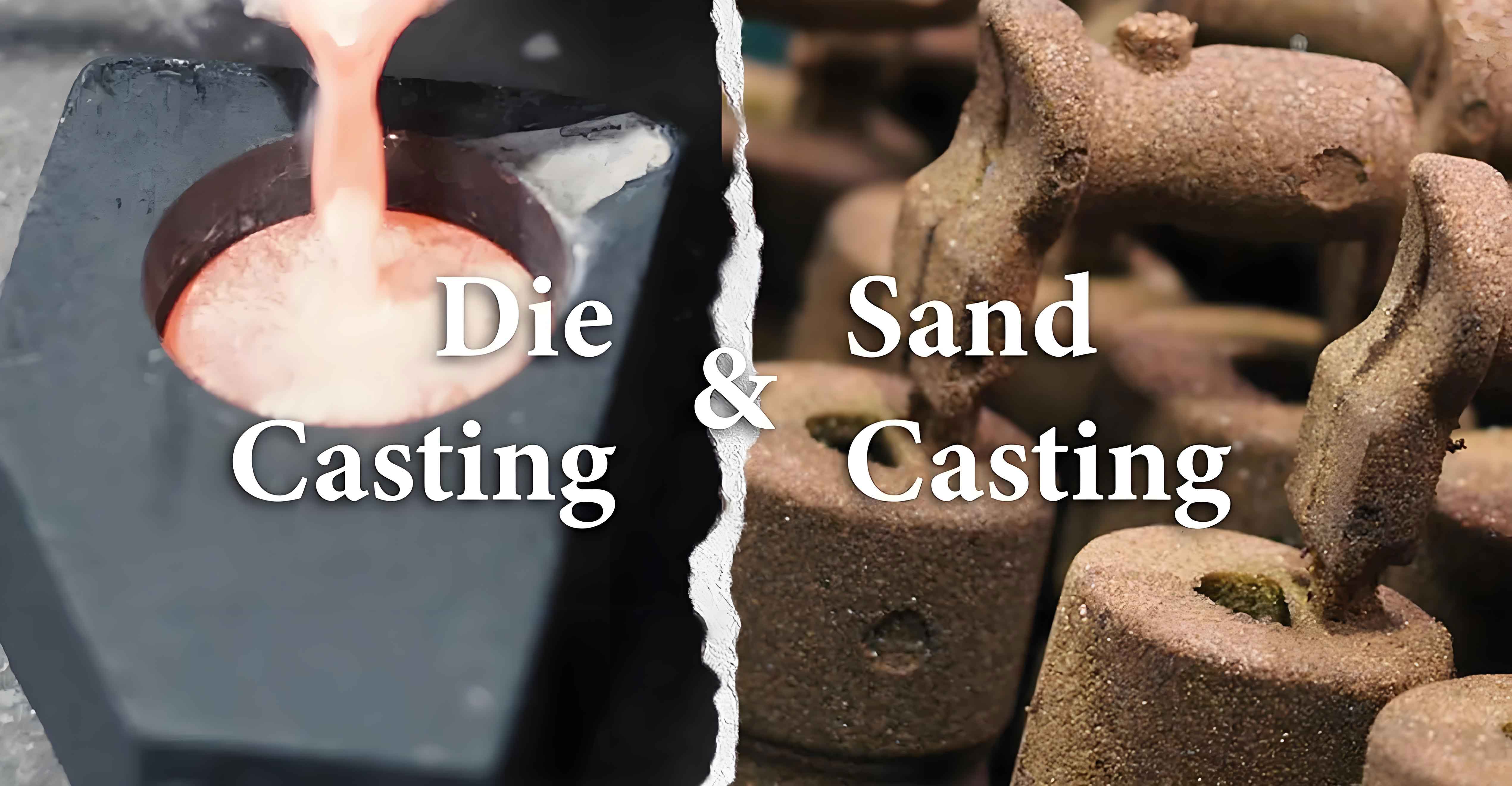
In the world of manufacturing and metal fabrication, die casting and sand casting stand as two principal methods used to create metal parts and components. These processes are essential for a variety of industries, from automotive to consumer goods. Here, we delve into a detailed comparison between die casting and sand casting, focusing on three critical aspects: cost, quality, and production time.
Overview of Die Casting and Sand Casting
Die Casting: Die casting is a metal casting process characterized by forcing molten metal under high pressure into a mold cavity. The mold, typically made from hardened steel, can withstand high temperatures and can be used repeatedly, making die casting suitable for high-volume production runs of small to medium-sized parts.
Sand Casting: Sand casting is one of the oldest casting methods. It involves compacting sand around a pattern and then removing the pattern to leave a cavity into which molten metal is poured. Once the metal solidifies, the sand mold is broken to release the cast part. This method is versatile and cost-effective for producing large and complex parts in small quantities.
Comparison Criteria
- Cost
- Quality
- Production Time
1. Cost Comparison
Casting Process | Tooling Cost | Production Cost | Economies of Scale |
---|---|---|---|
Die Casting | Higher | Lower per unit | Excellent |
Sand Casting | Lower | Higher per unit | Moderate |
Die Casting:
- Tooling Cost: Higher due to the complex and durable steel molds required, which are costly to manufacture but offer longevity.
- Production Cost: Lower per unit as the process allows for rapid production once the die is created, significantly reducing labor costs over large runs.
Sand Casting:
- Tooling Cost: Lower because the sand molds are inexpensive to produce. However, each sand mold can only be used once.
- Production Cost: Higher per unit due to the labor-intensive nature of the process, particularly in setting up and breaking down the sand molds.
2. Quality Comparison
Casting Process | Surface Finish | Dimensional Accuracy | Structural Integrity |
---|---|---|---|
Die Casting | Excellent | High | Superior |
Sand Casting | Moderate | Moderate | Variable |
Die Casting:
- Surface Finish: Produces parts with a high-quality surface finish that often requires minimal finishing work.
- Dimensional Accuracy: Achieves high precision and repeatability, making it ideal for complex, detailed designs.
- Structural Integrity: Parts are generally stronger and denser due to the high pressure used to fill the mold.
Sand Casting:
- Surface Finish: Typically rougher, requiring additional surface finishing processes.
- Dimensional Accuracy: Less precise, suitable for less complex designs or where some variability is acceptable.
- Structural Integrity: Good, but the mechanical properties can be inconsistent due to the nature of the sand mold.
3. Production Time Comparison
Casting Process | Setup Time | Cycle Time | Suitability for Large Batches |
---|---|---|---|
Die Casting | Longer | Very Short | High |
Sand Casting | Shorter | Longer | Low |
Die Casting:
- Setup Time: Initially longer because creating the dies is complex and time-consuming.
- Cycle Time: Once set up, produces parts very quickly due to the fast cooling of metals and the efficiency of the process.
- Suitability for Large Batches: Highly suitable for large-scale production due to fast cycle times and the reusability of molds.
Sand Casting:
- Setup Time: Generally quicker as creating a new sand mold is less complex.
- Cycle Time: Slower, as each mold can only be used once, and the casting and cooling times are longer.
- Suitability for Large Batches: Less efficient for large production runs unless the part size or complexity prohibits the use of die casting.
Conclusion
The choice between die casting and sand casting largely hinges on the specific requirements of your project. Die casting offers advantages in terms of speed, repeatability, and surface quality, making it ideal for high-volume production of small to medium components. Sand casting, on the other hand, is preferred for its flexibility, lower upfront costs, and suitability for larger or more intricate designs. Understanding the distinct benefits of each method will help manufacturers select the optimal process for their production needs, balancing cost, quality, and time effectively.