The figure shows the maximum porosity of a hydraulic valve body with cast material of QT500-7 as a function of pouring temperature. It can be seen from the figure that the maximum porosity is the smallest when pouring temperature is 1360 C, with a value of 0.634. When temperature is higher than 1360 C, the maximum porosity increases rapidly and then basically remains around 0.95.
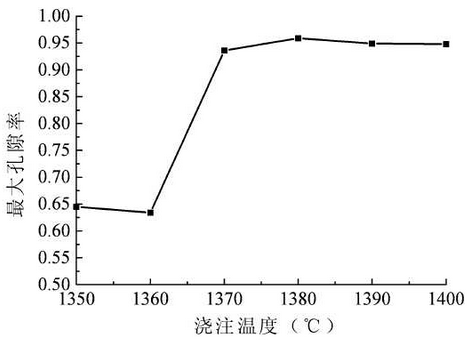
It can be seen from this that the higher the pouring temperature, the higher the maximum porosity of the castings. The optimum pouring temperature is 1360 C.This is because the liquid shrinkage of the metal liquid increases with the increase of pouring temperature. When the liquid shrinkage of the metal liquid increases, the graphite expansion is more insufficient to compensate for the liquid shrinkage in the subsequent solidification process, which ultimately leads to the increase of casting porosity. On the other hand, when the pouring temperature increases, the heat from the metal liquid increases the solidification time of the whole casting.As a result, at the initial stage of solidification, the liquid metal shrinkage in the pouring system increases, which partially offsets the increase in liquid shrinkage due to the increase in pouring temperature. Therefore, the maximum porosity of the casting remains basically unchanged when the pouring temperature is higher than 1370 C.