1. Manufacturing process
All the technologies described above have different advantages. In this study, selective laser sintering technology is mainly used for investment casting of agricultural machinery engine impeller.
Firstly, the selective laser sintering system needs to receive the CAD model of the agricultural machinery engine impeller and select the corresponding format according to the actual situation. In this study, STL format is applied. In order to build a three-dimensional solid surface, a large number of triangular patches need to be used to gradually enclose the model entity to form a model that is basically equivalent to the parts in the ideal state. After receiving the solid CAD model, the system applies special slicing software to slice the model longitudinally.

In the process of slicing, the slicing plane must have a certain height, and then intersect with the model to obtain the intersection line between the model and the plane. This intersection line is the boundary of the part layer. For the closed area formed by this boundary, use the slicing software to fill it with straight line segments, and the obtained is a layer of the model, as shown in Figure 1. The distance between each line segment is the interval generated by laser scanning; The filled line segment is the scanline.
After obtaining the model layer, the wax model of a layer can be obtained by sintering the paraffin powder material at the corresponding position using the laser beam of the computer control system and taking the scanning line as the benchmark. After one layer of sintering is completed, the workbench moves downward, and the moving range is the thickness of one layer. Then repeat the above steps until the investment mold sintering is completed.
2. Precautions
2.1 Control modeling accuracy
In the process of investment casting using selective laser sintering technology, it is necessary to use STL format CAD model to build a model that approximates the ideal state. The difference between the model and the ideal state is the modeling error. Theoretically, the more triangular patches are used in the model, the smaller the modeling error is, and the higher the precision of the model is. However, too many triangular patches will reduce the efficiency of data processing, so attention should be paid to controlling the modeling accuracy.
2.2 Control scan interval and slice thickness
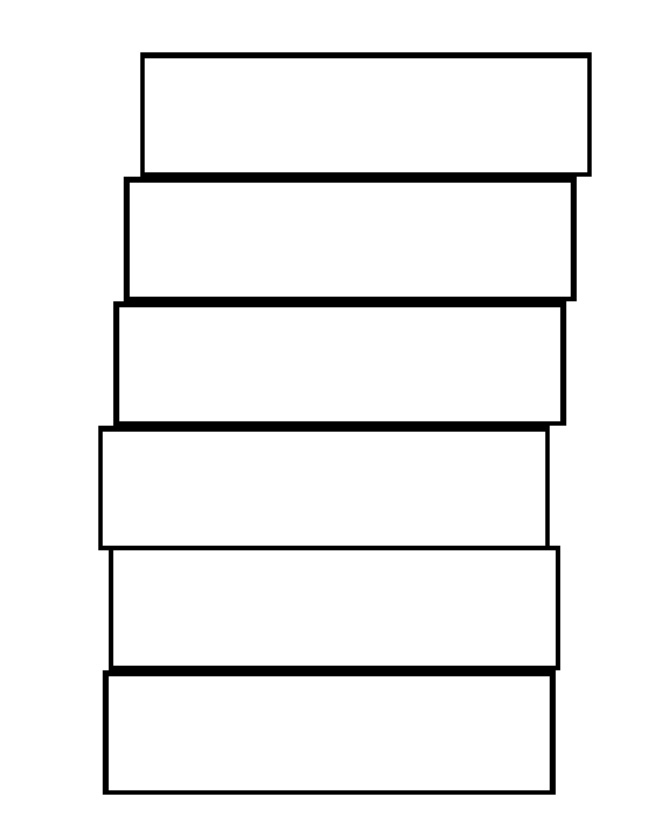
In the process of selective laser sintering technology, the surface quality and accuracy of the casting investment mold are affected by the slice thickness and scanning interval. The greater the thickness and interval, the more significant step effect will appear during manufacturing, the less ideal the shape and accuracy of the investment mold, and the poor surface quality, as shown in Figure 2. However, reducing the layer thickness will inevitably increase the number of layers. Although it can improve the accuracy and optimize the shape, the scanning interval will be reduced, the scanning times will be increased, and the production efficiency will also be affected.