Data transfer in the process of fluid-solid coupling (FSI) calculation is to transfer the simulation results of flow field (pressure, temperature) to the solid part through the interface and calculate the stress and strain of solid structure under pressure and temperature.
1 Grid Division
Patch Independent method is used to divide the tetrahedron mesh while limiting the minimum size (MinSize Limit) to 0.3mm and the maximum size (Max Element Size) to 6mm. Advanced Sized Function (Proximity and Curvature) is also turned on.The grid number is about 1.1 million and the maximum Skewness is about 0.94. The grid model is shown in Figure 1.
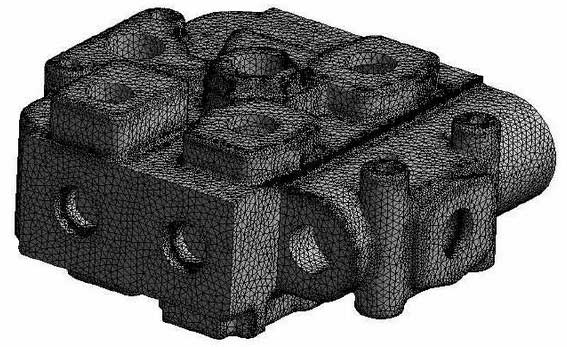
2 Constraints and Material Properties
The multi-way valve is fixed to the mounting plate by four screws while it is in operation, so Fixed Support is used in the calculation to restrict all degrees of freedom on the end face of the screw hole as shown in Figure 2.
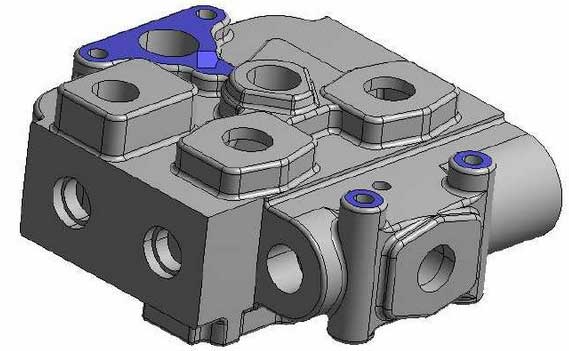
The valve body material is ductile iron QT500-7 with density of 7270 kg/m3, Poisson ratio of 0.27, Young’s modulus of 1.835_105 MPa, thermal conductivity of 32.2 W/m/K and yield limit of 320 MPa.
3 Applying Loads
1) Temperature load
The results of flow field simulation are introduced into Workbench and temperature load is applied to the valve body surface through the coupling surface. The results are shown in Figure 3. It can be seen from the diagram that the results correspond to the simulation results of flow field. The corresponding parts of the valve body and the spool orifice have a higher temperature, the highest temperature reaches 43 C, and there is no high temperature in other areas. After the orifice, the temperature of the valve body corresponds to that of the spool orifice.In the region where the temperature decreases gradually.
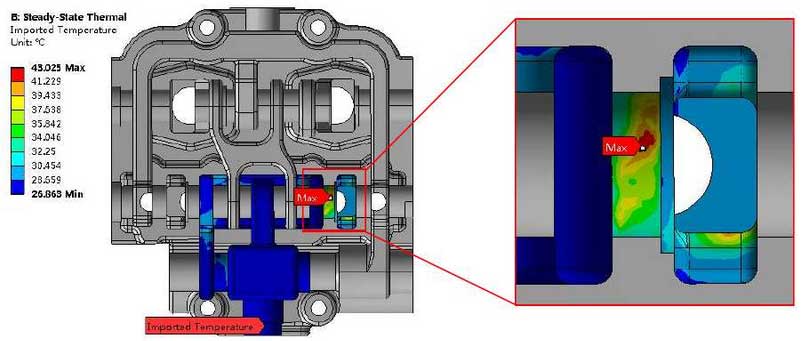
2) Pressure load
Similarly, the pressure load generated by the flow field simulation is applied to the valve body surface through the coupling surface. The result is shown in Figure 4, which is in agreement with the simulation result of the flow field. When the oil flows through the throttle port, the pressure loss is caused by the throttling effect of the valve port, resulting in a decrease of the oil pressure behind the throttle port.
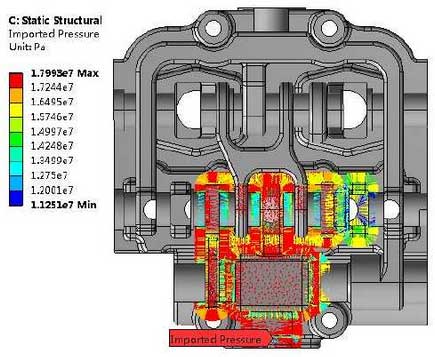
4 Stress distribution
The pressure and temperature loads are applied to the valve body surface through the coupling surface. The stress distribution cloud diagram of the ideal multi-way valve body is shown in Figure 4.11. It can be seen from the diagram that the maximum stress is concentrated at the inlet of the middle oil passage in the bucket linkage of the valve body, with a value of 220.88MPalt; 320MPa, which meets the strength requirements.The main reason for stress concentration is that the structure of this part of the valve body changes greatly and the transition roundness is small, which is easy to cause stress concentration.
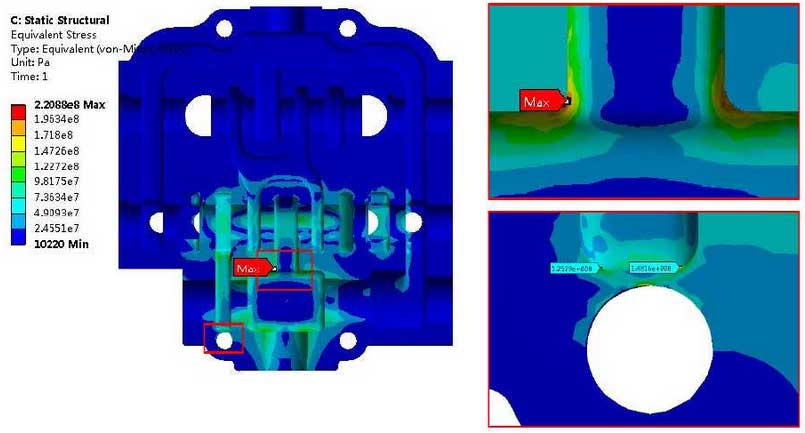
In addition, when high-speed and high-pressure oil flows through this part, the flow area suddenly becomes smaller, which leads to the increase of the flow rate of oil and the serious scouring of this area.Stress is also concentrated in the oil duct behind the one-way valve because the wall thickness between the oil duct and the bolt hole is small and the carrying capacity is weak.