Based on the previous calculation methods and results, some calculation factors have been modified by zhougengao Engineering Co., Ltd., and a new calculation method has been proposed to comprehensively consider the various stages of solidification process of nodular cast iron. The volume change in the solidification process is more accurately calculated, and it is concluded that no matter what process is used, the nodular iron casting always needs feeding [8]. According to the volume change model diagram of the theory, Hong HENGFA of Dongfeng Automobile Foundry Research Laboratory drew the schematic diagram of feeding method model of nodular cast iron as shown in Figure 1 below, and worked out the guidance on how to select riser according to the casting modulus. The feeding methods and riser selection methods of general riser, control pressure riser, full pressure riser and riser free casting were classified and explained.
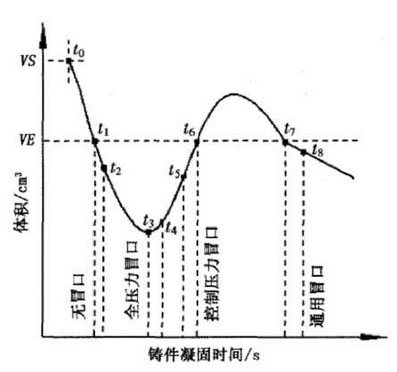
(1) The feeding time of general riser is from the beginning of liquid shrinkage (T0) to the end of secondary shrinkage (T7), or even longer (T8). The feeding and feeding of general riser follows the principle of sequential solidification, that is, the solidification of riser neck is later than that of casting, and the solidification of riser is later than that of riser neck. The liquid shrinkage of casting is supplied by riser, and the molten metal is squeezed back to the riser when the casting enters eutectic expansion period. The shrinkage porosity defect in the later solidification stage can be eliminated by the gravity of liquid metal.
(2) The control pressure riser is that after pouring, the riser supplies the liquid shrinkage of the casting. In the early stage of eutectic solidification, the riser neck is unobstructed, so that the inner metal of the casting is backfilled with the riser to release the pressure. When the eutectic solidification is not finished, the riser neck is timely closed to control the backfill degree, and a moderate internal pressure is established in the casting by partial eutectic expansion to offset the secondary shrinkage defects.
(3) The full pressure riser is used to feed the liquid shrinkage of the casting. When the eutectic solidification begins (T3) or the expansion begins in a short time (T4), the riser neck is completely closed. In this way, the liquid metal will not return to the riser because of eutectic expansion, so that the liquid metal is under positive pressure and completely depends on graphite expansion to offset the secondary shrinkage.
(4) Riser free casting means that the liquid metal is fed through the gating system before it is cooled to (T1). When the molten metal is cooled to T1, the residual expansion is greater than or equal to the residual shrinkage. Therefore, riser free casting is not a non feeding casting. Its feeding principle is to make full use of graphitization expansion to the maximum extent or even 100%, and the gating system is used to supplement the liquid shrinkage in the early stage.
When Wu Hebao of Huazhong University of science and technology cooperated with Jiangling foundry to develop the wheel hub casting of Quanshun front axle, it was found that the cause of shrinkage porosity was that there was a thin arm structure split with small modulus, which blocked the feeding channel of molten iron during solidification, so that the feeding function of riser could not be transferred to isolated hot spot, as shown in Figure 2 below.

The key to eliminate the defect is to overcome the blocking effect of small modulus thin arm separation, keep the feeding channel unblocked or accelerate the solidification of isolated hot spot area, so that the large hot spot area solidifies before the feeding channel. Based on the above two points, cold iron is set at the hot spot to improve the cooling speed of hot spot to eliminate shrinkage porosity, or chromite ore sand with high thermal conductivity is used as sand core material to improve the heat dissipation effect at hot spot, so as to eliminate shrinkage porosity. Through the practice verification, all can achieve the expected effect.