The external geometric dimension is 200mmx100mm, the internal geometric dimension is 150mmx50mm, and the thickness of the model is 20mm. Measuring points are arranged on the centerline of the model.
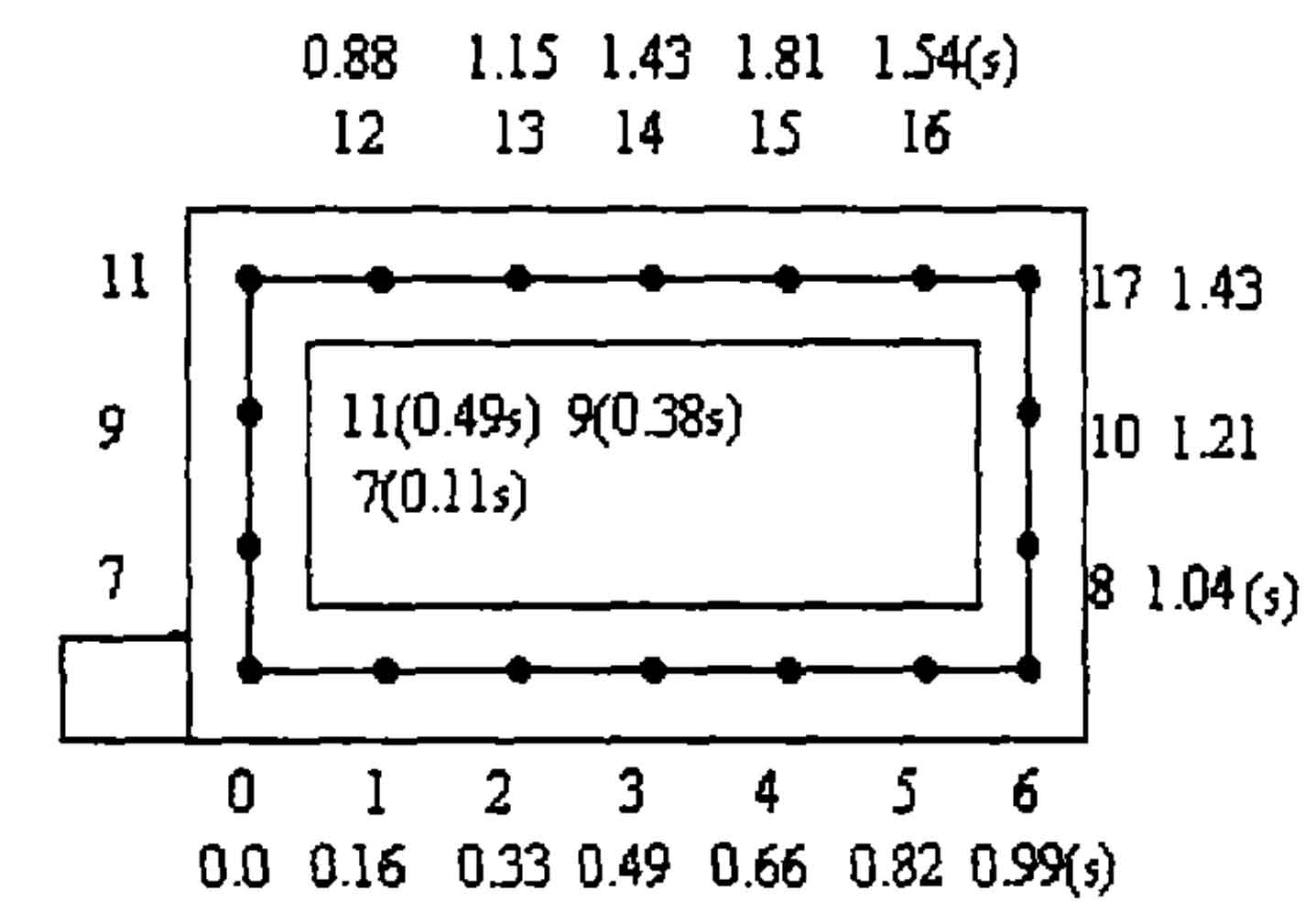
As shown in Figure 1, the ingate is introduced from the side of the width direction of the model, and the model is placed horizontally in the sand box. The size of the ingate is 20mmx20mmx30mm, the spacing of measuring points in the width direction of the model is 25mm, and the spacing of measuring points in the length direction of the model is 29.2mm. As shown in Figure 2, the ingate is introduced from the symmetrical centerline of the model. The model is placed horizontally in the sand box. The size of the ingate is 20mmx20mmx30mm. Measuring points are arranged on one side of the centerline of the model. The spacing of measuring points in the width direction of the model is, and the spacing of measuring points in the length direction of the model is 18.8mm. The test number is shown in Figure 1 and Figure 2.
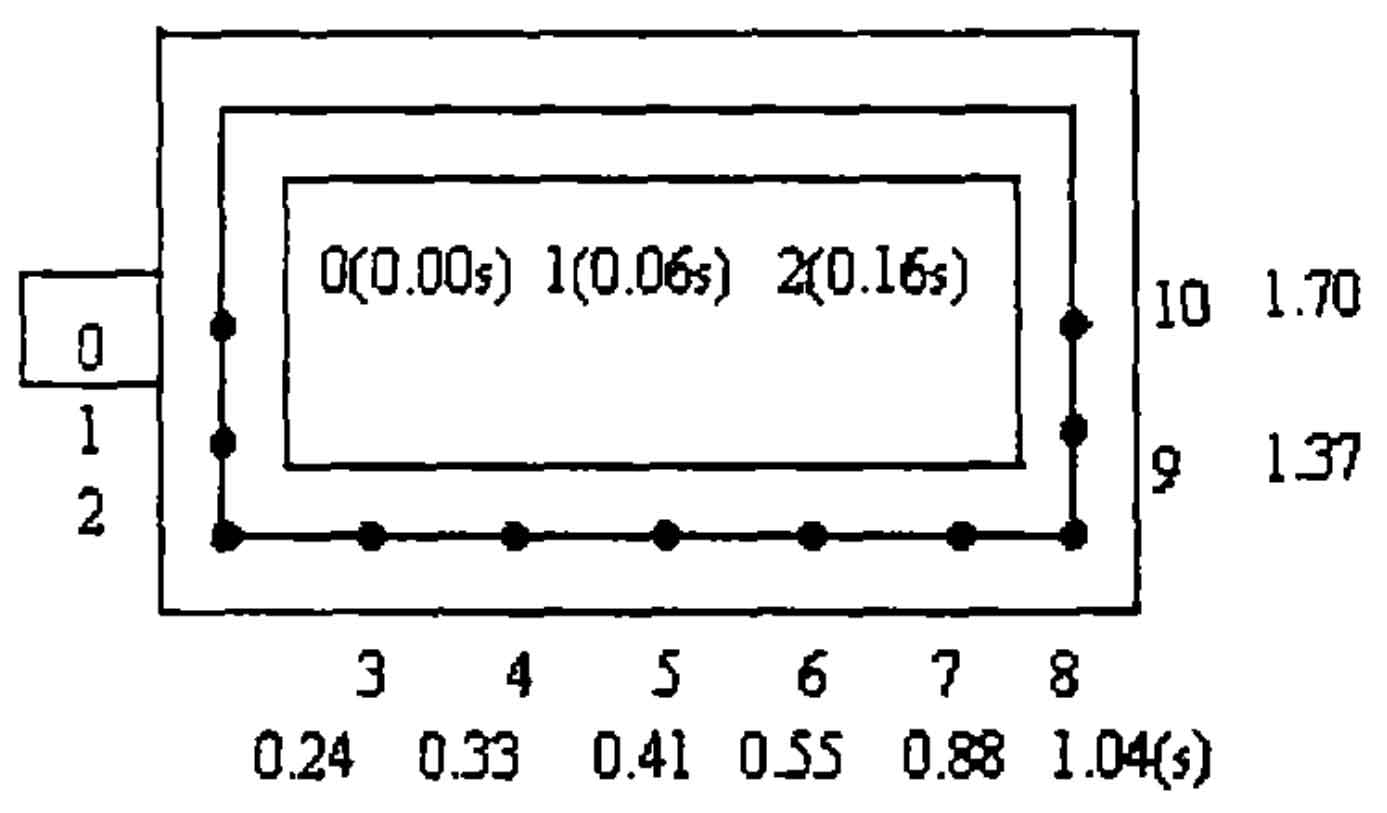
Figure 3 is the relationship curve between the filling distance and filling time of liquid metal in the model shown in Figure 1. After the liquid metal enters the inner gate, it will be divided into two streams, flowing along the length and width of the model. At a certain time, the two streams converge, and the liquid metal filling of lost foam casting ends. The test results show that the time required to complete the filling of the molten metal in lost foam casting is 1.81s, the last filling position of the molten metal is at the measuring point 15, the flowing distance of the molten metal in the longitudinal direction is 310mm, and the flowing distance of the molten metal in the width direction is 190mm. The filling speed of the molten metal in the two directions is 17.1cm/s and 10.5cm/s respectively, the former is 1.6 times of the latter, The average filling speed is 13.8m/s, and the inertial effect of molten metal filling is the reason for this difference.
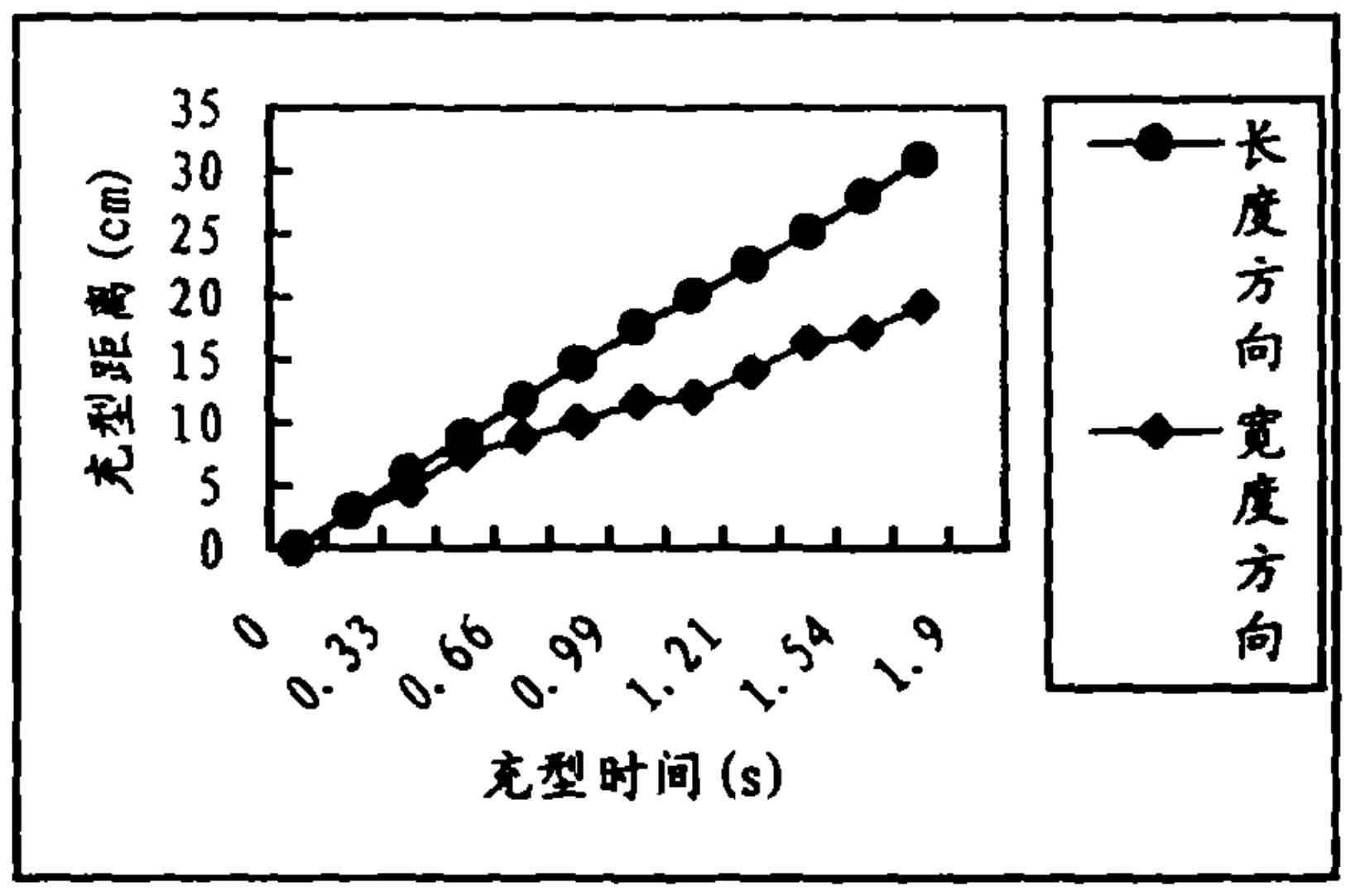
Figure 4 is the relationship curve between the filling distance of liquid metal and the filling time of liquid metal in the model shown in Figure 2. From the slope of the curve in the figure, it can be seen that the liquid metal has a faster filling speed in the initial stage of lost foam casting filling. With the lost foam casting filling process, the filling speed decreases until it reaches a relatively constant filling speed. The average filling speed of liquid metal in lost foam casting is 14.7cm/s.
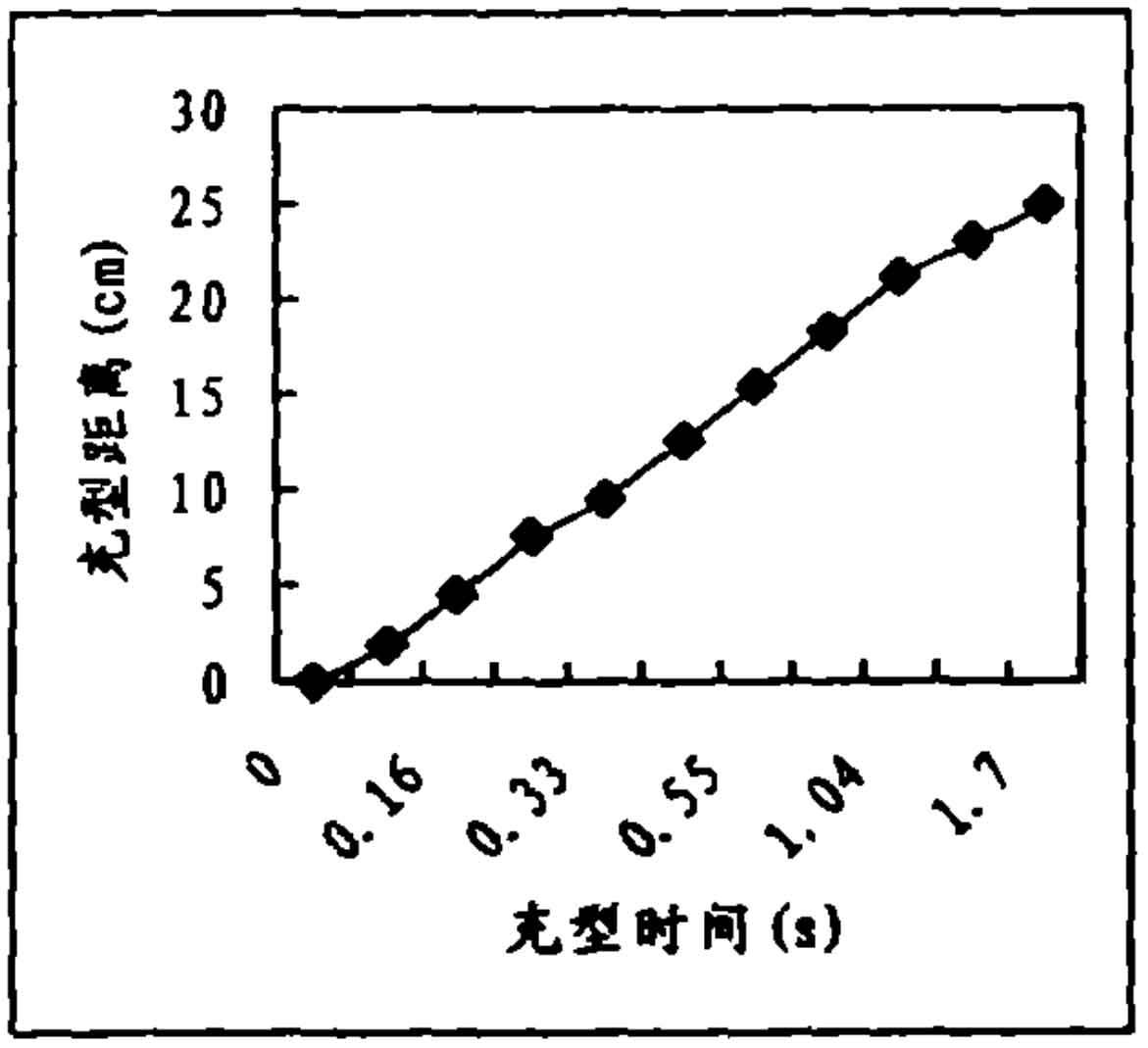
When the pouring temperature, negative pressure, static head of liquid metal, coating and model material are the same, the average filling speed of liquid metal in flat model and box model are 22.9cm/s and 14.7cm/s respectively. The geometry of the model has an important impact on the filling process. The ratio of the perimeter and cross-sectional area of the filling section of the flat model and the box model is 0.12 and 0.18, respectively. The ratio of perimeter / cross-sectional area decreases, which reduces the friction resistance loss in the filling process of liquid metal in lost foam casting and improves the fluidity of liquid metal.
In the process of metal liquid filling, the heat loss along the way is mainly due to the decomposition and gasification of foamed plastic and the heat exchange with the coating. The former is related to the volume of the foamed plastic decomposed by gasification and the latter is related to the coating area flowing at the front of the liquid flow. The larger the coating area flowing, the more heat is consumed, the worse the metal liquid filling ability and the slower the lost foam casting filling speed. The moduli of the plate model and the box model are 7.69 and 5.56 respectively, so the relative heat dissipation area of the metal liquid is large when the box model is filled, the filling capacity of the metal liquid in lost foam casting is weak, and the filling speed of lost foam casting is low.