1 Introduction
In recent years, with the continuous improvement of environmental requirements, our company has changed the original cupola and insulation furnace dual melting process to medium frequency induction furnace melting process to meet environmental requirements. After changing to the electric furnace melting process, environmental issues were resolved, but some of the products produced had abnormal quality, especially a large hole defect in the fuel nozzle area after processing a 4-cylinder cylinder cylinder head. To this end, our company has made various improvements, ultimately effectively reducing the occurrence rate of this defect.
2 Process Introduction
2.1 Basic Process
Product Outline Size: 467 × one hundred and seventy-five × ninety-five
Single piece weight: 33Kg
Material grade: HT300
2.2 Casting process
Typing method: horizontal typing
Styling line: GF line air impact molding, 4-piece/type
Core laying method: core laying fixture for core laying
3 Defect Analysis and Countermeasures
3.1 Defect location and characteristics
By dissecting and confirming the defect area, it was found that the internal surface of the defect is very smooth, which is in line with the characteristics of the gas hole defect. The location of the defect is very concentrated, located at the middle two fuel injection nozzles, and the two near the two ends do not have the defect. The specific location of the defect is shown in Figure 1:
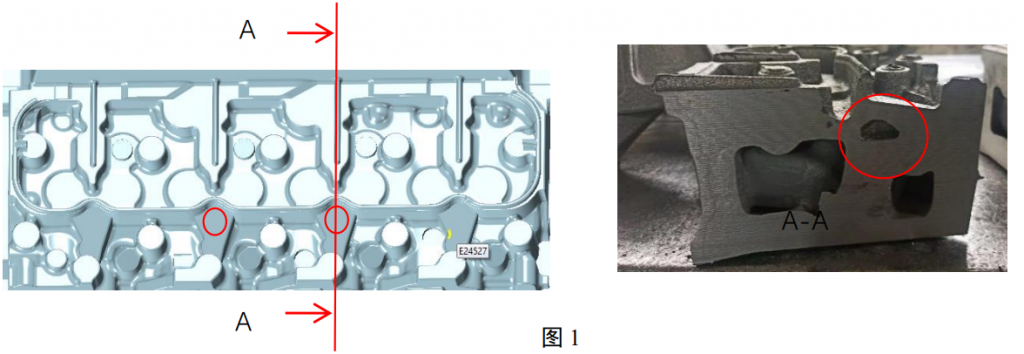
Figure 1
3.2 Analysis of the causes of defects
This product is an old one. Before changing the electric furnace melting process, the occurrence rate of the fuel nozzle air hole in the product was always controlled within 0.5%. After changing to an electric furnace, the average occurrence rate of this defect was as high as about 10%, and it is very unstable, with some batches reaching as high as about 20%.The following analysis was conducted on the reasons for this occurrence:
1) From the cross-sectional view in Figure 1, it can be seen that this hole is very large, so it is suspected that it may be due to the local pouring of shuttle water, causing the gas in the mold cavity to not be discharged smoothly and forming a large pore defect in this area;
2) By tracking the production process, it was found that some box numbers had poor exhaust of the water jacket, so it is suspected that there is a blockage in the main exhaust channel of the water jacket core, leading to poor exhaust of the water jacket core;
3) From the cross-section in Figure 2, we can see that the hot spot here is relatively large, so the analysis may indicate that the hot spot in this area is too large, Large shrinkage defects were generated (during the later solidification stage of the casting, the gas solute in the liquid phase at the hot spot is highly concentrated, and the liquid phase at the hot spot undergoes volume shrinkage, creating vacuum holes, creating conditions for gas precipitation. At the same time, the generated gas also hinders the filling of the metal liquid, ultimately forming large hole defects in the thick parts of the hot spot).
At the same time, the hole defects after processing are mainly concentrated in the middle two fuel injection nozzles (the middle of the casting is also equivalent to the middle of the sand box, and the temperature in the middle should be the highest, while the temperature near the edge should be relatively low), which further proves the speculation of shrinkage defects.
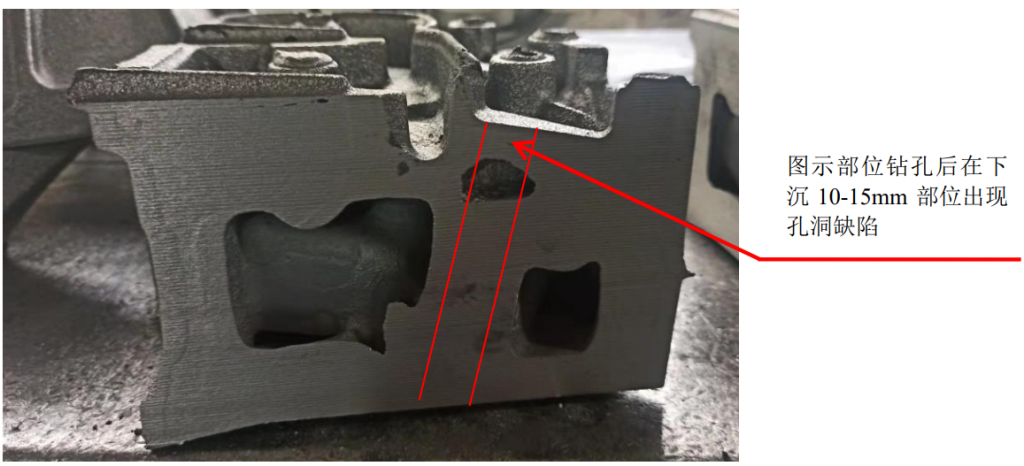
Figure 2
3.3 Measures Development
1) Problem with pouring shuttle water: Through on-site tracking and observation, it was found that there were slight shuttle water phenomena in some boxes. So, first, perform sealing verification on the core head of the airway: seal all the core head parts with sealing strips (as the lower mold of the product is formed by clay core, and the upper mold is formed by casting, there may be shuttle water phenomenon when there is deviation in the box); Adjust the fit gap between the airway and the tray to prevent molten iron from entering the tray during pouring and reducing void;
2) Blockage of the main exhaust channel of the water jacket: Through a thorough inspection and confirmation of the water jacket cores in production, it was found that there is indeed a certain proportion (3% -5%) of the main exhaust channel blockage in certain batches of water jacket cores. Given that this situation is uncontrollable, (the reason is: firstly, there are fluctuations in the coating sand and core making process, making it difficult to ensure consistency; secondly, the wall thickness of the water jacket core varies greatly, and the thick parts cannot be completely solidified. During the polishing and flipping of the water jacket, loose sand that has not been solidified in the thick parts enters the main exhaust channel of the water jacket, causing blockage in the exhaust channel.) Therefore, we take a measure: after the clay core is removed from the core making machine, Firstly, insert the steel needle directly into the main exhaust channel of the water jacket, and after one polishing, dipping, baking until the second polishing is completed, the steel needle can be removed. This ensures the secondary solidification of the main exhaust channel of the water jacket, and loose sand will not flow into the main exhaust channel;
3) Shrinkage defect: Through analysis of the structure of this area, it is suspected that the possibility of gas gathering towards the hot spot due to shrinkage is high. Therefore, we made an accompanying external cold iron in this area for trial production verification (see Figure 3).
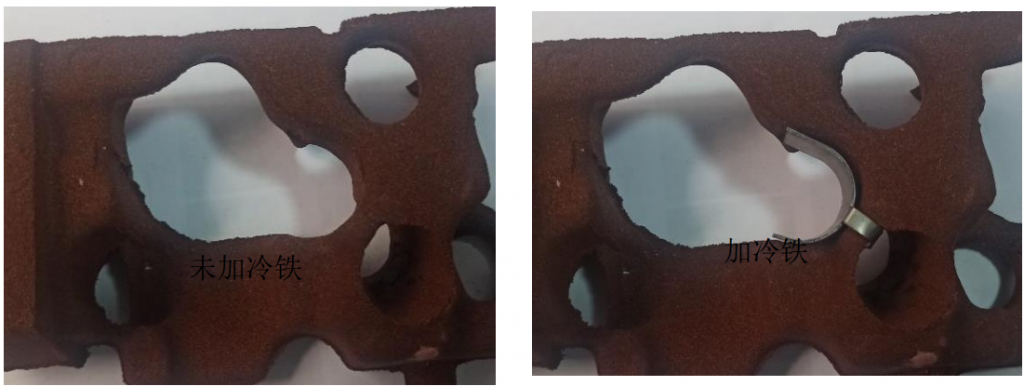
Figure 3
Effect of 4 measures
1) Take sealing measures for the airway core head and ensure that the airway is After adjusting the clearance of the tray, the pouring is basically free from water shuttling and the pouring is very smooth. But after processing, the occurrence rate of nozzle air holes is still not high How much change there has been;
2) Blockage of the main exhaust channel of the water jacket core, measures to be taken After tracking and inspecting 3000 pieces, no blockage was found in the main exhaust channel of the water jacket, but the defect of the fuel injection nozzle air hole was still not resolved Transfer;
3) Add external cooling iron, adopt external cooling iron process, and process and verify The defect has significantly improved, from the original 10% to 0.2%.
5 Conclusion
Through this rectification, after conducting electron microscopy scanning, it was found that:,Although it conforms to the characteristics of pores, based on our analysis of this type of defect From the perspective of rectification and the results achieved, it is mainly due to the Shrinkage caused. That is to say, while forming shrinkage cavities at the hot spot, The gas in the mold cavity also accumulates towards the hot spot, resulting in the hot spot area Large hole defects appear. So we believe that improving this type of
Defects can be solved from two aspects: firstly, from the perspective of shrinkage, either increasing the feeding system or reducing the hot spot; Secondly, From the perspective of gas, the first step is to maximize the size of the clay core and exhaust the mold cavity as much as possible The system ensures a smooth exhaust system, followed by a reduction in core gas generation Measures such as quantity.