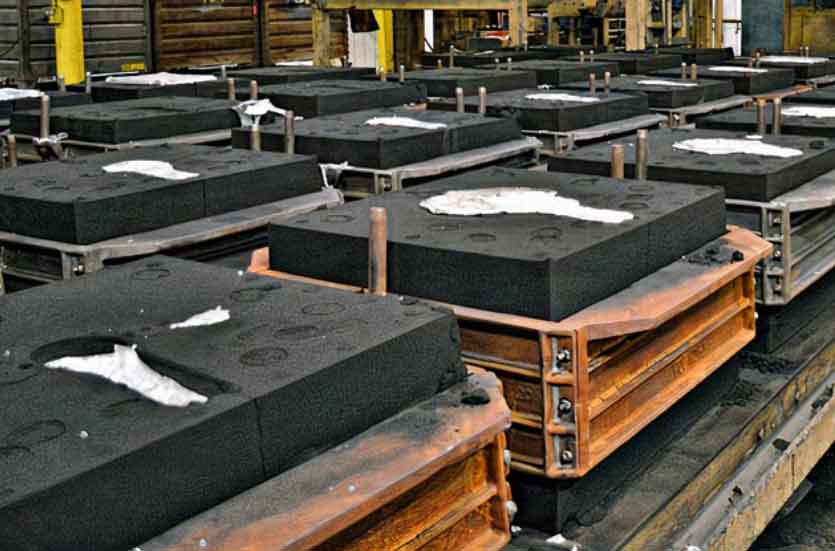
Advanced simulation in resin sand casting can significantly enhance casting accuracy by providing valuable insights into the casting process and predicting potential issues before actual production begins. By using computer simulations, manufacturers can optimize mold designs, gating systems, and process parameters to achieve more precise and reliable castings. Here’s how advanced simulation improves casting accuracy in resin sand casting:
- Mold Filling Simulation: Casting simulation software allows manufacturers to visualize the flow of molten metal during mold filling. This helps identify potential filling-related defects like misruns, cold shuts, and incomplete mold filling. By adjusting the gating and riser designs based on simulation results, manufacturers can improve mold filling and minimize defects.
- Solidification Simulation: The software can predict the solidification behavior of the molten metal, helping manufacturers identify potential shrinkage defects and hot spots. With this information, appropriate riser placement and cooling strategies can be implemented to ensure sound and defect-free castings.
- Thermal Analysis: Simulation tools provide temperature profiles during the casting process, helping to analyze and control thermal gradients. This information is crucial for preventing thermal stress-induced defects and ensuring dimensional accuracy in the final castings.
- Resin Sand Mold Behavior: Simulation models can predict the behavior of the resin sand mold during the casting process. This allows manufacturers to optimize the curing process, ensuring consistent mold properties and reducing mold-related defects.
- Virtual Prototyping: Casting simulations act as a virtual prototype, allowing manufacturers to assess multiple design iterations quickly and cost-effectively. This iterative approach helps identify the most suitable design and process parameters for achieving the desired casting accuracy.
- Material Selection: Simulation software can evaluate the impact of different materials on the casting process. This helps in selecting the most suitable material that provides the desired mechanical properties while minimizing casting defects.
- Defect Prediction and Avoidance: By simulating various scenarios, manufacturers can predict potential casting defects and their locations. Armed with this knowledge, they can implement preventive measures to avoid defects during actual production.
- Process Optimization: Casting simulations enable manufacturers to optimize the entire casting process, including mold preparation, gating and riser design, and metal pouring parameters. The optimized process leads to higher casting accuracy and reduced scrap rate.
- Reduced Prototyping Costs: By using simulations to validate casting designs, manufacturers can reduce the need for physical prototypes and avoid costly trial-and-error iterations, thus saving time and resources.
- Real-Time Monitoring: Advanced simulations can be coupled with real-time process monitoring to ensure that the actual production closely follows the simulated predictions, further improving casting accuracy and consistency.
Advanced simulation in resin sand casting offers a powerful tool for enhancing casting accuracy and quality. By providing insights into mold filling, solidification, and thermal behavior, manufacturers can optimize the entire casting process to achieve the desired dimensional accuracy, minimize defects, and produce high-quality castings efficiently.