The application of sand casting coating can close the pores between sand particles on the surface of mold and core, block the channel of liquid metal penetration, and reduce the mechanical sand adhesion of sand castings. Sand casting coating can slow down the radiation heating of mold or core, so as to reduce or eliminate the occurrence of sand inclusion defects. By adding thermal insulation and chilling materials to the coating, it can improve the temperature distribution in the mold cavity and control the solidification and crystallization process of the alloy, so as to reduce the occurrence of cold and hot cracks on the surface of sand castings.
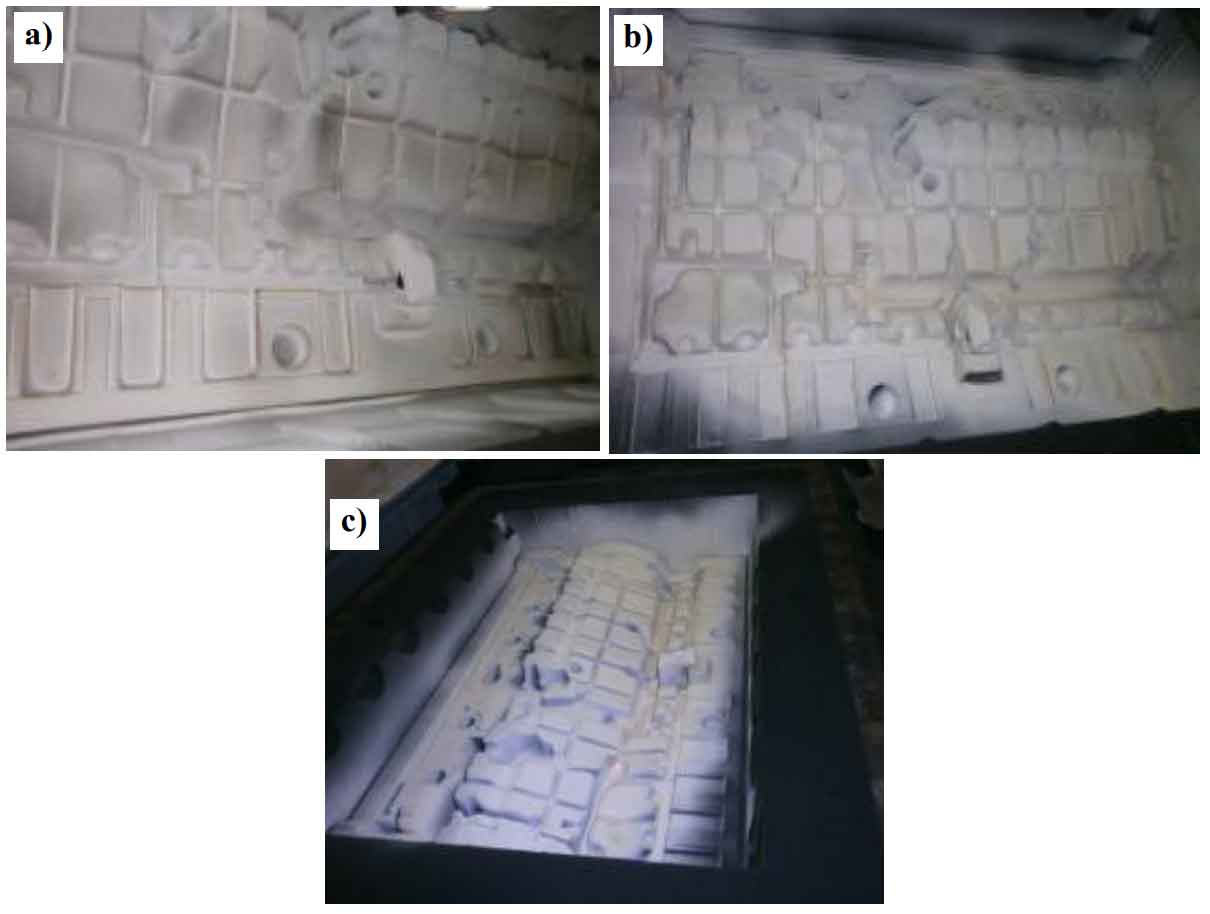
b) Sand mold with serial number 53 after spraying and ignition (spraying for 6 seconds)
c) Sand mold with serial number 55 after spraying and ignition (spraying for 8 seconds)
The paint spraying process scheme is used to test the 36d cylinder block of the static pressure line. A total of 5 boxes of paint with model ks55 are sprayed with serial number 51-55, of which serial number 51 and 52 are sprayed for 4-5 seconds, serial number 53 is sprayed for 5-6 seconds, serial number 54 and 55 are sprayed for 7-8 seconds: a total of 5 boxes of paint with model 3139 are sprayed with serial number 56-60 and spraying time is 7-8 seconds: ignition is started after spraying. The surface of the mold after spraying is shown in Figure 1.
When the coating spraying process scheme was used to test the HA coating spraying 36d cylinder block sand mold, the coating spraying and ignition sand mold of model ks55 were normal, while the sand mold of model 3139 FD powder alcohol based coating was cracked and foamed after ignition, as shown in Figure 2.
For the mold sprayed and ignited with HA coating, although there are qualified molds with coating surface quality during coating spraying and placement, there are still serious surface sand sticking defects in the cast sand castings, which are difficult to be removed through the subsequent cleaning process, and some sand castings even have peeling in some parts. Figure 3 shows that the sand still exists at the corner under the camshaft of the cylinder block. The experimental results show that the sand sticking defect on the cylinder surface can not be avoided by using the coating spraying process. There are not only surface sand sticking defects, but also local surface sand sticking defects are more serious. Therefore, the coating spraying process scheme is not suitable for cylinder sand castings.
According to the surface quality of sand castings after the coating spraying process scheme test, the coating spraying process scheme is used to test the 81D cylinder block, and three boxes of alcohol based ink coating with model ks55 are sprayed, with serial numbers of 30, 31 and 32 for 5-7 seconds; No ignition after spraying, as shown in Figure 4, the surface quality comparison of the same sand mold just after spraying and two minutes after spraying is shown. The surface quality of the mold is good.
According to the conclusion of scheme (I), the scheme is carried out in 81D cylinder block sand mold (2) Although no abnormality was found during the spraying process, the surface quality of sand mold casting was not significantly improved compared with the current production state, as shown in Figure 5. It can be seen from the figure that although the surface quality of HA coating was slightly improved, the sand sticking on the cylinder bottom was not completely solved, and the sand sticking at the corner still existed. This also shows that the surface of sand mold after coating spraying is good The surface can not be used as the final coating performance evaluation. The thermal effect of pouring liquid metal on the coating layer will affect the final performance of the coating.
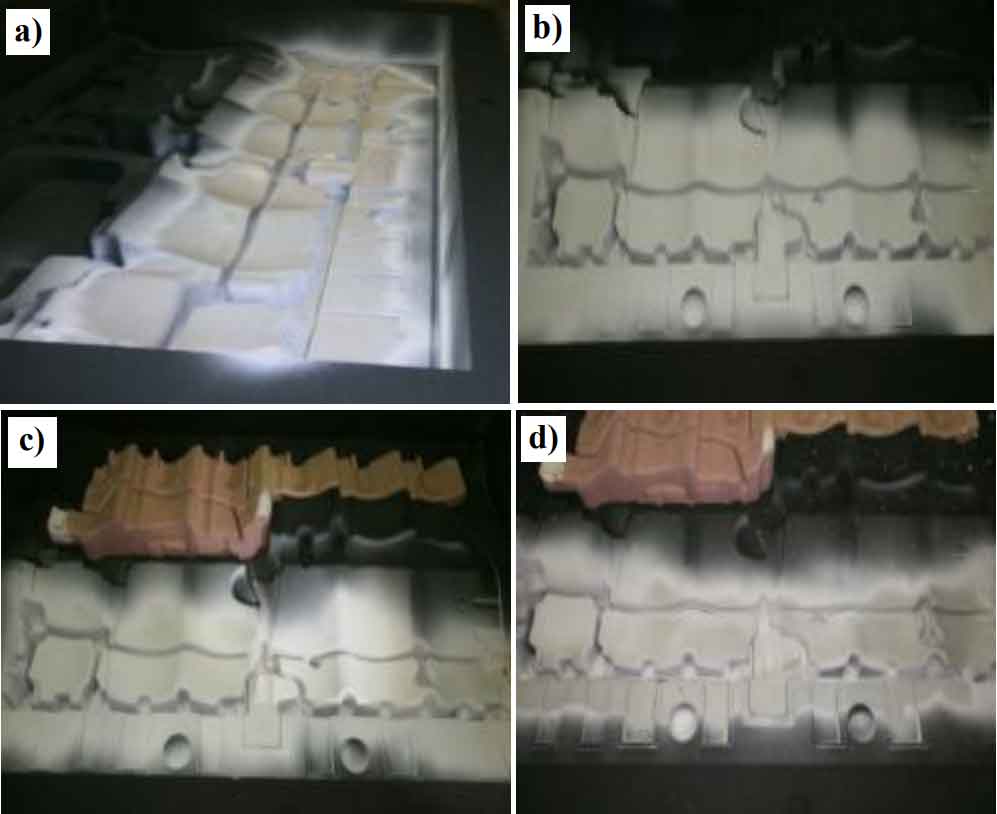
c) Low specific gravity key fire sand mold d) Low specific gravity non ignition sand mold
According to scheme (3), the 81D cylinder block of the static pressure line is tested in the modeling workshop using scheme (2). The results are shown in Figure 6.
Alcohol based FD powder coating with Chinese invention patent developed by ZHY casting, Application scheme of sand mold in 81D cylinder block (3) During the test, the sand mold ignited after spraying also has a layer phenomenon, as shown in Fig. 7. Compared with the current production state, the surface quality of the sand mold casting without ignition has the same improvement effect as that of the cylinder block after HA coating spraying. As shown in Fig. 8 and Fig. 9, whether it is high specific gravity ignition and non ignition sand mold or low specific gravity ignition and non ignition sand mold When the sand mold is ignited, the sand sticking still exists at the nest corner of the last cast sand mold casting.
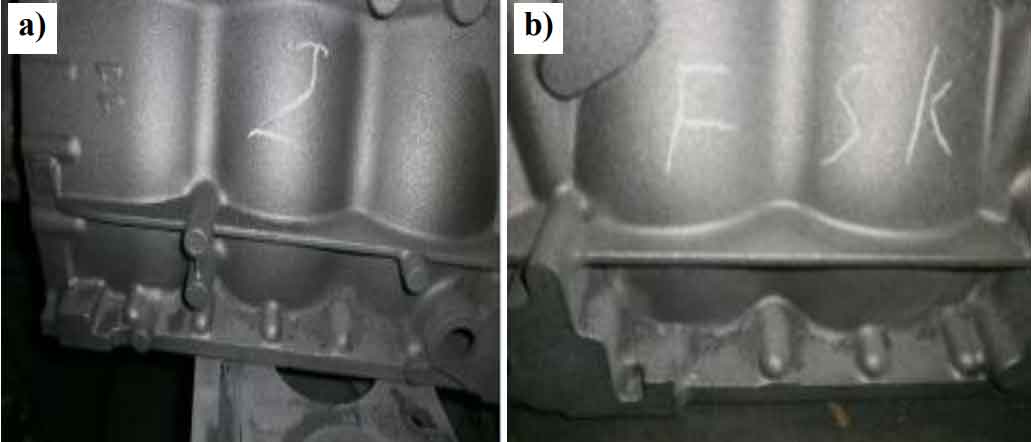
In the wet sand molding production line, the traditional process of mold spraying is alcohol based coating spraying, alcohol ignition and drying. Alcohol based coating is easy to dry as long as it is ignited, but the temperature during combustion can not be controlled, resulting in cracks in the mold. Alcohol based coatings have the characteristics of fast drying (ignition drying or natural volatilization drying), high production efficiency and wide application range. There are few studies on alcohol based coatings for Clay Green Sand in China, and the suspension, crack resistance, gas evolution and permeability of the coatings are relatively low. Due to the fine grain size of wet sand, poor air permeability and large gas generation, alcohol based coatings are required to have high permeability, crack resistance and small gas generation.
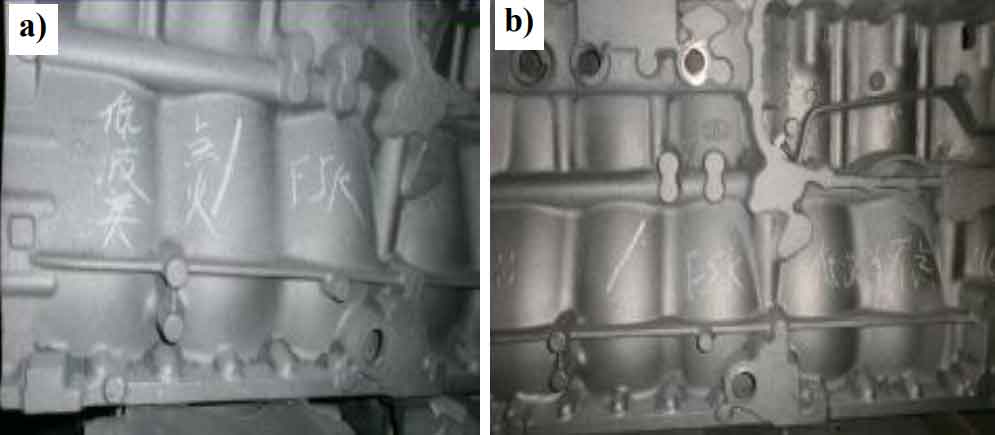
b) Castings formed by high specific gravity non ignition sand mold
The following conclusions can be drawn from the above coating spraying processes:
(1) When HA spray coating is used, the sand mold after ignition blisters and cracks. Although the sand mold castings at the blister and crack positions are not scrapped, there are potential quality hazards;
(2) When HA spray coating is used, peeling occurs in some parts of the cylinder block, which will not be scrapped after dissection, but it also has potential quality hazards;
(3) With HA spray coating, although there are slight signs of sand sticking at the corners of the non ignited cylinder block, the sand sticking at the corners of the cylinder bottom surface has not been completely solved;
(4) The coating developed by ZHY casting uses the coating with high and low specific gravity. After ignition, the sand mold has delamination, but there is no abnormality on the surface of the sand mold casting, and there are no problems such as peeling or sand washing;
(5) ZHY casting R & D coating ignited and non ignited cylinder blocks, with little difference in surface quality;
(6) The effect of HA spray coating is not very obvious. Although it is slightly better than the current production state, the problem of sand sticking at the ground corner of the cylinder block has not been completely solved.