After putting the mold coated with lost foam casting paint into the sand box containing bottom sand, fill the sand box with rain and sand, and then place the sand box on the three-dimensional vibrating table to vibrate and compact the shape.
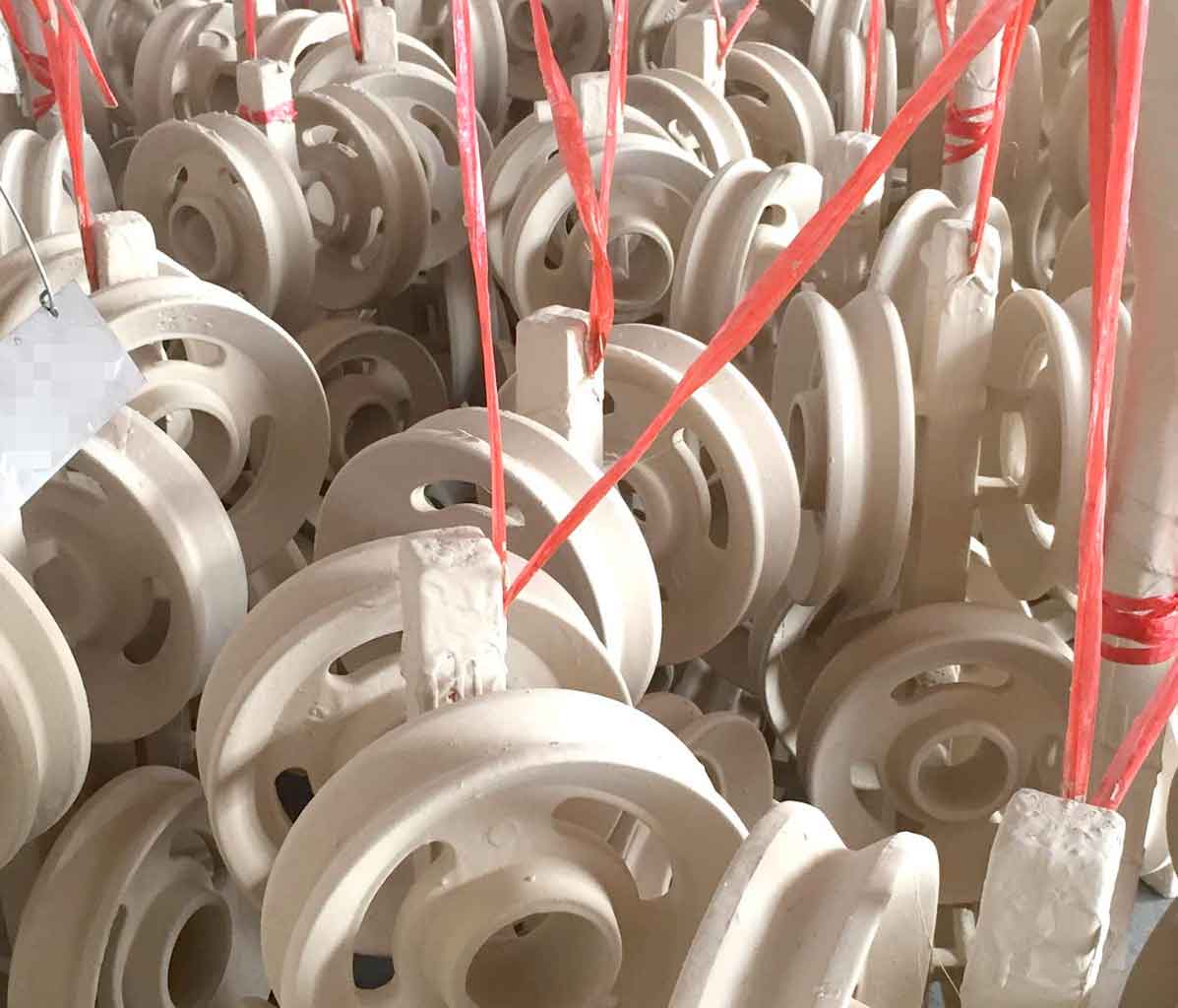
1.Molding sand
Lost foam casting uses dry sand. In order to obtain lost foam castings consistent with the pattern and prevent pattern deformation, it is required that the density of dry sand filling is high and the pressure in all directions is consistent. In addition, in order to fill the inner cavity of the pattern and its holes, especially the blind holes, well, the sand must have high fluidity. In the pouring process, the gas decomposition products produced by the decomposition of the foam pattern should be discharged into the mold cavity through the molding sand, which requires that the molding sand has high permeability. Based on the above two points, the molding sand for lost foam casting should have appropriate particle shape and particle size composition, and a round natural quartz sand is generally selected.
2.Vibration
As one of the key technologies of the dry sand lost foam casting process, the vibration filling and compaction of dry sand should not only make the sand quickly reach anywhere around the model to form sufficient compactness, but also make the deformation of the model smaller, so as to ensure the formation of a clear outline and accurate size lost foam casting after pouring.
The filling and compaction process of dry sand in the vibration state is an extremely complex unsteady process of granular body dynamics. In the vibration process, each sand particle is independent and interrelated. The basic principle of vibration modeling is to make the sand overcome the internal friction between sand particles, the external friction between sand model and sand box wall, and its own gravity in the vibration process, Fill the periphery and inner cavity of the model. When the pattern is placed in the sand box for vibration molding, it is inevitably deformed by the exciting force from the shaking table and the extrusion force and impact force when the sand in the sand box is filled with the model. If the deformation is too large, it will affect the accuracy of lost foam castings after pouring, and even lead to serious deviation in the size of lost foam castings, resulting in waste products. The vibration process not only makes the inner cavity and surrounding of the model full of molding sand, And ensure that the deformation of the pattern is not too large. The main vibration parameters involved in lost foam casting process include vibration direction, vibration time, vibration frequency, vibration acceleration and amplitude. The vibration direction can be obtained by horizontal and vertical excitation sources and their combinations, which can form one-dimensional vibration, two-dimensional vibration and three-dimensional vibration. Generally, two-dimensional vibration table is used, and three-dimensional vibration table is used for complex models. The effect is good. The vibration time of dry sand in the sand box is generally seconds, There is a danger of deformation if the vibration time is too long. The vibration frequency is generally vibration acceleration, and the amplitude of gravity acceleration is generally. It should also be adjusted according to different lost foam castings. Because vibration increases the filling density of molding sand and the strength of the mold, the selection of vibration conditions is one of the important aspects of quality management of French casting. In order to obtain uniform high filling density and ensure that the model is not deformed, it is necessary to determine the vibration conditions according to the lost foam castings.
3.Negative pressure
In lost foam casting, negative pressure has the following effects:
(1) Produce pressure gradient in the mold, bond the molding sand, and prevent sand flow and mold collapse;
(2) Absorb the gas produced by the thermal decomposition of the mold, reduce the pressure in the mold, and prevent the casting from producing internal defects such as pores;
(3) Absorb the gas produced by the thermal decomposition of the model to prevent the casting surface defects such as bright carbon formed by the gas decomposition products;
(4) Promote the liquid flow at the interface between the mold and the mold;
(5) The metal filling speed is accelerated, and the filling distance is lengthened;
(6) The harmful gas and smoke generated by EPS decomposition can be eliminated by the pressure reducing device, which greatly improves the working environment.
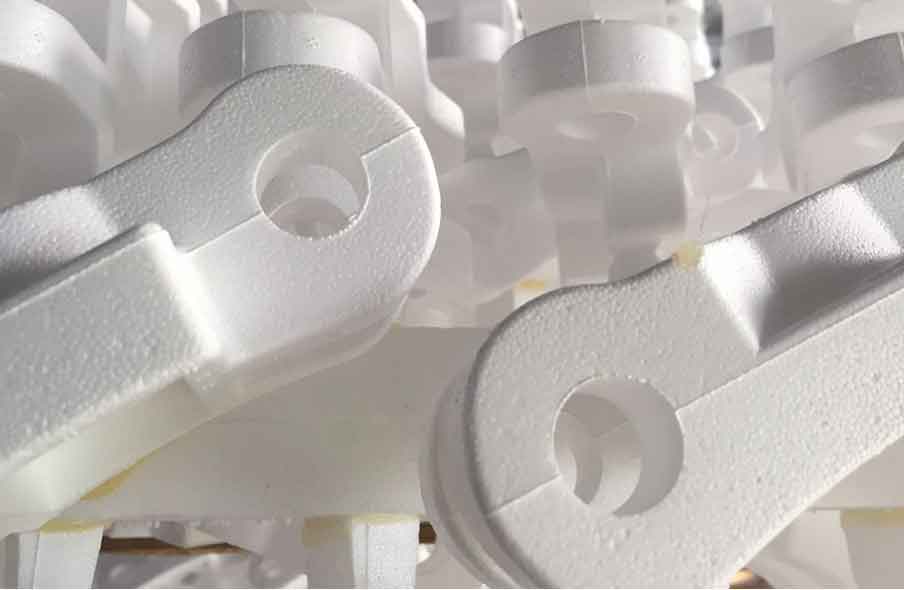
The main means to make sand filling and compaction are vibration and negative pressure pumping. Vibration is the primary condition to obtain a compacted mold. Negative pressure plays a very important role in compaction. It seriously affects the filling morphology, solidification and penetration of molten metal, and directly affects the hardness and yielding of the mold. The determination of negative pressure is mainly based on the type of alloy, fluidity, section thickness of lost foam casting, coating and sand of lost foam casting, etc. When pouring aluminum alloy, due to its good fluidity, the negative pressure should not be too large to prevent metal penetration defects in lost foam castings, which is generally about -100mmhg; When pouring cast iron, due to the high pouring temperature, the effect between the molten metal and the pattern is intense, and there are many gas decomposition products. If the pressure reduction is too low, the effect of pressure reduction is not obvious. Generally, a negative pressure of more than -400mmhg is used.