In the context of the fourth industrial revolution, the sand casting industry is facing challenges such as complex processes and unbalanced data. This article focuses on the defect prediction of construction machinery castings in the sand casting process. It proposes a convolutional neural network defect prediction method based on feature redistribution and cost – sensitive learning. The article details the construction and optimization of the model, analyzes the defect evolution law, and verifies the effectiveness of the method through experimental data. The research results provide a new solution for improving the quality and production efficiency of sand casting.
1. Introduction
1.1 Background
In the era of the fourth industrial revolution, digital transformation has become a key trend in the manufacturing industry. Sand casting, as one of the important manufacturing processes, is also facing the need for innovation and improvement. The traditional sand casting process involves multiple complex procedures, and the interaction between process parameters makes it difficult to ensure product quality. Moreover, the imbalance of data in the actual production process further complicates the defect prediction and quality control of castings.
1.2 Research Significance
The research on defect prediction in sand casting is of great significance for improving product quality, reducing production costs, and enhancing the competitiveness of enterprises. By accurately predicting defects, manufacturers can take timely measures to adjust the process, reduce waste, and improve production efficiency. This study aims to address the challenges in sand casting defect prediction and provide a practical and effective solution.
1.3 Research Objectives and Scope
The main objective of this research is to develop a defect prediction model for construction machinery castings in the sand casting process. The scope of the study includes the collection and analysis of casting process data, the construction and optimization of the prediction model, and the exploration of the relationship between process parameters and defect formation. The research focuses on common defects such as sand holes, pores, shrinkage cavities, and cold shuts.
2. Literature Review
2.1 Previous Research on Casting Defect Prediction
Researchers around the world have been actively exploring defect prediction methods in casting. For example, A. S. Normanton et al. in the UK used the MLP network to improve the quality prediction system. S. Hore et al. in India analyzed the influence of processing parameters on defects in the continuous casting process and built a neural network model to predict the probability of defects. Lee et al. in South Korea proposed an error – weighted deep neural network model to reduce prediction errors. In China, scholars such as Dou Yihua and Zhang Long also made contributions in related fields.
2.2 Limitations of Existing Research
Although previous studies have achieved certain results, there are still some limitations. Some methods may not be suitable for complex sand casting processes with multiple parameters and strong coupling. The problem of data imbalance has not been effectively addressed in some models, resulting in inaccurate prediction of minority defect samples. In addition, the interpretability of the model and the analysis of the defect evolution law need to be further strengthened.
2.3 Research Gaps and the Need for This Study
Based on the above analysis, there is a need for a more effective defect prediction method that can handle complex sand casting data and address the issue of data imbalance. This study proposes a new approach to fill these gaps and provide a more accurate and practical defect prediction model for the sand casting industry.
3. Data Collection and Preprocessing
3.1 Data Sources
The data used in this study were collected from a sand casting enterprise. The data cover the key casting process parameters of steering axles, slewing frames, and axle housings, including 18 parameters related to sand mixing, metal melting, and pouring processes. The data were obtained through on – site sensors and production records.
3.2 Data Cleaning and Preprocessing
The collected data may contain noise and outliers. Therefore, data cleaning was performed to remove abnormal values and fill in missing data. Additionally, the data were normalized to ensure that all parameters were within a similar range, which is beneficial for the training and performance of the neural network model.
3.3 Data Analysis and Visualization
Descriptive statistical analysis was conducted on the preprocessed data to understand the distribution and characteristics of each parameter. Visualization methods such as histograms and scatter plots were used to display the data, providing an intuitive understanding of the relationship between parameters and potential defect patterns.
4. Defect Prediction Model Construction
4.1 Feature Redistribution
4.1.1 Principle and Motivation
The order of feature vectors can affect the performance of the neural network model. In traditional methods, simple concatenation of features may lead to the combination of strongly correlated features, resulting in the loss of information on weakly correlated feature combinations. Therefore, feature redistribution is proposed to optimize the arrangement of feature vectors.
4.1.2 Implementation Steps
The Pearson correlation coefficient matrix of the 18 process parameters was converted into a weight matrix. Then, all possible pairwise combinations of the 18 parameters were generated, and these combinations were sorted based on the weights. Finally, using the greedy algorithm, the optimal combination of features was selected to achieve global optimization.
4.2 Cost – Sensitive Optimization
4.2.1 Handling Data Imbalance
In the collected data, the number of qualified castings is much larger than that of defective castings, resulting in a serious imbalance in the data. This imbalance can cause the model to be biased towards the majority class and ignore the characteristics of minority defect samples.
4.2.2 Cost – Sensitive Learning Mechanism
Cost – sensitive learning was introduced to address this issue. By assigning different prediction costs to different categories in the loss function, the model can pay more attention to minority defect samples. The specific implementation is to add a regularization term containing a cost matrix to the original loss function.
4.3 Model Architecture and Training
4.3.1 FR – CS – CNN Model Structure
The proposed FR – CS – CNN model is based on a one – dimensional convolutional neural network. It consists of an input layer, multiple convolutional layers, pooling layers, fully connected layers, and an output layer. The convolutional layers are used to extract local features, and the pooling layers are used to reduce the dimensionality of the data. The fully connected layers are used for classification.
4.3.2 Training Process and Parameter Settings
The model was trained using the preprocessed data. The training process involved optimizing the model parameters to minimize the loss function. The learning rate, batch size, and number of epochs were adjusted to achieve the best training results. Cross – validation was also used to evaluate the generalization ability of the model.
5. Model Evaluation and Comparison
5.1 Evaluation Metrics
5.1.1 Accuracy, Precision, Recall, and F1 – Score
Accuracy measures the overall correctness of the model’s predictions. Precision reflects the proportion of correctly predicted positive samples among all predicted positive samples. Recall indicates the proportion of correctly predicted positive samples among all actual positive samples. The F1 – score is a comprehensive metric that balances precision and recall.
5.1.2 Confusion Matrix
The confusion matrix provides a detailed view of the model’s predictions for each category. It shows the number of true positives, false positives, true negatives, and false negatives, allowing for a more in – depth analysis of the model’s performance.
5.2 Comparison with Other Models
5.2.1 MLP and CNN Models
The performance of the FR – CS – CNN model was compared with that of the traditional MLP and CNN models. The results showed that the FR – CS – CNN model achieved higher accuracy and better performance in handling data imbalance.
5.2.2 Improvement and Significance
The improvement in the FR – CS – CNN model is mainly due to the feature redistribution and cost – sensitive learning strategies. These strategies enable the model to better capture the characteristics of the data and improve the prediction accuracy of minority defect samples, which is of great significance for practical production.
6. Defect Evolution Law Analysis
6.1 Single – Factor Analysis
6.1.1 Influence of Shear Strength
The analysis of the influence of shear strength on defects showed that sand holes are more likely to occur at lower shear strengths. Therefore, in actual production, it is necessary to control the shear strength above a certain value to reduce the occurrence of sand holes.
6.1.2 Effect of C Content
The C content has an impact on the formation of cold shuts. Higher C content may increase the probability of cold shuts. Therefore, appropriate control of the C content is required to ensure casting quality.
6.1.3 Impact of Pouring Temperature
Pouring temperature affects the formation of cold shuts and pores. Low pouring temperatures can lead to the formation of cold shuts and pores. Therefore, it is important to ensure an appropriate pouring temperature to avoid these defects.
6.2 Multi – Factor Interaction Analysis
6.2.1 Shear Strength – Compactness Rate Interaction
The interaction between shear strength and compactness rate has a significant impact on the formation of pores. In certain ranges of shear strength and compactness rate, the probability of pore formation increases significantly. Therefore, these parameters need to be carefully controlled in production.
6.2.2 C Content – Mg Content Interaction
The interaction between C content and Mg content mainly affects the formation of shrinkage cavities and cold shuts. Understanding this interaction can help optimize the process parameters to reduce the occurrence of these defects.
6.2.3 Pouring Temperature – Inoculant Dosage Interaction
The interaction between pouring temperature and inoculant dosage also affects the quality of castings. Appropriate control of these two parameters can ensure good casting quality and reduce the occurrence of defects.
7. Conclusion and Future Work
7.1 Summary of Research Findings
This study proposed a defect prediction method based on feature redistribution and cost – sensitive learning for sand casting of construction machinery castings. The method effectively addressed the problems of data imbalance and complex process parameters. The FR – CS – CNN model achieved high prediction accuracy and provided valuable insights into the defect evolution law.
7.2 Contributions to the Field
The research contributions include the development of an effective defect prediction model, the exploration of the relationship between process parameters and defect formation, and the provision of a practical solution for improving the quality of sand casting.
7.3 Limitations and Future Research Directions
Although the proposed method has achieved good results, there are still some limitations. For example, the model may need to be further optimized for different types of castings and defects. Future research can focus on improving the model’s generalization ability, exploring more advanced machine learning algorithms, and integrating the defect prediction model with the actual production process for real – time quality control.
7.4 Implications for the Industry
The research results have important implications for the sand casting industry. They can help enterprises improve product quality, reduce production costs, and enhance competitiveness. The proposed method can be applied in actual production to guide process optimization and quality control.
8. Appendix
8.1 List of Process Parameters
Parameter Name | Unit | Range |
---|---|---|
Compactness Rate | % | 35.07 – 48.82 |
Shear Strength | kPa | 2 – 6 |
Old Sand Temperature | °C | 33.4 – 48.8 |
Old Sand Moisture | % | 1.38 – 2.38 |
Bentonite | % | 19.9 – 33.2 |
Mixed Soil | % | 9.8 – 19.7 |
New Sand | % | 0 – 40 |
C | % | 3.61 – 3.85 |
Si | % | 2.6 – 2.92 |
Mn | % | 0.38 – 0.66 |
P | % | 0.013 – 0.047 |
S | % | 0.006 – 0.018 |
Mg | % | 0.034 – 0.057 |
Al | % | 0.017 – 0.054 |
Pouring Temperature | °C | 1385 – 1415 |
Pouring Weight | kg | 128 – 145 |
Pouring Time | s | 11.9 – 30.5 |
Inoculant Dosage | g | 24 – 92 |
8.2 Sample Data
Compactness Rate | Shear Strength | Old Sand Temperature | Old Sand Moisture | Bentonite | Mixed Soil | New Sand | C | Si | Mn | P | S | Mg | Al | Pouring Temperature | Pouring Weight | Pouring Time | Inoculant Dosage | Defect Type |
---|---|---|---|---|---|---|---|---|---|---|---|---|---|---|---|---|---|---|
40.5 | 3.5 | 40.2 | 1.8 | 25.5 | 12.5 | 15 | 3.7 | 2.75 | 0.5 | 0.025 | 0.01 | 0.045 | 0.03 | 1395 | 135 | 20 | 50 | Sand Hole |
42.8 | 4.2 | 43.5 | 2.1 | 28.2 | 15.3 | 20 | 3.8 | 2.8 | 0.55 | 0.03 | 0.012 | 0.048 | 0.035 | 1405 | 140 | 25 | 60 | Pore |
38.5 | 3.2 | 38.8 | 1.6 | 22.5 | 11.2 | 12 | 3.65 | 2.65 | 0.45 | 0.02 | 0.008 | 0.042 | 0.025 | 1388 | 132 | 18 | 45 | Shrinkage Cavity |
45.5 | 4.8 | 46.5 | 2.2 | 30.5 | 17.5 | 25 | 3.82 | 2.85 | 0.6 | 0.035 | 0.015 | 0.052 | 0.04 | 1410 | 142 | 28 | 70 | Cold Shut |
43.2 | 4.5 | 44.2 | 2.0 | 27.5 | 14.5 | 18 | 3.75 | 2.78 | 0.58 | 0.032 | 0.013 | 0.046 | 0.038 | 1398 | 138 | 22 | 55 | Qualified |
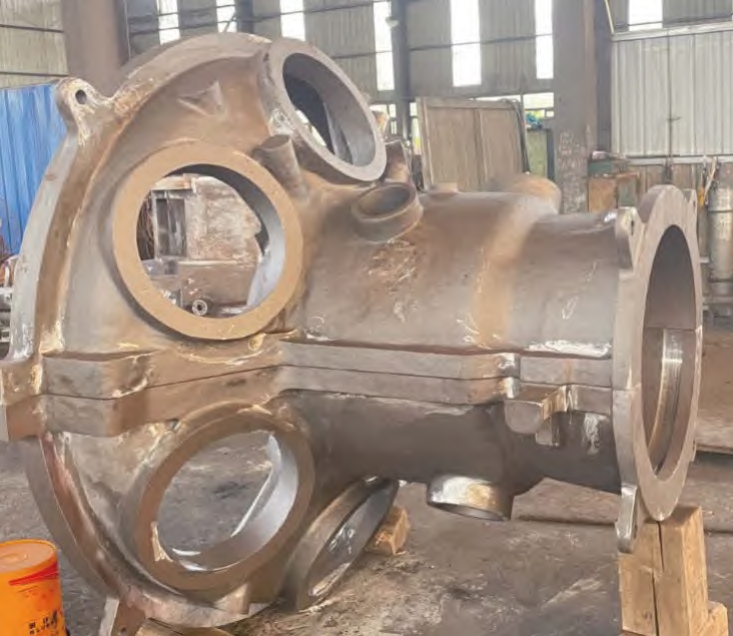