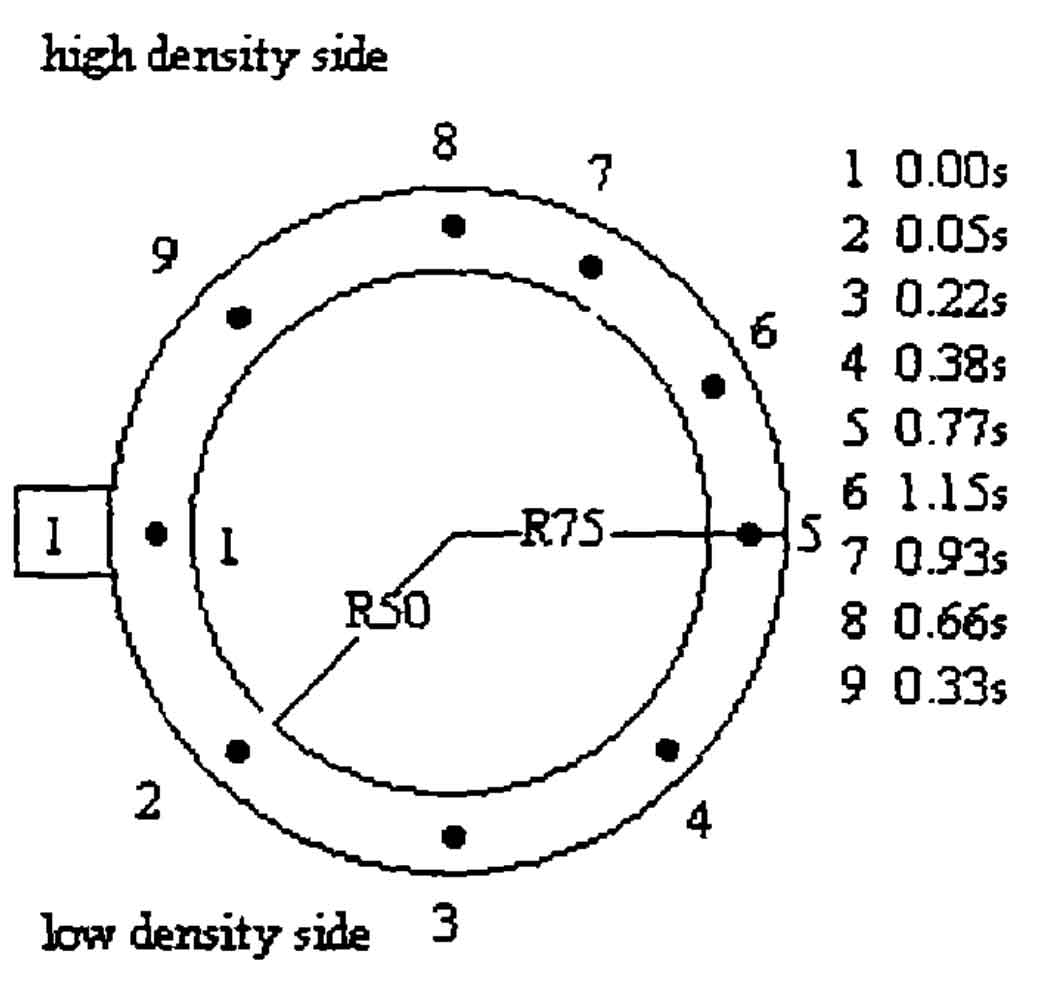
The outer circle diameter is 150mm, the inner circle diameter is 100mm, and the ring thickness is 20mm. The model is placed horizontally in the sand box, and the measuring points are evenly arranged on the center line of the model. The density of the model shown in Fig. 2 is 13.2g/I, and the model shown in Fig. 1 is made of two models with different densities bonded by hot melt adhesive. The density of the model is 13.2g/I and 9g/I respectively, and the inner runner is introduced from the bonding part of the model.
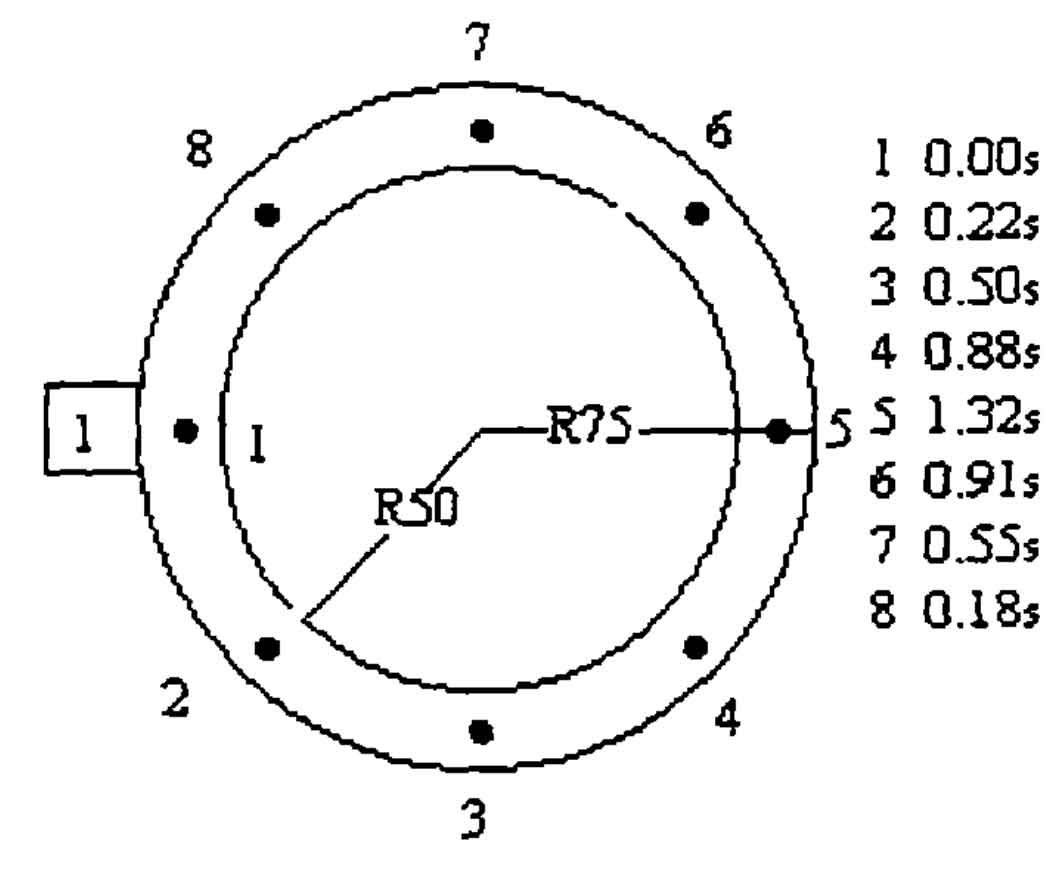
Fig. 3 is the relationship curve between the filling distance of molten metal and the filling time of molten metal in a single density model. The last filling position of molten metal is located at the symmetrical position with the center of the ingate. The filling time of molten metal in lost foam casting is 1.32s and the average filling speed is 14.9cm/s.
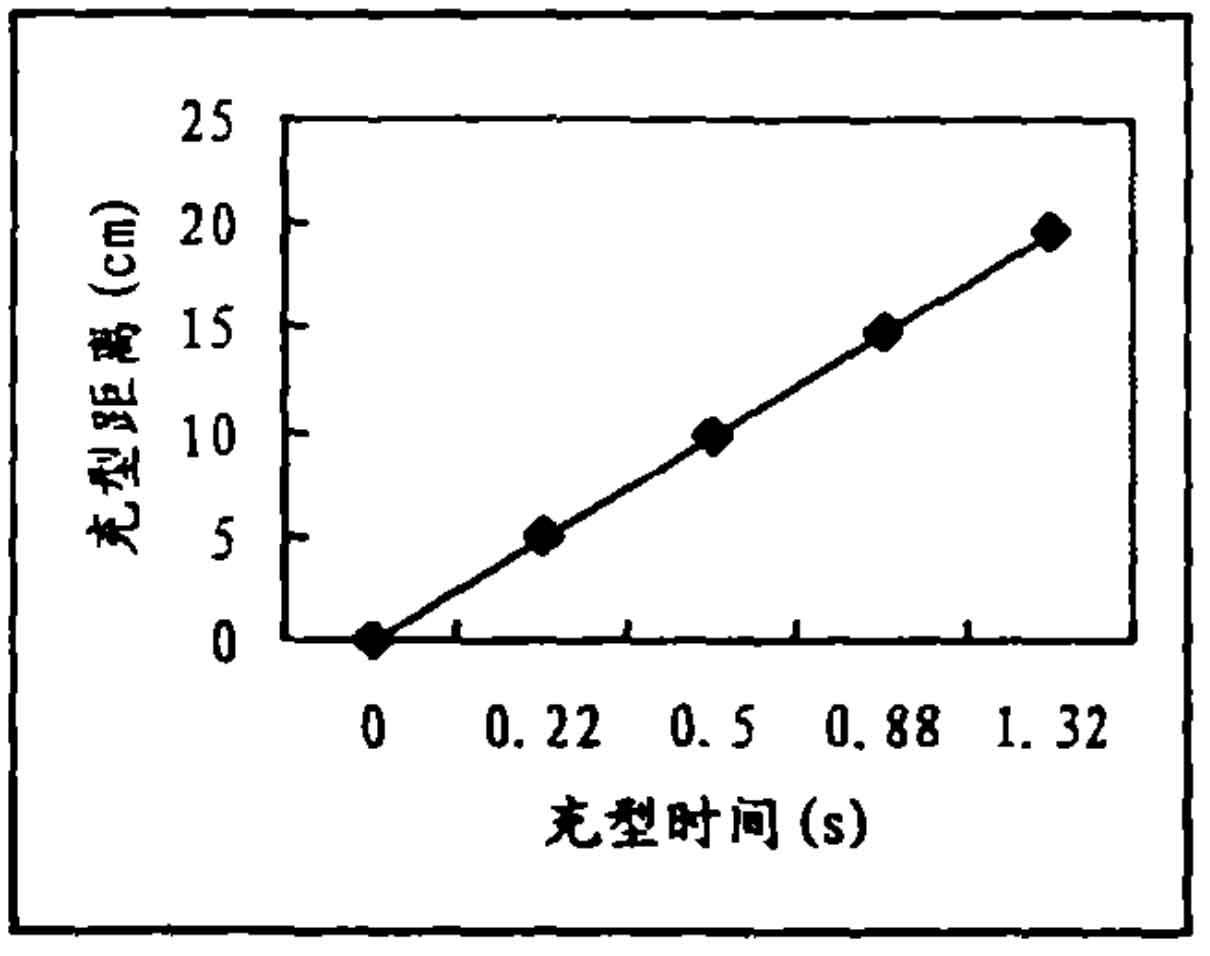
Figure 4 shows the flow curve of liquid metal in the combined model. The last filling position of liquid metal is at measuring point 6. The filling time of lost foam casting is 1.15s. At the end of filling, the flow distance of liquid metal along the side of high-density model is 17.92cm/s, and the flow distance of liquid metal along the side of low-density model is 22.9cm/s. The filling speed of liquid metal in lost foam casting is 15.58cm/s and 19.91cm/s respectively, which is 1.28 times that of the former.
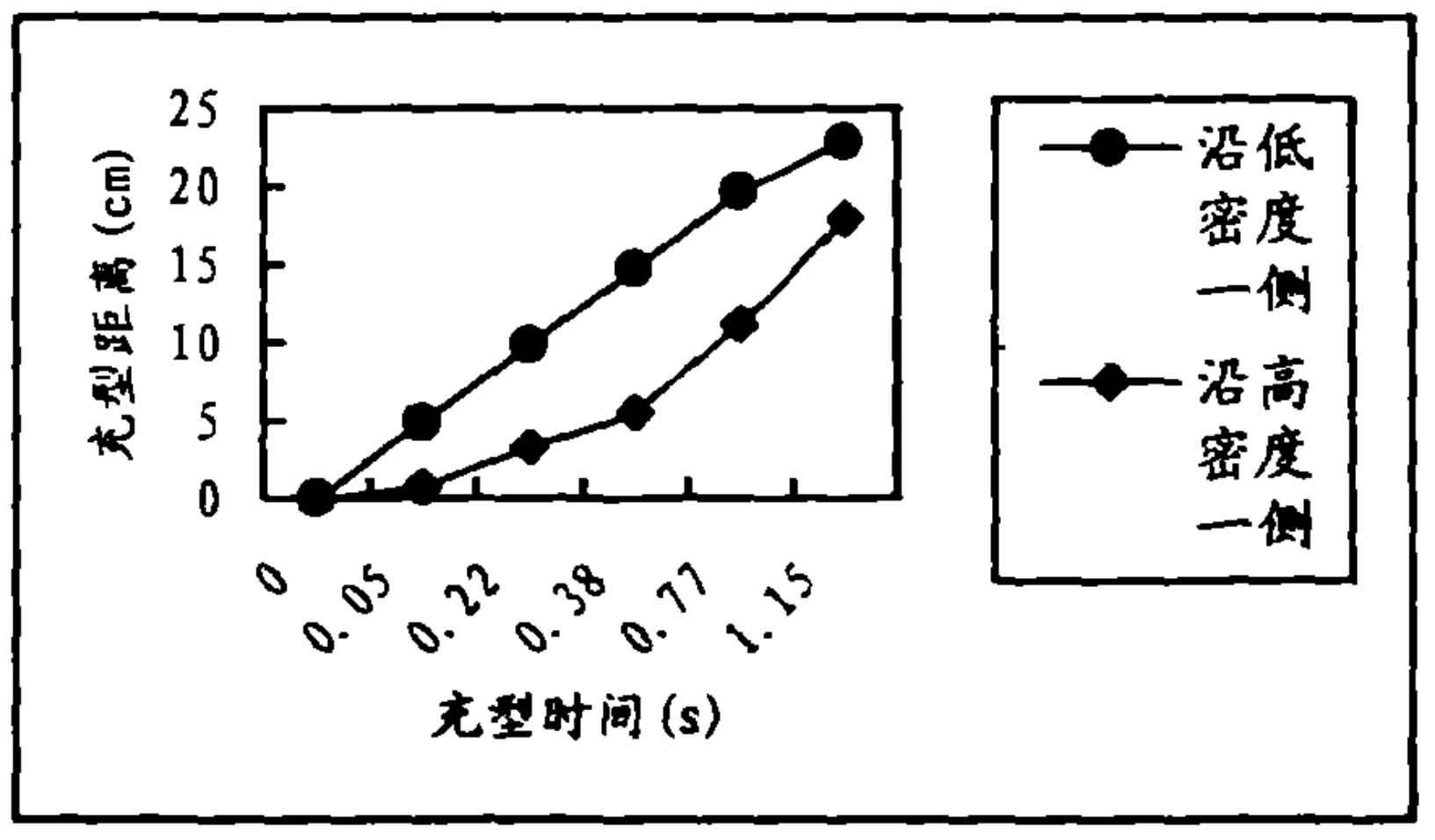
The filling time of molten metal in lost foam casting is longer than that in cavity casting. The existence of pattern is the main reason for this difference. The gasification and decomposition process of pattern needs to absorb heat from the liquid metal, and the decomposition products of pattern, especially the gas decomposition products, need to be diffused from the mold through coating
Into the surrounding molding sand. The pattern material determines the type, quantity and decomposition speed of decomposition products. Low density patterns consume less heat in the decomposition process, and the number of gas decomposition products is small. Therefore, under the same other conditions, the liquid metal filling speed of low density patterns is fast.
Under the same pouring temperature, negative pressure, hydrostatic head of molten metal, coating and model material, the average filling speed of molten metal of flat model, square model and circular model is 22.9cm/s, 14.7cm/s and 14.9cm/s respectively, and the ratio of filling section perimeter to cross-sectional area of lost foam casting is 0.12, 0.18 and 0.14 respectively. The smaller the ratio of perimeter to cross-sectional area, The smaller the friction resistance loss in the process of liquid metal filling in lost foam casting, under the same test conditions, the metal filling speed of plate model is the fastest, the ring model is the second, and the box model is the slowest.
In actual production, the geometry of the model is diverse. When pouring and filling the mold in lost foam casting, the influence of the model shape should be fully considered. Complex or thin-walled castings need faster pouring speed and higher pouring temperature. For castings with the same volume, the smaller the modulus is, the larger the surface area is. With the increase of the surface area of the casting, the heat dissipation area and cooling rate of the molten metal increase during the pouring process. In the late filling stage, the temperature at the front of the molten metal flow decreases sharply, and the liquid metal does not have enough heat to make the front model fully gasified and decomposed. These non gasified decomposition products interact with the molten metal, which will lead to casting defects.