Fig. 1 is the variation curve between mechanical properties and amplitude of EPC ductile iron. It can be seen from Figure 1 that the tensile strength of lost foam casting nodular cast iron increases with the increase of amplitude. However, compared with the nodular cast iron prepared with the amplitude of 0.75mm, the increase of tensile strength of nodular cast iron prepared with the amplitude of 2mm is very small, which is mainly related to the small difference in the structure of nodular cast iron prepared under the two conditions, including the number of graphite balls per unit area Pearlite content, etc. The tensile strength of nodular cast iron continues to increase when the amplitude of vibration lost foam casting is further increased. When the amplitude is 4mm, the tensile strength of nodular cast iron reaches 674mpa, which is 26.63% higher than that of nodular cast iron prepared when the amplitude is 0,75mm. Therefore, when the vibration frequency is 35Hz, the selection of larger amplitude parameters is conducive to improve the tensile strength of vibration lost foam casting ductile iron.
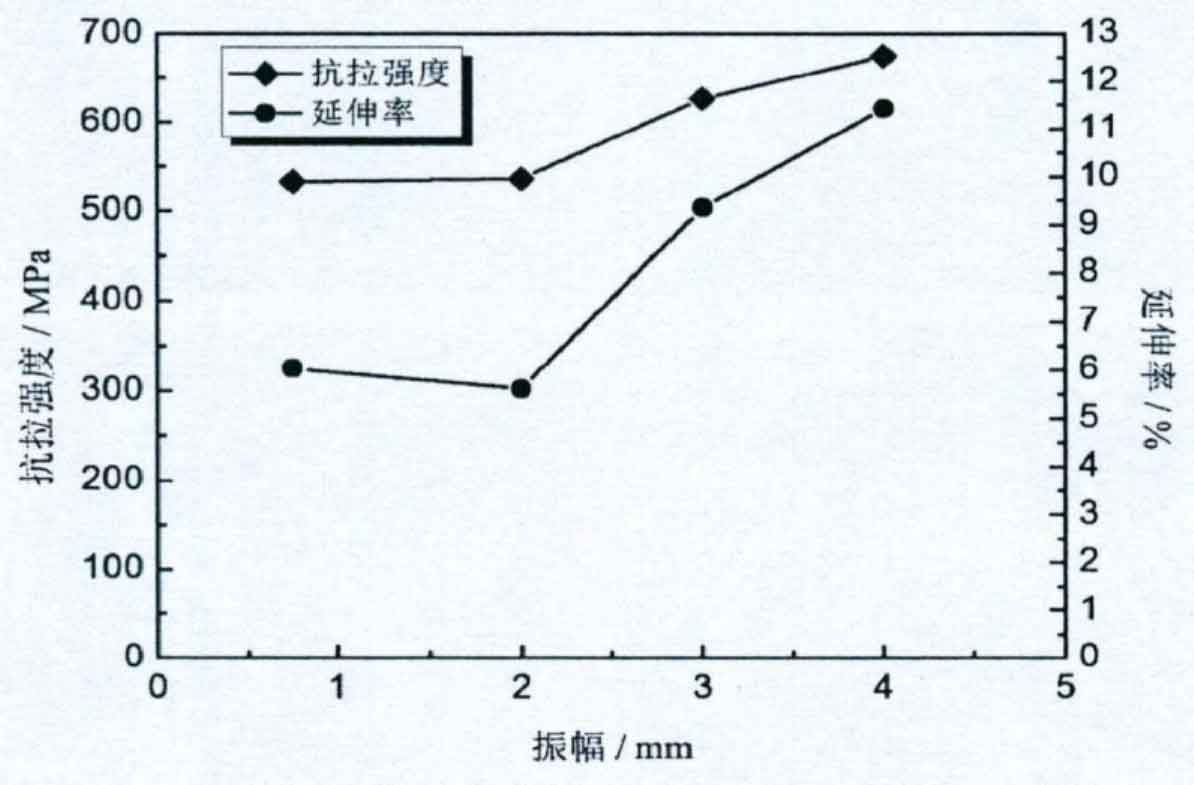
In addition, it can be seen from Figure 1 that the elongation of nodular cast iron decreases first and then increases with the increase of amplitude. The pearlite content of nodular cast iron prepared under the condition of 2mm amplitude is more than that of nodular cast iron prepared under the condition of 0.75mm amplitude. In addition, the number of deformed graphite in the nodular cast iron prepared by this process is more, the graphite morphology is poor, and the ability of the matrix to resist plastic deformation is weakened. Therefore, its elongation is lower than that of nodular cast iron prepared under the condition of 0.75mm amplitude. When the amplitude increases to 3mm, the elongation of nodular cast iron increases because the pearlite content in nodular cast iron decreases, the number of graphite balls per unit area is more, the spheroidization rate is higher, and the shape of graphite balls is better. When the amplitude is further increased to 4mm, the elongation of nodular cast iron in vibration lost foam casting is larger, which is 11.43%. This is the result of the joint action of the number, morphology and distribution of graphite balls in the nodular cast iron prepared by this process, as well as the pearlite and ferrite in the matrix structure.
Figure 2 shows the fracture morphology of nodular cast iron prepared under different amplitude conditions. Figures 2 (a) – (d) show the fracture morphology of nodular cast iron prepared under the conditions of amplitude of 0.75mm, 2mm, 3mm and 4mm respectively.
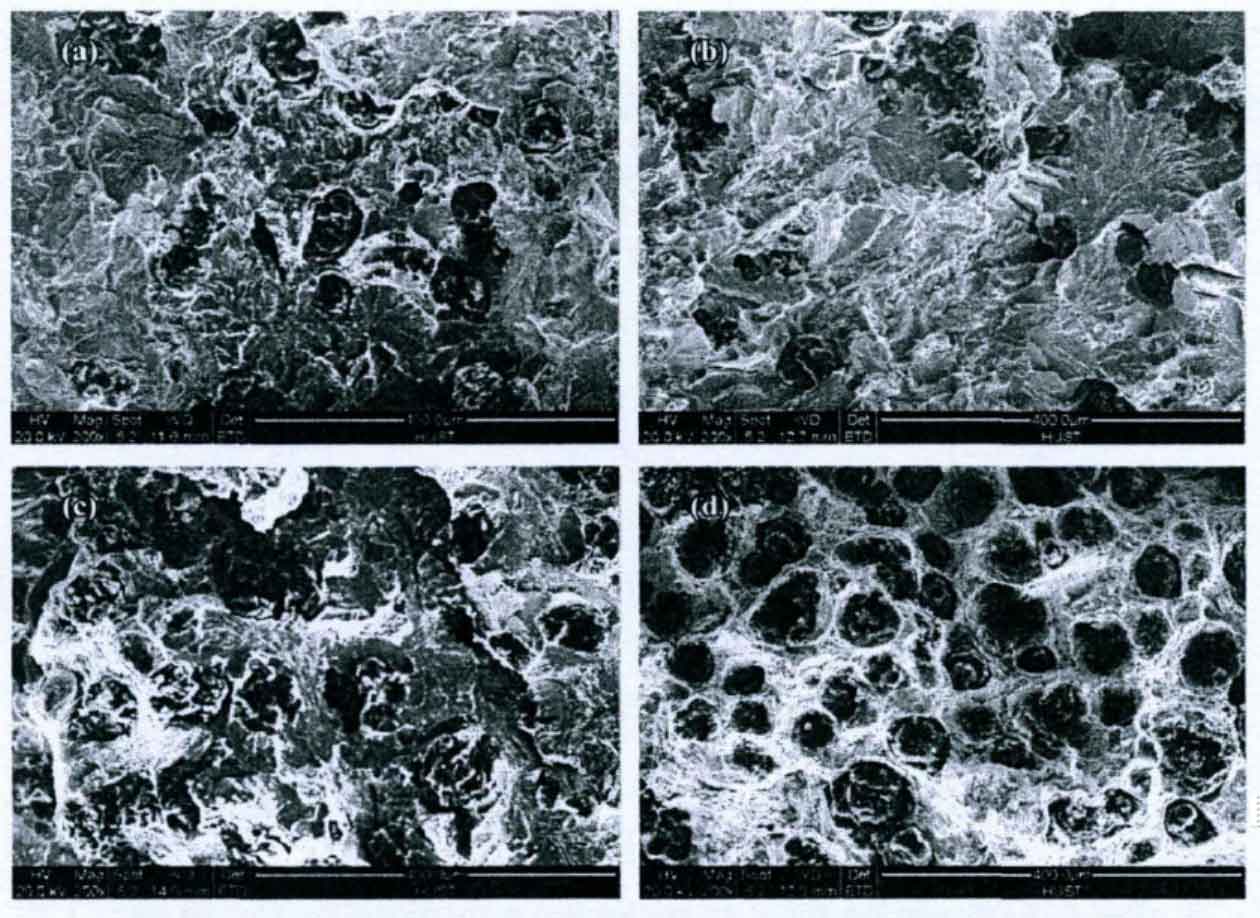
It can be seen from Fig. 2 that the fracture of nodular cast iron prepared at the amplitudes of 0.75mm, 2mm and 3mm presents the cleavage fracture mechanism of river pattern; However, when the amplitude is 4mm, a large number of dimples are distributed on the fracture surface of nodular cast iron, and the fracture of nodular cast iron prepared by this process belongs to ductile fracture.
In addition, it can be seen from the fracture morphology that a small number of graphite balls are distributed on the fracture surface of nodular cast iron prepared under the condition of amplitude of 0.75mm and 2mm, and the morphology of graphite balls is poor and the distribution is uneven, which will weaken the strength of the matrix to a great extent and reduce the tensile strength of nodular cast iron. However, a large number of graphite balls are distributed on the fracture surface of the nodular cast iron prepared under the condition of amplitude, and the spacing between the graphite balls and the tearing edge is large, which has a great effect on the resistance to the yield deformation of the metal under tension. Therefore, it can be seen that the ductile cast iron prepared by this process has a high plasticity. There are a large number of graphite balls on the fracture surface of nodular cast iron prepared under the condition of amplitude of 4mm, and the morphology of graphite balls is good. The number of initial pits on the fracture surface is large and evenly distributed. Therefore, the ductile iron prepared under this process condition has the best shaping and the highest elongation.