When the rotating speed and feed rate are constant, the cutting length of the cutting edge for cutting each sample remains unchanged at 1000 mm. The cutting resistance of different cutting depths is shown in Figures 1, 2 and 3. It can be seen from the figure that under the three cutting depths, the cutting force of sample 3 in the X, y and Z directions is the largest, while the cutting force of sample 2 in the three directions is the smallest. Among them, the main cutting force at the three cutting depths of 1 mm, 1.25 mm and 1.5 mm is 3.2%, 6.2% and 2.2% lower than that of sample 3 respectively. The cutting forces in the three directions of sample 1 are between the two. At the three cutting depths, the main cutting forces are reduced by 2.1%, 5.8% and 1.4% respectively compared with sample 3. The greater the cutting force when cutting the sample, the worse the machinability of the material. It can be concluded that under the condition of alloying gray cast iron with multi-element alloy additives, the machinability of Gray Cast Iron Inoculated with SRSI inoculant is the best, the machinability of Gray Cast Iron Inoculated with 75sife is better, and the machinability of Gray Cast Iron Inoculated with basi inoculant is the worst.
Figure 4 shows the graphite morphology of three groups of gray cast iron samples. It can be seen from Figure 4 that the graphite morphology of inoculation treatment with different inoculants is different. The graphite morphology of sample 1 and sample 2 is fine curved flake A-type graphite, sample 3 is B-type graphite and a small amount of A-type graphite, and the graphite is relatively flat, with relatively large length and width (Fig. 4C)). Although the graphite of samples 1 and 2 are relatively fine curved, the graphite distribution of sample 1 is not very uniform (FIG. 4A)), only sample 2 (Fig. 4-9b)) The graphite is fine, curved and evenly distributed. It can also be seen from the figure that sample 3 has the most graphite content, sample 2 takes the second place, and sample 1 has the least graphite content.
A-type graphite has strong nucleation ability, low undercooling and small bending disorder. Flake A-type graphite can not only break chips, but also lubricate and reduce obstacles to tools, making materials easier to cut, so as to improve the cutting performance of workpieces. Sample 1 and sample 2 are also type a graphite, but the graphite of sample 2 is finely bent and evenly distributed. As the graphite distribution of sample 1 is uneven and the graphite content is less than that of sample 2, this is also one reason why its machinability is worse than that of sample 2. Sample 3 shows type B graphite, which is essentially type D graphite in the center, Type a graphite is in the periphery, and the cutting performance of type B graphite is worse than that of type a graphite. Although the graphite content of sample 3 is very high, the cutting performance of sample 3 is worse than that of sample 1 and sample 2 because its graphite morphology is not conducive to cutting (Fig. 1, 2 and 3), which also shows that the machining performance is largely restricted by the graphite morphology, It does not mean that the more graphite content, the better processing performance will be.
In general, with the increase of graphite content, the tensile strength of gray cast iron will decrease, which will help to improve the service life of the tool during cutting. Under the condition that the matrix structure is basically the same, the shape and size of graphite are the main factors affecting the strength of gray cast iron. Moreover, the improvement of graphite morphology and quantity is the main reason for the improvement of machinability of gray cast iron. Multi alloy additive alloying treatment uses a variety of alloys together, which can effectively improve the graphite morphology and quantity of gray cast iron, so as to improve the strength and machinability of gray cast iron to a certain extent.
Figure 5 shows the pearlite structure of three groups of gray cast iron. As can be seen from Fig. 5 (a) – F), the matrix structure of gray cast iron treated by multi-element addition alloying is pearlite. However, the differences of pearlite sheet spacing, lamellar structure and carbide arrangement among the three groups of samples can not be seen. Similarly, the machinability of gray cast iron can not be quantified. However, because the microhardness deviation of sample 3 is the largest, it can be concluded that its microstructure is the most uneven and its machinability is the worst, while the microhardness deviation of sample 2 is slightly larger than that of sample 1, but its machinability is better than that of sample 1, which shows that although the machinability of gray iron castings is affected by the uniformity of matrix structure to a certain extent, However, it is also restricted by the morphology and quantity of graphite.
Through the above analysis, it can be concluded that the effective way to improve the machinability of gray cast iron is to improve the deformation ability of iron filings, which requires to improve the microstructure uniformity. Therefore, it is necessary to improve the metallurgical quality of molten iron, the control measures conducive to its own nucleation, the selection of appropriate inoculants and inoculation methods, the selection of alloy elements with small side effects and the addition of alloy elements as little as possible, so as to meet the strength requirements and improve the organization uniformity and processing performance.
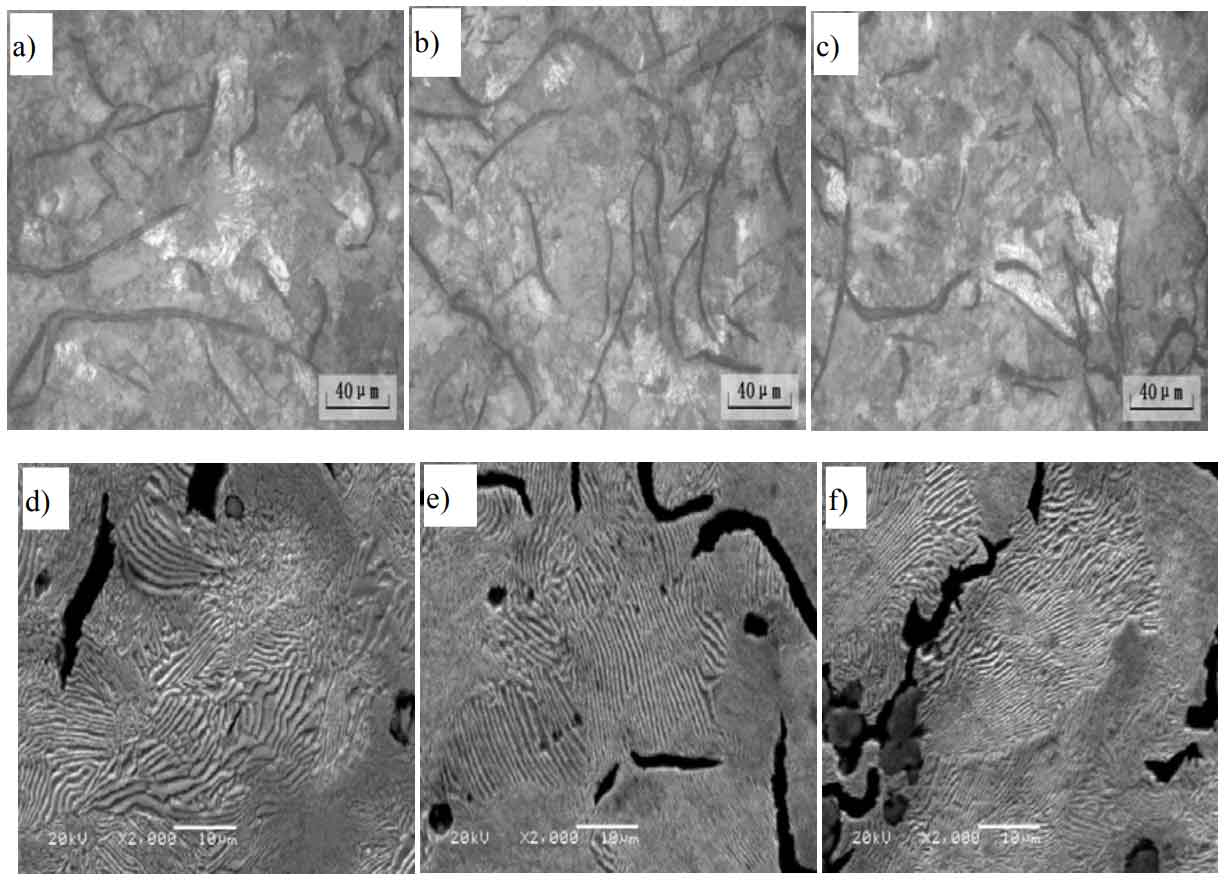
Different inoculants have their own advantages in improving the strength of gray cast iron, improving the graphite morphology and matrix hardness, controlling the white tendency, improving the uniformity of matrix structure and reducing the sensitivity of casting section. Moreover, they can promote graphitization, inhibit eutectoid cementite and even prevent matrix ferrite. 75sife is the most commonly used inoculant, and the aluminum and calcium in 75 ferrosilicon play an important role in the inoculation effect. Some data believe that the inoculant of ferrosilicon does not contain aluminum and calcium, so the inoculant has little inoculation effect on gray cast iron. Aluminum and calcium in molten iron react with oxygen and nitrogen to form high melting point compounds and form graphite crystalline core. Adding inoculant into molten iron can form local silicon rich micro region which is convenient for graphite precipitation. However, too high aluminum content in molten iron can lead to subcutaneous pores in castings.
SisR inoculant containing SR can enhance the graphitization ability, which is characterized by promoting graphitization without significantly increasing the number of eutectic clusters. Eutectic clusters are the main part of porosity. Reducing the number of eutectic clusters is beneficial to reducing intergranular porosity defects. There are few carbides and graphite refinement tendency in the matrix structure of cast iron containing SR inoculant, which may be one of the main reasons for the improvement of machinability of gray cast iron treated with SR inoculant. Strontium silicon
Strontium in the inoculant has strong affinity for oxygen. It combines with the oxidation in molten iron to form SrO, which deoxidizes the molten iron, that is, inoculation. When a small amount of strontium oxide with considerable energy is formed in molten iron, the existing crystal nuclei in the melt may also be activated. Strontium silicon inoculant has a strong ability to eliminate white mouth, especially in improving the quality of thin-walled castings
The morphology and distribution of graphite are favorable to reduce the difference of microstructure at different thickness. The domestic supply of ferrosilicon containing strontium has two strontium contents of 0.6% – 1.0% and 1.0% – 2.0%. Ferrosilicon containing strontium is a highly effective inoculant, and its addition is only half of ferrosilicon 75. In addition, the anti fading ability of molten iron treated with strontium silicon inoculant is stronger than that of ferrosilicon and calcium silicon inoculants. Under the same test conditions, the anti decay ability of Si SR inoculant is stronger than that of Si Fe and Si Ca, and it is a long-term inoculant. Literature [49] reports that the cylinder blocks of gasoline and diesel engines are produced by using high carbon equivalent gray cast iron and inoculated with silicon calcium inoculant, the mechanical properties often fail to meet the requirements, and the produced cylinder blocks often have defects such as leakage and slag inclusion in the machining process. After analysis, the main reason for these defects is the coarse tissue and shrinkage porosity at the hot spot; In addition, due to the large slag forming tendency of silicon calcium inoculant and the large amount of addition required for treatment, it is easy to produce slag inclusion in castings due to the large amount of slag. Good results have been obtained after using strontium silicon inoculant.
The graphite of Gray Cast Iron Inoculated with Siba inoculant containing Ba is evenly distributed and slender, all of which are type a graphite. The three inoculants can improve the graphite morphology and make the graphite precipitate evenly. In the production of thin-wall castings, it can effectively prevent the formation of white cast iron at the thin-wall, reduce the free cementite in the matrix structure and uniform the layer spacing of pearlite structure, Improving the machinability while ensuring the mechanical properties of castings can improve the wall thickness sensitivity of castings and significantly improve the anti recession ability of castings. As we all know, barium salt is an activated substance (barium itself is a surface active element). Its decomposed barium has strong affinity for oxygen and has good deoxidation and degassing effect on molten iron. Barium silicon inoculant has a strong ability to promote graphitization, which is helpful to improve the morphology and distribution of graphite in thin-walled castings, refine eutectic clusters and improve mechanical properties. Another outstanding advantage is its strong ability to resist inoculation decay, and the amount of treatment is less than 75 ferrosilicon. It is reported that adding too much barium will increase the ferrite content in the body, increase the strength of cast iron and reduce the strength of cast iron. At present, the content of barium in barium ferrosilicon in China is generally 4% – 6%.