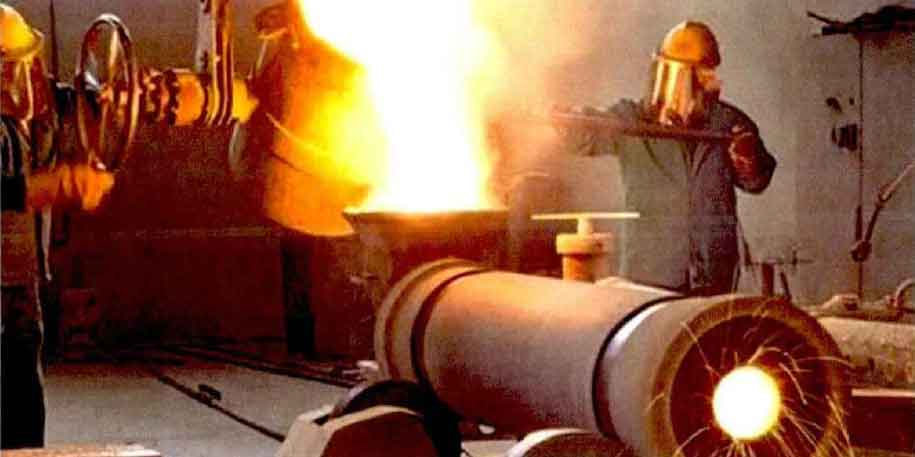
The working surface of the composite roll is the outer surface, that is, the outer layer should meet the requirements of high hardness and high wear resistance, and the inner layer should have good toughness. The combination effect of centrifugal casting determines the mechanical properties of the composite roll, and the crack is the most common failure form in the working process of the composite roll, which is difficult to avoid in the actual production. Cracks are mainly caused by too many inclusions in the molten metal, resulting in the formation of internal slip bands, which are easy to form dislocation accumulation at the interface between the inclusions and the matrix, resulting in the reduction of grain boundary adhesion, the formation of microcracks at the interface, and the cold shut of the casting caused by too low preheating temperature of the preform during compound pouring, which eventually leads to cracks. Howard et al. Proposed that the solid-liquid two-phase zone can be divided into quasi solid phase zone and quasi liquid phase zone during solidification of liquid metal, which provides a certain theoretical basis for the study of defects such as cracks. At the same time, combined with the variable speed cooling technology of the mold, using variable speed centrifugal casting to improve the distribution of temperature field and stress field of the roll can effectively improve the crack distribution and prolong the service life of the roll. High strength, high hardness, high wear resistance and long service life are the primary consideration standards for the practical use of composite rolls. In order to eliminate the coarse as cast structure of high-speed steel and the eutectic carbide at the grain boundary in the rolls, the centrifugal casting composite roll ring is studied. It is found that after RE Mg Ti Modification, the internal structure of high-speed steel is dense, the eutectic carbide is obviously refined, and the service life is significantly prolonged. In order to eliminate component segregation and prevent roll fracture, appropriate amount of alloy elements can be added for treatment. For composite rolls with high Ni Cr cast iron on the outer layer and ductile iron on the inner layer, elements V and Nb are added to the outer layer during pouring. After tempering, the graphite on the outer layer becomes fine and uniform, and the carbide content is 30% ~ 35%. The hardness, thermal shock resistance and spalling resistance of the rolls are improved. In addition, the introduction of magnetic field during centrifugal casting and solidification can also improve the structure and properties of high-speed steel rolls. As shown in the figure, black MC carbides are evenly distributed in the matrix of each sample. With the increase of magnetic field strength, the eutectic carbides in the solidification structure gradually show discontinuous network and increase in quantity, distribution and hardness value, indicating that the magnetic field can reduce the content of residual austenite in high-speed steel, Thus, the macro hardness is increased.
The results show that the heat treatment process of bimetallic composite roll after centrifugal casting can eliminate the solute segregation and casting stress during solidification, control the amount of residual austenite, and have a direct impact on the microstructure, interface element diffusion and mechanical properties of components. By comparing and analyzing the effects of subcritical heat treatment and high temperature heat treatment on the microstructure and properties of high chromium composite roll, it is found that after high temperature austenitizing heat treatment, the residual austenite basically transforms into martensite or sorbite, and the hardness increases significantly, with an average of about 79 25HRC。 On this basis, lijucang et al. Studied the effect of different heat treatment processes on the mechanical properties of centrifugal casting high chromium cast iron composite roll. After high temperature of 950 ℃ × 1 h, medium temperature 450 ℃ × 10 h air cooling quenching +525 ℃ × After 6 h air cooling tempering, the microstructure of the composite roll is mainly martensite + dispersed carbide, and the hardness reaches 55 Above 6hrc, impact toughness reaches 5 Above 66 j/cm2, the mechanical properties of the roll are the best. Wuweiqiang et al. Used induction heat treatment to study the properties of outer layer modified high carbon cobalt free high speed steel and inner layer ductile iron roll ring. The results show that the properties of inner layer change little, but the hardness of outer layer increases significantly. The hardness of roll ring after annealing is 220HB ~ 250hb. At the same time, the bonding effect of roller ring was tested by ultrasonic flaw detection technology. It was found that the transition layer was well bonded, and the bonding interface had no defects such as delamination, slag inclusion and porosity. Due to the joint action of micro defects and tensile stress in the transition zone of the inner and outer layers of the composite roll, the composite roll tends to crack during the heat treatment process. Further research shows that the cracking of the composite roll can be prevented by reducing the heating and cooling rate of the composite roll and increasing the charging temperature after air cooling, or by adopting multi-stage tempering process and reasonably designing the shoulder shape of the roll body. In addition, for the roll sleeve with biting pattern, it is easy to oxidize the outer layer of the roll sleeve and reduce the wear resistance during the high-temperature heating stage. However, the “quenching + multiple high-temperature tempering” process of “differential temperature and no oxidation” heating can not only avoid this problem, but also reduce the amount of residual austenite, improve its biting, passivate eutectic carbides and reduce the splitting effect by rapid heating, Increasing the hardness of the outer substrate is the best heat treatment process for high chromium cast iron composite roll at present. However, it should be noted that the process has high energy consumption and long heat treatment cycle, and the effect on the composite roll with serious segregation is not obvious.
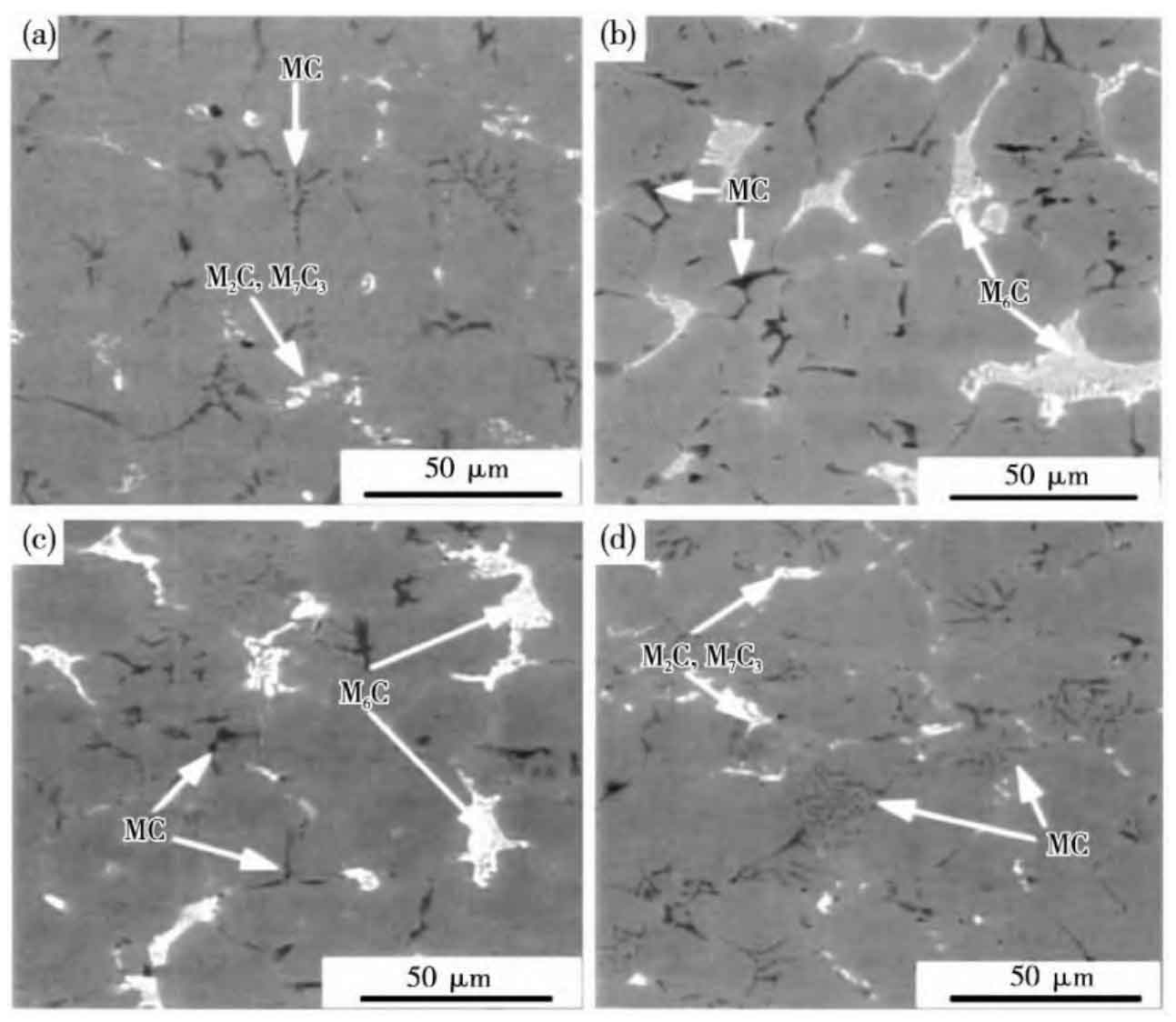
By analyzing the effects of alloy modification, differential temperature heat treatment and electromagnetic centrifugal casting on the mechanical properties of bimetal composite roll, the theory and method of improving the mechanical properties of centrifugal casting composite roll are put forward, but there are still some shortcomings. For example, high alloy steel composite roll is easy to produce alloy element segregation in centrifugal casting, which reduces the uniformity of structure and composition distribution; Defects such as shrinkage cavity, porosity and inclusion are easy to appear in the composite roll body and roll neck, which reduces the roll stability; The higher die temperature is easy to cause the formation of coarse grains, which intensifies the uneven temperature distribution of the roll. At the same time, the temperature difference between the compound roll and the surrounding environment is large, which will generate greater thermal stress and increase the probability of crack initiation; The inner and outer bonding interfaces are prone to graphite deformation and carbide segregation, which reduce the toughness and bonding strength and lead to spalling. Whether it is the combination of interface segregation and shrinkage cavity or coarse grain and crack, it will directly deteriorate the mechanical properties of the bimetallic composite roll. Therefore, in the next work, it is necessary to focus on the in-depth analysis and research of such problems.