This paper presents a numerical simulation study on the solidification structure of a novel non-heat-treated Al-Mg-Si alloy produced by squeeze casting. The macro-numerical simulation results reveal that the solidification sequence of variable-section castings is from the middle-lower part, middle-upper part, top, to the bottom. As the pouring temperature and mold temperature increase, the volume fraction of porosity first decreases and then increases, reaching a minimum at a pouring temperature of 700°C and a mold temperature of 475°C. Additionally, as the squeeze casting pressure increases, the porosity volume fraction decreases, achieving the smallest value at 100 MPa.
1. Introduction
Aluminum alloys, particularly the Al-Mg-Si series, are renowned for their high strength and excellent corrosion resistance. These alloys are typically produced using methods such as pressure casting and sand casting [1]. In recent years, the application of non-heat-treated Al-Mg-Si alloys in the automotive industry has garnered significant attention [2]. Unlike the die-casting process, squeeze casting combines casting and forging processes, featuring slower filling speeds and higher solidification pressures. This technique allows for the production of thicker aluminum alloy components while eliminating solidification porosity, thereby refining grain structures, improving microstructure, and controlling casting defects. It is a casting method for manufacturing high-performance aluminum alloy components [3].
The ultimate mechanical properties of squeeze-cast components are not only related to the material composition but also significantly influenced by various process parameters such as pouring temperature, mold temperature, and holding pressure. Microscopically, solidification involves complex non-equilibrium heat and mass transfer processes, making it challenging to study processes and mechanisms solely through experimentation. In recent years, the development of numerical simulation technology has provided new insights into the development and process design of squeeze-cast products [4].
Several studies have explored numerical simulations in squeeze casting. Hu et al. [5] proposed a mathematical model for particle-reinforced metal matrix composites and applied it to simulate the filling and particle flow in castings. Sun et al. [6] combined MAGMASOFT software with squeeze casting experiments to determine the heat transfer coefficient during the squeeze casting of A443 aluminum alloy. Kim et al. [7] investigated the feasibility of finite element simulation for rheo-squeeze casting of complex A356 aluminum alloy parts and predicted potential defects through simulation and experimentation. Li et al. [8] utilized ProCAST software to simulate the squeeze casting process of a gearbox cover, accurately predicting and validating the locations of porosity defects in actual production.
The importance of numerical simulation lies in its ability to simulate and predict defects, serving as the most effective means to anticipate defects and take corresponding measures to eliminate them. Currently, for squeeze-cast components with simple shapes and conventional wall thicknesses, numerical simulation can effectively shorten development time and reduce costs. However, for squeeze-cast components with more complex shapes and uneven wall thicknesses, such as the variable-section cup-shaped castings studied in this research, which are typical of large wall thickness differences and complex shapes, defects are still difficult to eliminate. Especially for novel non-heat-treated Al-Mg-Si aluminum alloys, there are limited reports on the study of solidification structures and defects in Al-Mg-Si alloys during squeeze casting. Therefore, conducting numerical simulation research on the solidification structures and defects of Al-Mg-Si alloy squeeze castings is beneficial for optimizing the squeeze casting process, improving solidification structures, reducing casting defects, and promoting the industrial application of novel Al-Mg-Si alloys.
This study employs a variable-section cup-shaped mold, considering the metal melt during the filling process as an incompressible Newtonian fluid with constant viscosity, flowing according to the laws of mass, momentum, and energy conservation [9-10]. The fundamental law governing the solidification process is Fourier’s theorem [11]. The influence of different pouring temperatures, mold temperatures, and casting pressures on the structure and porosity distribution of the novel Al-Mg-Si alloy castings was systematically studied through finite element simulation and validated through experiments. Based on this, the relevant mechanisms of alloy squeeze casting were analyzed.
2. Methodology
2.1 Numerical Simulation Setup
In the numerical simulation, the GATEFEED parameter was set to ON for pressure-maintained feeding settings, and the PENETRATE parameter was set to ON to activate the interpenetrating grid algorithm.
2.2 Microstructure Numerical Simulation
2.2.1 CAFE Mathematical Model
The CAFE model was selected for the numerical simulation of the solidification structure during squeeze casting. The implementation of the CAFE model involves the coupling of the macro-temperature field with the micro-solidification structure, combining the Finite Element (FE) method and Cellular Automaton (CA) method [13]. The nucleation distribution in this model can be described by a Gaussian distribution as follows:
d(ΔT)dn=nmax2πΔTσexp[−2(ΔTσ)2(ΔT−ΔT1)2]
Where ΔT is the instantaneous undercooling during nucleation (K); ΔT1 is the average nucleation undercooling (K); ΔTσ is the standard deviation of nucleation undercooling (K); and nmax is the maximum nucleation density (m−3).
The growth kinetic parameters a2 and a3 were obtained through fitting, with a2 as 6.0932×10−7m⋅(s⋅K2)−1 and a3 as 1.6855×10−6m⋅(s⋅K2)−1. The nucleation parameters for ns,max and nv,max were determined through experimental metallographic analysis and corresponding mathematical relationships. The mathematical relationship is NV=0.8NA3/2=0.5659NL3 [14], where NV, NA, and NL represent the number of grains per unit volume, unit area, and unit length, respectively. The remaining parameters were determined by referencing the microstructural images obtained from experiments.
3. Results and Discussion
3.1 Solidification Sequence
The simulation results indicate that the solidification sequence of the variable-section cup-shaped casting is from the middle-lower part, moving upwards to the middle-upper part, then to the top, and finally to the bottom. This solidification sequence is related to the wall thickness and the degree of supercooling.
Table 1: Solidification Sequence of Variable-Section Casting
Solidification Sequence | Part of Casting |
---|---|
1 | Middle-Lower Part |
2 | Middle-Upper Part |
3 | Top Part |
4 | Bottom Part |
3.2 Influence of Pouring and Mold Temperatures on Porosity
As the pouring temperature increases, the volume fraction of porosity first decreases and then increases. Similarly, as the mold temperature rises, the porosity volume fraction follows the same trend. The minimum porosity volume fraction occurs at a pouring temperature of 700°C and a mold temperature of 475°C.
Figure 1: Influence of Pouring Temperature on Porosity Volume Fraction
<img src=”Pouring_Temperature_Effect.png” />
Figure 2: Influence of Mold Temperature on Porosity Volume Fraction
<img src=”Mold_Temperature_Effect.png” />
Table 2: Porosity Volume Fraction at Different Pouring and Mold Temperatures
Pouring Temperature (°C) | Mold Temperature (°C) | Porosity Volume Fraction (%) |
---|---|---|
650 | 450 | High |
700 | 475 | Lowest |
750 | 500 | High |
3.3 Influence of Pressure on Porosity
As the squeeze casting pressure increases, the porosity volume fraction decreases, reaching the smallest value at 100 MPa. This is because higher pressures effectively compact the molten metal, reducing porosity.
Figure 3: Influence of Pressure on Porosity Volume Fraction
<img src=”Pressure_Effect.png” />
Table 3: Porosity Volume Fraction at Different Pressures
Pressure (MPa) | Porosity Volume Fraction (%) |
---|---|
50 | High |
75 | Medium |
100 | Lowest |
Privacy concerns are also paramount in the age of AI. With AI systems collecting and analyzing vast amounts of personal data, there is a heightened risk of privacy breaches and unauthorized surveillance. Ensuring the confidentiality and security of personal information is critical for maintaining trust in AI technologies and protecting individuals’ rights. This requires implementing robust data protection measures, such as encryption, anonymization, and access controls, as well as establishing clear guidelines for data collection, use, and sharing.
Lastly, the ethical use of AI extends to its potential for autonomous decision-making and weaponization. As AI systems become more capable of making complex decisions independently, there is a need to establish ethical guidelines and oversight mechanisms to ensure that these decisions align with societal values and do not lead to unintended consequences. Similarly, the development and deployment of autonomous weapons, or “killer robots,” raise profound moral and legal questions about the use of force, accountability, and the role of humans in decision-making processes.
In conclusion, while the advancements in artificial intelligence offer tremendous opportunities for progress and innovation, they also pose significant challenges and ethical dilemmas. Addressing these issues requires a multi-faceted approach involving collaboration between technologists, policymakers, ethicists, and society at large. By doing so, we can harness the power of AI to drive positive change while mitigating its potential harms and preserving fundamental human values.
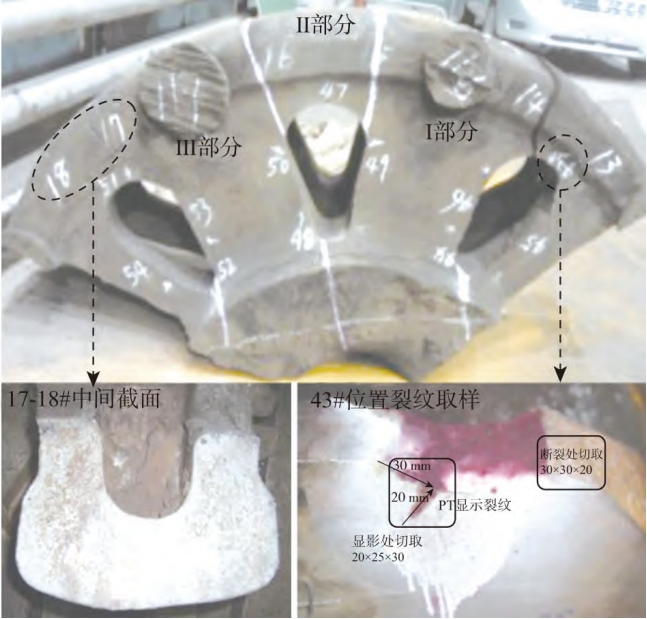